Player FM - Internet Radio Done Right
15 subscribers
Checked 4m ago
تمت الإضافة منذ قبل four أعوام
المحتوى المقدم من Allen Hall, Rosemary Barnes, Joel Saxum & Phil Totaro, Allen Hall, Rosemary Barnes, Joel Saxum, and Phil Totaro. يتم تحميل جميع محتويات البودكاست بما في ذلك الحلقات والرسومات وأوصاف البودكاست وتقديمها مباشرة بواسطة Allen Hall, Rosemary Barnes, Joel Saxum & Phil Totaro, Allen Hall, Rosemary Barnes, Joel Saxum, and Phil Totaro أو شريك منصة البودكاست الخاص بهم. إذا كنت تعتقد أن شخصًا ما يستخدم عملك المحمي بحقوق الطبع والنشر دون إذنك، فيمكنك اتباع العملية الموضحة هنا https://ar.player.fm/legal.
Player FM - تطبيق بودكاست
انتقل إلى وضع عدم الاتصال باستخدام تطبيق Player FM !
انتقل إلى وضع عدم الاتصال باستخدام تطبيق Player FM !
المدونة الصوتية تستحق الاستماع
برعاية
B
Biscuits & Jam


1 The War and Treaty Are Getting Carried Away 46:55
46:55
التشغيل لاحقا
التشغيل لاحقا
قوائم
إعجاب
احب46:55
The War and Treaty’s Michael and Tanya Trotter grew up in Cleveland, Ohio, and Washington, DC, respectively, but both have family roots in the South. They also grew up in the musical traditions of their churches – Tanya in the Black Baptist Church and Michael in the Seventh Day Adventist Church – where they learned the power of song to move people. After becoming a father at a very young age, Michael eventually joined the armed forces and served in Iraq and Germany, where he took up songwriting as a way of dealing with his experiences there. Meanwhile Tanya embarked on a singing and acting career after a breakthrough appearance in Sister Act 2 alongside Whoopi Goldberg and Lauryn Hill. Now, after a long and sometimes traumatic journey, Michael and Tanya are married, touring, winning all sorts of awards, and set to release their fifth album together, and their fourth as The War and Treaty. Sid talks to Michael and Tanya about the new record, Plus One , as well as their collaboration with Miranda Lambert, what it was like to record at FAME studios in Muscle Shoals, and how they’re blending country, soul, gospel, and R&B. Learn more about your ad choices. Visit podcastchoices.com/adchoices…
Malloy Wind Solves Gearbox Bearing Mysteries
Manage episode 458946872 series 2912702
المحتوى المقدم من Allen Hall, Rosemary Barnes, Joel Saxum & Phil Totaro, Allen Hall, Rosemary Barnes, Joel Saxum, and Phil Totaro. يتم تحميل جميع محتويات البودكاست بما في ذلك الحلقات والرسومات وأوصاف البودكاست وتقديمها مباشرة بواسطة Allen Hall, Rosemary Barnes, Joel Saxum & Phil Totaro, Allen Hall, Rosemary Barnes, Joel Saxum, and Phil Totaro أو شريك منصة البودكاست الخاص بهم. إذا كنت تعتقد أن شخصًا ما يستخدم عملك المحمي بحقوق الطبع والنشر دون إذنك، فيمكنك اتباع العملية الموضحة هنا https://ar.player.fm/legal.
From mysterious white etching cracks to cutting-edge material innovations, Malloy Wind's expert Cory Mittleider reveals the complex world of gearbox bearing failures that plague wind turbines. Learn why traditional monitoring may not be enough and what operators need to know about the latest solutions to keep their gearboxes running reliably. Read the EPRI article Cory references: https://restservice.epri.com/publicdownload/000000003002021422/0/Product Fill out our Uptime listener survey and enter to win an Uptime mug! Sign up now for Uptime Tech News, our weekly email update on all things wind technology. This episode is sponsored by Weather Guard Lightning Tech. Learn more about Weather Guard's StrikeTape Wind Turbine LPS retrofit. Follow the show on Facebook, YouTube, Twitter, Linkedin and visit Weather Guard on the web. And subscribe to Rosemary Barnes' YouTube channel here. Have a question we can answer on the show? Email us! Pardalote Consulting - https://www.pardaloteconsulting.comWeather Guard Lightning Tech - www.weatherguardwind.comIntelstor - https://www.intelstor.com Register for Wind Energy O&M Australia! https://www.windaustralia.com Welcome to Uptime Spotlight, shining light on wind energy's brightest innovators. This is the progress powering tomorrow. Allen Hall: Welcome back to the Uptime Wind Energy Podcast Spotlight, where we tackle the technical challenges and innovations in wind energy. I'm your host, Allen Hall, joined by my co host, Joel Saxum. We're excited to welcome back one of our most popular guests, Cory Mittleider from Malloy Wind. In his previous appearance, Cory shared his expertise on main bearing failures. And many of you reached out asking for a deep dive into gearbox bearings. Today, Cory returns to do exactly that. As Malloy's business unit manager, he and his team have diagnosed and solved countless gearbox bearing issues across different turbine platforms. Having spent over 15 years in power transmission, Cory has become a specialist in understanding why these critical components fail and, more importantly, how to prevent those failures through better bearing selection and maintenance practices. Cory, welcome to the Uptime Wind Energy Podcast Spotlight. Thanks for having me again. All right, so we've got a lot of requests to hear about gearbox, bearing, and what the issues are with those bearings. Gearboxes is something I know a little bit about. But you're the expert. I hear a lot of complaining from the field. What is happening to gearbox bearings at the minute? Cory Mittleider: Sure. Gearbox bearings has been an interesting one for me. So when I started in wind in 2011, it was generator bearings and gearbox bearings is where I started learning about this stuff. A lot of the generator stuff was electrical fluting damage. That's pretty well figured out how to avoid that. The gearbox one was a little more complex than that. And I don't know if you've heard of. NREL's Drivetrain Reliability Conference that's happened for the last 12 plus years now. That's a recurring topic for the last every single year, right? Is gearbox bearing failures. A lot of the conversation that started back in the day and is still going on is around what they call white etching cracking or white etching failures. And back, in say, 11 and 12, A lot of the conversation was around was around that. It was around, the oils in the gearboxes. It was around coatings and bearing types and how they could affect the bearing itself to improve the life. And, specifically when it comes to gearbox bearings That was really hard back in the, the service providers and the operators themselves weren't used to having to replace gearbox bearings. They maybe weren't even planning on having to replace gearbox bearings, right? But they started to see these problems. They started to get their head around the scope and how to identify them early and started to dig into it.
…
continue reading
432 حلقات
Manage episode 458946872 series 2912702
المحتوى المقدم من Allen Hall, Rosemary Barnes, Joel Saxum & Phil Totaro, Allen Hall, Rosemary Barnes, Joel Saxum, and Phil Totaro. يتم تحميل جميع محتويات البودكاست بما في ذلك الحلقات والرسومات وأوصاف البودكاست وتقديمها مباشرة بواسطة Allen Hall, Rosemary Barnes, Joel Saxum & Phil Totaro, Allen Hall, Rosemary Barnes, Joel Saxum, and Phil Totaro أو شريك منصة البودكاست الخاص بهم. إذا كنت تعتقد أن شخصًا ما يستخدم عملك المحمي بحقوق الطبع والنشر دون إذنك، فيمكنك اتباع العملية الموضحة هنا https://ar.player.fm/legal.
From mysterious white etching cracks to cutting-edge material innovations, Malloy Wind's expert Cory Mittleider reveals the complex world of gearbox bearing failures that plague wind turbines. Learn why traditional monitoring may not be enough and what operators need to know about the latest solutions to keep their gearboxes running reliably. Read the EPRI article Cory references: https://restservice.epri.com/publicdownload/000000003002021422/0/Product Fill out our Uptime listener survey and enter to win an Uptime mug! Sign up now for Uptime Tech News, our weekly email update on all things wind technology. This episode is sponsored by Weather Guard Lightning Tech. Learn more about Weather Guard's StrikeTape Wind Turbine LPS retrofit. Follow the show on Facebook, YouTube, Twitter, Linkedin and visit Weather Guard on the web. And subscribe to Rosemary Barnes' YouTube channel here. Have a question we can answer on the show? Email us! Pardalote Consulting - https://www.pardaloteconsulting.comWeather Guard Lightning Tech - www.weatherguardwind.comIntelstor - https://www.intelstor.com Register for Wind Energy O&M Australia! https://www.windaustralia.com Welcome to Uptime Spotlight, shining light on wind energy's brightest innovators. This is the progress powering tomorrow. Allen Hall: Welcome back to the Uptime Wind Energy Podcast Spotlight, where we tackle the technical challenges and innovations in wind energy. I'm your host, Allen Hall, joined by my co host, Joel Saxum. We're excited to welcome back one of our most popular guests, Cory Mittleider from Malloy Wind. In his previous appearance, Cory shared his expertise on main bearing failures. And many of you reached out asking for a deep dive into gearbox bearings. Today, Cory returns to do exactly that. As Malloy's business unit manager, he and his team have diagnosed and solved countless gearbox bearing issues across different turbine platforms. Having spent over 15 years in power transmission, Cory has become a specialist in understanding why these critical components fail and, more importantly, how to prevent those failures through better bearing selection and maintenance practices. Cory, welcome to the Uptime Wind Energy Podcast Spotlight. Thanks for having me again. All right, so we've got a lot of requests to hear about gearbox, bearing, and what the issues are with those bearings. Gearboxes is something I know a little bit about. But you're the expert. I hear a lot of complaining from the field. What is happening to gearbox bearings at the minute? Cory Mittleider: Sure. Gearbox bearings has been an interesting one for me. So when I started in wind in 2011, it was generator bearings and gearbox bearings is where I started learning about this stuff. A lot of the generator stuff was electrical fluting damage. That's pretty well figured out how to avoid that. The gearbox one was a little more complex than that. And I don't know if you've heard of. NREL's Drivetrain Reliability Conference that's happened for the last 12 plus years now. That's a recurring topic for the last every single year, right? Is gearbox bearing failures. A lot of the conversation that started back in the day and is still going on is around what they call white etching cracking or white etching failures. And back, in say, 11 and 12, A lot of the conversation was around was around that. It was around, the oils in the gearboxes. It was around coatings and bearing types and how they could affect the bearing itself to improve the life. And, specifically when it comes to gearbox bearings That was really hard back in the, the service providers and the operators themselves weren't used to having to replace gearbox bearings. They maybe weren't even planning on having to replace gearbox bearings, right? But they started to see these problems. They started to get their head around the scope and how to identify them early and started to dig into it.
…
continue reading
432 حلقات
كل الحلقات
×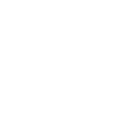
1 Hitachi Energy Leads the Energy Transition 33:58
33:58
التشغيل لاحقا
التشغيل لاحقا
قوائم
إعجاب
احب33:58
Laura Fleming and Alfredo Parres from Hitachi Energy dive into the critical challenges of integrating renewable energy, particularly offshore wind power, into the UK grid. They explore innovative solutions, including HVDC technology and digital advancements, that are driving efficient, reliable energy distribution and shaping the future of the global energy landscape. With Laura’s over 25 years of experience in the energy sector and Alfredo’s long history in renewables, the two give insights into how Hitachi is making the energy transition possible. Fill out our Uptime listener survey and enter to win an Uptime mug! Sign up now for Uptime Tech News , our weekly email update on all things wind technology. This episode is sponsored by Weather Guard Lightning Tech . Learn more about Weather Guard’s StrikeTape Wind Turbine LPS retrofit. Follow the show on Facebook , YouTube , Twitter , Linkedin and visit Weather Guard on the web . And subscribe to Rosemary Barnes’ YouTube channel here . Have a question we can answer on the show? Email us! Allen Hall: With power grids adapting to accommodate growing renewable energy, the challenges of integration had never been more critical. This week, we speak with Alfredo Parres group, senior Vice President and head of Renewables at Hitachi Energy. And Laura Fleming, country managing director at Hitachi Energy UK and Ireland. Together, they explain how Hitachi’s technology is enabling efficient, reliable connections between massive wind farms and our existing electrical infrastructure. This is a great interview. Stay tuned. Welcome to Uptime Spotlight, shining Light on Wind Energy’s brightest innovators. This is the progress. Powering tomorrow. Allen Hall: Laura and Alfredo, welcome to the podcast. Laura Flemming: Glad to be here. Alfredo Parres: Hey, huh. Allen Hall: How are you? Laura, let’s start with you because I’ve watched a number of your interviews on YouTube and there’s just a lot happening within Hitachi. What are some of the main challenges in the UK facing sort of the renewable energy grid and all of the particularly wind power, which is what we’re focused on. There’s a lot of wind power offshore being deployed in the UK at the minute. How is a Hitachi trying to handle that and distribute that energy? Laura Flemming: Yeah. Thank you for the question. And uh, it’s a super exciting time, as you’re saying in in the uk energy space. And maybe just to explain briefly what is going on the UK. At the moment, it’s very hard at work to decarbonize the electricity grid. It’s actually planning to be fully carbon zero by 2030. That’s only in five years time now. And that’s obviously a very big job. What we’re doing in order to reach that as a country is switching away from from carbon sources. And so about six weeks ago. We switched off our last coal-fired power station, for example. But of course we still need energy and we still need a lot of electricity. So what we’re doing instead is building out a lot of renewable energy predominantly offshore wind because that allows us to produce vast amounts of electricity quickly cheaply and sustainably. The result of all of that is that actually we’re producing electricity in very different places than that we used to. So offshore wind, obviously produced in the sea, mainly in the north of Scotland particularly in Scotland. But the demand centers are all in the s of the country, predominantly around London and Birmingham areas. So we needing to transport this electricity around the system in a very different way. And all of that is triggering lots of grid reinforcements requiring to be done as well. So, and obviously without that grid, we can’t move around this this new electricity from the generation source to the to the demand centers in a very efficient and also in a reliable way. And also making sure that we don’t have too many losses on the system. So this is a huge task. The role that Hitachi energy in is playing in all of this is to ensure that a large number of these offshore wind projects can be connected to the UK grid. We are also supporting the transmission owners to help build out the grid, to make it more flexible, more reliable, and more efficient. And then we’re also supporting, for example, onshore and solar generators connecting their projects in via, via substations, et cetera. Allen Hall: Alfredo, what happens if the, this interconnection doesn’t happen to the UK economy and more? Wider impacts in terms of Europe. It does seem Laura has mentioned a lot of the energy sources are coming from remote places, but the power is being used in kind of the big places. Paris, London in Germany, there’s just big power usage areas. If we don’t connect them, what’s the outcome of that? Alfredo Parres: Yeah. I think it’s fair to say that it’s difficult to think about an energy transition without grids. Grids, electricity is about to be everything as we move on. And we need a lot of those. And grids that’s in many places are also oldish. Depending where you are on the world can have assets where that are pretty old. So we need to pay attention to that. The good news on this, a Noel, as I like to say, is that I see that. The conversation on grid has evolved drastically, compared to a to previous years. I see the conversation as has already evolved a lot, typically in my early days in, in this business it’s a few years. We had to educate people, educate governments on the importance of grids, anticipating what was coming, or it was a lot of education to be done. These days, you go to any conference, any civil servant speaks about grids as well as I do. So that means they, they are aware, they’ve educated themselves, they know what they’re talking about. And they the connections, I think in Europe, if you think about the grid action plan that the commission has put together is looking at implementing. I think that speaks what I’m mentioning here, the plans are there and the options to do things are huge. From increasing capacity or improving the usage of the existing grids. That’s the first step we can do. Technologies are there to do that, building new grids and planning the development of new grids. There are things that are doing, so in a nutshell, Alan, and we can go in further details in the conversation, there is no energy transition without greats good news or politicians or governments. Got it. We start putting the real Joel Saxum: actions required, I think to speak on this problem here with grids and integration with renewables. Again, for the energy transitions. Someone once said there’ll be no transition without transmission. I like that statement. But to speak on that issue more when these, when the grid that we’re, that we’ve lived with for, a long time it was originally developed. Most of that was with this consistent power delivery to it, right? It was coal fired power plants and other sources where it was consistent. And now when we add renewables to the mix, and they are by nature, intermittent, whether it’s solar or wind or however and people are trying to control that now as we move forward with battery storage and things. It complicates that grid question as well because now we’re saying, Hey, we need to upgrade the grid, but we also need to upgrade and future proof the grid, and I think that’s a very important statement there as well. And Hitachi, that’s what you guys are doing. You’ve got loads of people working on these problems to solve this intermittent delivery issues. And that’s hand in hand with the contemporary term, I guess is the smart grid. So Alfredo, I’d like to ask you this question. At what point in time did you start to see, the stakeholders that can make some of these decisions around the grid start to open their eyes to the difference that we need to future proof this? The energy mix looks different, and if we don’t fix this, we’re gonna really run into issues Alfredo Parres: beside grids. We are spending a lot of time to tell exactly about that. It’s not just the grid, it’s the complexity of the power system we are developing. We are going to manage intermittent source of generation. Different side of science type of generation based on power electronics, which basically says it’s a generation profile that is much more volatile with less inertia. We will have to manage all those elements in a harmonious way because we want to keep a sustainable power system at power safe and save power system. So the education is happening and we see the message getting there. As I said, you think from a planning perspective and everything start with planning. There’s no point to try to solve it if you don’t have a visibility 5, 10, 15, 20 years ahead to see what are we going to need? What are the investments we going to need? What is infras going to need? And that is happening. We still, of course, need to always to improve, and that’s what we’re talking right now with the authorities, know how we can improve the planning piece on the technology side, we tell them technology exists to manage this complexity we’re going to face. Intermittency is not the end of the world. It should not stop penetration of renewables. We can bring much more into the system and technologies are there to help us for electronics. These things we use for batteries management to use fax, all those system, I have to stabilize grids to be the HVDC connections. Essential to keep the stability, to keep this flow of energy oriented in different directions. Digital, absolutely key. Also because digital will help us to manage this complexity we’re facing. From a demand perspective, from a generation perspective, to operate, to maintain, the digital piece absolutely key. And that’s a not so easy story to get through because digital, not everybody understand what it means. For real. We are Hitachi, we make it as a party for us, no to tell how digital is real and can help us to to address our challenges. No. Allen Hall: Laura, I want to use the Eastern GreenLake two as our test case here to walk through some of the things Hitachi is doing. So the Eastern GreenLake two is A-H-V-D-C project, two gigawatts that is being transmitted from Northern Scotland down to England offshore, and the this distance is 440 kilometers, which in America terms is about 250 plus miles. That’s a long way for an HVE DC cable. The complexities of that project have to be enormous. How does Hitachi fit into that infrastructure project? Laura Flemming: Yeah, it’s a really good question. And the exactly as you say, the Eastern Greenland project is a is massive in terms of scale. But it’s also groundbreaking in terms of what it’s trying to do. It it will be collecting the power from a number of offshore wind farms and renewable generation capacity from the north of Scotland collected at this this, really large substation that’s going to be built in in the north of Scotland, as you say. And then to be transporting that power to the somewhere in the middle of England. Via an offshore connection. So rather than transporting that power via, multiple pylons and multiple cables that going onshore overground as we would’ve done in the maybe in the good old days. All of this power is being transported offshore. And that has a number, a number of advantages. In terms of connection with the communities in terms of environmental impact in terms of, being able to cross communities, et cetera. But it also has an added benefit because actually using A three DC over a large distance also means that, the energy losses will be significantly reduced. So what is it that Hitachi Energy is doing? We’re providing both the on and offshore substations that’s basically can, making the connection. So we don’t do the cables, but we do, we effectively provide the plug, right? That allows this energy to be collected and to be put into the cables. And then to be taken out of the cables and then put into the grid so it can actually be usefully used. And what that’s actually allowing, the UK electricity system operator to do is manage the power flows around the country. So really providing that security and that stabilization delivering power as and when they need it but also as and when it is being produced and really optimizing. What we’re producing as a country. And as you say, also that helps us manage the the renewable resource, which is sometimes, is it is intermittent. So there’s a lot more work around digitalization power electronics going on in the background to to manage those flows. At any given time of the day, we can still keep the lights on. Allen Hall: I want to dig into that a little bit because we use HV dc you just throw on that term. It’s we just use HVDC, but that is really complicated. The power electronics that are going into these devices are revolutionary. To do something at a high voltage DC wise in the electronics to make that happen are truly incredible. And to do it bidirectionally, you can move power around as needed because of the renewable energy factor where sometimes as the wind’s not blowing, sometimes it’s not as sunny out. You need to redirect where energy is flowing. H Feed DC gives you that. But how much infrastructure on the Hitachi side is. Dedicated to HVDC and the software and all the control systems to create this grid. Alfredo Parres: So we just celebrated 75 years of anniversary for the technology. We started back in the early fifties. So that tells is a young, old technology we are talking about here, the last version or the last technology we’re using. The VSC variable source converter version of it is a bit younger. No, but this is a technology that has been proving by the years benefits. No you mentioned it, long distance transmission, bidirectional flow, but there are a lot of orders benefits, no, not the least, the low losses. No. We use it because we reduce drastically the losses of our lung transmission. Plus the support we can give to the grid to which the HBC link is connected. So actually this link is supporting the stability of the grid. And in these days with the high penetration renewables, that’s extremely important just to tell. The benefits are absolutely phenomenal. And it’s true that with the emergence and the boom on around offshore wind, the technologies is facing fantastic times. And for us it’s really where we are putting a lot of our investments, a lot of our people we’re talking about, of thousands of people are being hired to support this business. Among the six billions we are investing these days, a lot is going in manufacturing of new valve new valve manufacturings, hiring new engineers to go in all different centers. And in Sweden, ru where we have, the capital, the place where the technology was born. Are we talking about the middle of Sweden in a very nice natural place, but not necessarily the place you would go for to in business, having hundreds of people going there, finding the, finding themselves comfortable with a clean mission, which is to accelerate this energy, trans transition and working with, for leading company, they got education. They work in a diverse environment because of course we got people coming from all over the world. They find themselves and they can law. So really I think HVDC is leaving extraordinary times. We see that all suppliers knowing this technology investing. So we are not the only ones, which is good also because that’s, the demand is huge. We need. Everybody to contribute, and we need then society to understand the benefits now of the technology. Joel Saxum: So HVDC in my mind, I think would it’s going to be as the grid gets newer, fresher, more innovative, and we start putting some money into it. You’re starting to see some of that here in the states. Couple saw a couple of reports in the last week of some big money rolling into it. HVDC to me should start to be a much broader part of that energy grid as you guys are focusing a lot of effort into it with employees and investment. How mu, how much of a percentage growth do you think, and I know that’s a pointed question, do you see an HVDC versus in the past? Laura Flemming: If I can maybe comment on in terms of the growth that we see in the uk, we’re seeing the UK really moving for maybe doing. One HVDC project that, as a country, right? Not necessarily as Hitachi Energy by themselves, but as a country we’re really moving from doing one of these projects a year to doing, multiple, like three or four, maybe even more projects a year. So the growth is, not just huge, it’s exponential. And as Alfredo was saying earlier, that’s really why we’re, we’re resourcing up, we’re hiring, thousands of people. To be able to work on HVDC solutions around the world. And because it’s not just the manufacturing of the converters and all of the other equipments that goes onto the, into the platforms and into the substations. There’s a huge amount of engineering, of front end engineering that and design that needs to be done. Before you can start building such a project and really planning all of that in, in a strategic way into the overall grid is really crucial. And I think this is really the interesting thing that we’re seeing in the UK where we’ve really, moved from a connect and manage sort of approach. So we’ll connect it when there is a need for it, and we know we have everything ready. To, know, let’s actually plan for, let’s plan for the future and we’re going to see what we need in the future, and we’re going to get ready and build that because we know that the generation and the demand will be coming. And that’s when solutions such as HVDC become really critical. And it also depends on distance, right? So the distance is really a big element in HVDC. So anything. Over 120, 30 miles away. Is really going to be beneficial to use HVDC Allen Hall: and Hitachi touches. Almost everyone’s lives in Europe and the United States. You may not realize that, but Hitachi’s big on H-V-A-C-H-V-D-C and on the monitoring and support side they’re involved everywhere. And maybe touch upon Alfredo what. Hitachi is doing after the sale, after the grid’s been installed. There’s a lot of monitoring, support and software that goes on after the grid has been connected, right? Absolutely. Alfredo Parres: And welcome to, to, to this new world know, and I mentioned it before, know, which is digital, I mean with our new owners, as I guess more many people know by, by now. As a former a PB now owned by Hitachi. We have new owners that believe deeply in, in the role of digital and they invest heavily as a business itself. And we are enjoying the benefits of being part of this larger corporation and developing the, those solutions of the future based on the core knowledge we do have. ’cause at the end, what makes a difference in digital is the understanding of the product and the process and the technology, which we master in Hitachi. And you put a layer of digital on top of that. Which is the embedded digital solution we have in product solutions plus the layers of digital. You have to control and operate all those assets. Bingo. Then you start having comprehensive solutions that bring value to customers. No, and that’s where we are heading for the train has left the station ready for a while now. We are not so starting now but the journey is still long to go until we reach full benefits. And Forest Service is going to be a huge focus area because we are sitting not only on a huge install base, you think about what a hundred years working on, on, on the market with millions of equipments out there that we can serve and we to serve more of them, but the requirements really come higher as the system will become more complex, more fragile. So we need to be able to react quickly. But also we have to react to the environment, conditions that we are facing. Going to tell about all the climate incidents that we’re facing. That’s part also of operating an asset. No. And here too, a digital play, a big role or to not only anticipate forecasting evidence that can happen. Get prepared with your plans. Get prepared with your actions to add quickly. Definitely for us is a critical area. Allen Hall: Can we discuss the order book for Hitachi at a top level A little bit? How busy is Hitachi right now on orders and my guess is that your phone is ringing all the time. People trying to get orders in for HVDC, even HVAC at the minute. How busy are you? Laura Flemming: Yeah, now I can comment from a UK and Ireland perspective, so no, we’re very busy. And obviously that is wonderful. What’s really important for us is to ensure how do we bring the best of what Hitachi energy has got offer to our customers? And therefore we have changed slightly the approach in which we are working with customers really working in programs. And frameworks and again, in in a systematic and strategic way. And that is a number of benefits. Yes, it allows us to understand, what work is coming. And that is really important for us, for our production planning, for making the investments that we talked about earlier. And also for hiring people because the biggest. Obstacle that we have in in this energy transition is actually people we need. We need to train, we need to hire, we need to manage a vast amount of new people coming into the industry, not just in Hitachi energy, but into the industry. So we’re really facing facing quite an uphill battle there. And so yeah, having that visibility requires us to, and allows us to plan in advance, there’s another very important aspect to all of this as well is that when we know what our customers are looking to do over the next few years or so, we can start working and engaging with them at a much earlier stage in their project. That will allow us to help them standardize some of the solutions and that standardization will allow us to speed up, it’ll allow us to work more safely. It will allow us to, move from site to site knowing the issues that can appear on sites and actually be able to anticipate on the, on those in advance. So yeah, that early engagement and a strategic approach to, to the order book, as you were saying earlier is super critical for us, but also ultimately for the customer and for the overall, for the greater good. Allen Hall: Let’s talk about that variations that you see on orders and everybody when you hear about the power grid, a lot of operators, owners want a very specific set of parameters. They don’t want to order a generic piece of equipment, but that’s a huge problem for the grid and for the manufacturing and planning. Are you starting to see a little more standardization as. The demand goes up that maybe I can use a slightly better HVD system that’s standardized for my project instead of having a tailored one for my specific needs. Alfredo Parres: I think it’s a moving reality. And, and we cannot say we are there. Of course, we cannot say we are there, but we mentioned this always on the different ways. No, now I refer to the first one. Or if you have a frame agreement, if you work on a portfolio of project. Here we go. That’s what we got. That’s what we did with the transmission system operator tenant in Germany where they came out with a large number of HVDC connection, 12 in one shot, and they went to markets. We got half of them, 13 billion contracts, 3 billion US dollar contract with that. You can imagine with that in, in ahead of us, ahead of you to be delivered the next. Five to six years, there is an opportunity to go project by project, get lessons learned, standardize improve efficiency, and that’s what’s the opportunity we are in front of us and customer get it. Of course, they’ll still like to specify. And that’s the second message we are giving. No, we talk about standardization. We should not think about having equipment out of the shelf. No, I don’t think we get there, and we should be dreaming of that. It’s more strategizing the requirements and then the manufacturers will put all their innovation, their creativity, to make those equipment as standard, as reputable as possible. We had to start with the requirements. No, as you said, the transmission system operators, the utility companies, if they could standardize their requirements as much as possible, that will help the supply chain big time. Not only Hitachi energy, the whole supply chain. Allen Hall: Yeah. If we wanna build the grid quickly, we need to have some level of standardization. The number of varieties of transformers that exist in the world is in the thousands. The tens of thousands at the moment, which is a little crazy because we’re just moving power from A to B. We can have some standardization. I and Hitachi being a huge company worldwide, global company, country to country, that changes also. So you’re getting to different types of requirements in different countries. If we’re going to go fast, we have to standardize at least a little bit and have maybe have a little more flexibility, which I think is afraid of what your point is. Come in with a spec sheet, but have a little bit of movement in it so we can deliver you the products faster. Because the grid buildout is important right now, right? We say we need to Alfredo Parres: go at speed and scale. That’s the name of the game, and that’s standardization. It’s innovation technology, but also innovation business models. Laura Flemming: Standardization doesn’t mean, it is off the shelf and it’s, I am, 100% identical. So much time is being used up because every time you start with a blank sheet and start, designing and engineering from the ground up, what if we could start at 70 or 80% and then, specify and and personalize that last 20. That saves saves so much time, but also removes the the the room for error redesign, et cetera, et cetera. And as of, as Alfredo was saying, that’s really gonna speed us up Joel Saxum: and I want to touch on that too, because of. Big part of what you guys do, and Alan had said this earlier, even if you don’t really realize it, Hitachi is touching your life somewhere, right When you flip the lights on at some point in time, Laura and Alfredo had something to do with that. But what I wanna say is that with all of the innovation and the work that you guys are doing, and we’re talking about kind of economies of scale and standardization and getting things done more efficiently. What kind of impact do you think that Hitachi’s work has on the public perception of renewables? Alfredo Parres: First of all, I want to say we like to be humbled also. We are a large corporation. We do a lot of things. We are a successful company, but we are only one part of the whole value chain. And it’s true that the big weight is carried by the investors or the ones who have to build the projects. The trust the utility companies will have to build those lines. So our contribution to that is, is very much in providing the education, explaining what we do, explaining the benefits of the technologies, or sometimes also to make sure we don’t get misleaded in some wrong concepts, nor what could be the impact on people of high voltage transmission lines to say something, so we can tell things in a simple way. We like to do it, but we are only what we are. No, we are a technology companies. And we have to support all of us, those who are taking the major risk to to define, to provide investments to to talk to to, to people, to talk to civil servants, to talk to local populations, to say what’s, what are the benefits of those technologies? Laura Flemming: I think what Hitachi Energy is doing is, really showing also how all of the different pieces, come together. A lot of our technology and equipment, it’s usually a little bit hidden, right? The in terms of renewable energy, the attention goes to the the, the lovely shiny turbines and the things, and the things that we see. But they are also usually the ones that attract, a lot of the negative attention. And I think by showing how renewable energy. Can be integrated into the grid successfully. How we make sure that where the turbines are turning, that we don’t throw any of that energy away. Because we’re now optimizing, we can be more flexible and actually we can provide energy security because, at the end of the day, this has been one of the big drivers. Particularly so since we saw the impacts after, COVID and in Europe, particularly the the war in Ukraine, how easily, we can really be caught on the back foot in, in terms of our energy supply. So providing that energy security is absolutely critical because, let’s be honest, as we go on and on as a country and as a population, we’ll be needing more energy as we go forward. So bringing the public along is super important. I don’t think as an industry we’re doing enough yet. But I’m really pleased that since the summer, IT energy is now actually one of the key five key requirements and action plans in the UK in terms of what the government is driving forward. So having that specific focus. On energy, the same as education, the same as health is is a massive game changer. And I think what that oil will also do is make a lot more people interested to come and work in the energy industry going forward, which is exactly what we need. Allen Hall: So what does the energy future look like with Hitachi? What should we be looking for in the next year or two? Laura Flemming: I think we’ll be building a lot of projects. I will be, think we’ll be supporting a lot of customers. And I also think you’ll be seeing a lot of innovation in terms of how we speed up, how we do things more quickly and flexibly. But also how the grid is actually going to look like, once we’re actually building up to the capacity that we need. How is digitization really going to help us, accurately create the flows through the electricity system? And making sure that at any given time, the lights will stay on. Allen Hall: Lauren Alfredo, this has been a terrific discussion. I’ve learned a tremendous amount. I think the world needs to know more about Hitachi energy and what you’re doing to make the grid more reliable. I. And larger. And Laura, how do people get ahold of Hitachi Energy? How do they find out more about the great things that Hitachi is doing? Laura Flemming: Thank you very much. It was indeed a very interesting conversation. So thank you for inviting us. And for anyone who would like to find out more about Hitachi Energy please follow us. Via the usual channels or find us on Hitachi energy.com. Allen Hall: Laura and Alfredo, thank you so much for being on the podcast. Really enjoy speaking with you today. Laura Flemming: Thank you. Thank you.…
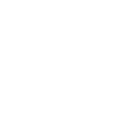
1 How Low Cost CMS Stops Catastrophic Damage 28:26
28:26
التشغيل لاحقا
التشغيل لاحقا
قوائم
إعجاب
احب28:26
We discuss how using continuous monitoring systems (CMS) can prevent catastrophic blade damage from transportation and lightning. We also share insights from GE Vernova CEO Scott Strazik on potential industry growth. And TPI Composites has hit the milestone of manufacturing their 100,000th blade. Fill out our Uptime listener survey and enter to win an Uptime mug! Sign up now for Uptime Tech News , our weekly email update on all things wind technology. This episode is sponsored by Weather Guard Lightning Tech . Learn more about Weather Guard’s StrikeTape Wind Turbine LPS retrofit. Follow the show on Facebook , YouTube , Twitter , Linkedin and visit Weather Guard on the web . And subscribe to Rosemary Barnes’ YouTube channel here . Have a question we can answer on the show? Email us! Allen Hall: On this week’s Uptime Wind Energy Podcast, we discuss how continuous monitoring systems could prevent catastrophic blade damage due to transportation issues and lightning strikes. And that’s a good discussion. GE Renova, CEO Scott Straza sees a soft entree wind market through early 2025, highlighting potential growth in Repowering projects. TPI composites manufactures their 100,000th blade. Congratulations. And our wind farm of the week is the Jericho Rise Wind Farm in upstate New York. You’re listening to the Uptime Wind Energy Podcast brought to you by bill turbines.com. Learn, train, and be a part of the Clean Energy Revolution. Visit build turbines.com today. Now here’s your hosts, Allen Hall, Joel Saxum, Phil Totaro, and Rosemary Barnes. Allen Hall: in his first appearance at Barclays Conference. Since GE Vernova’s spinoff, CEO Scott Strazik offered a sobering assessment of their wind business while highlighting some positive developments. Now, Strazik, uh, described the onshore wind market. Is currently very soft, quote unquote, with weak order expectations for the first half of 2025, though he noted opportunities in Repowering projects and certain international markets that could, uh, at least partially offset North American weakness. Now, one of the things that was mentioned during the Scott Straza, um, conference or discussion was that they are doing internal inspections and a lot of them using crawlers, which I, I believe is are from Aeros, where they’re looking at. Uh, the blades at the factory internally after transportation, and then once they’re up on tower trying to capture any defects that are happening. And this, at, at, when I saw this, I thought, oh, it goes back to Phil’s comment that a lot of damage is actually happening during transportation. And that there maybe they’re trying to, uh, work on that transportation piece or at least be able to make some claims that their blades have been damaged during transportation. That’s a unique piece ’cause I don’t know any other. OEM that is doing that many inspections at the moment. Joel, do you know any of Joel Saxum: others that are doing that? I know they should be. Uh, but, but, uh, yeah, same page. I don’t know anybody that actually is. I think it’s a, a bit of a. It’s good market response, to be honest with you, from my opinion, because I mean, you know, we’ve, we’ve seen so many blades that are brand new or within warranty having issues. Well now you can trace them back. If you get that inspection done at the factory, you put in a, uh, basically a, a. Data point of traceability. If it was good then and it got to site and then all of a sudden there’s a damage, well that happened during transportation and handling. So you can start to say, that was your fault. This is who should pay for this. These are the things that are being traced. Right. Um, and we did see in a presentation, uh, just yesterday or two days ago from Arons that they were putting statistics to the findings of their internal crawlers. And one of them was rad at like that. 70% from root to tip mark where that handling happens. There was a spike in damages that they’re finding. And it was mostly all related to handling, so I don’t know of any others. I know it’s actually kind of hard to get anybody as, even as an operator, get any of these OEMs or blade manufacturers to agree to get inspections done of the factory. Allen Hall: Joel, do you think that some of the damage is caused by the cradles or the saddles that are used during transport, or is it more about just the roughness of the roads and the, the trucks that are used to move the Joel Saxum: blades around? Well, it’s ha, it’s handling. Uh, for the most part because if you can eliminate how many times you have to handle anything, you can avoid damages. This is why offshore wind farms have a, a problem as well, because if you’re going to move, even if the factory is key, the factory’s close to keyside for those blades, you still have to get them out of the factory, into the lay down yard to the key, and then craned onto the vessel, and then crane, you know, moved on the vessel and then craned off the vessel. And if you’re in that Jones Act situation, like we are here in this. States, you’ve got to move them twice offshore. That’s just not good, right? Uh, you don’t want to be, you want to handle these things as minimal amounts as possible, because at the end of the day, they’re fragile. How many blades Allen have we seen where like the trailing edge has like a little. Crunch in it, you know, a lot too, way too many. Allen Hall: Rosemary. Is there a lot of structural reinforcement that happens on these longer blades for the lifting points and the transportation points? Rosemary Barnes: No, they don’t. Uh, I, I mean they definitely, um, consider that, uh, as a potential failure mode, but they’re not. Necessarily trying to reinforce a blade as they are trying to make the cradle so that it won’t damage the blade and put it in a location where there is some, um, reinforcement there. I’m not a hundred percent sure that it’s like purely one way direction. They might, you know, know where the cradles roughly have to go and make sure that there is, you know, like a bulkhead or something there that can, um, stiffen, stiffen up that area a bit locally. But they’re definitely, they definitely don’t want, you know, a bunch of extra weight added purely for the. Point of transportation, because then it’s up there on the turbine weighing more than it needs to for 20, 30 years. And that affects every, every other component. The, you know, bearings, the. Um, drive, train the tower. The foundations all need to be beefed up a little bit extra because of the extra weight. Allen Hall: Phil, what is the cost to the industry due to transportation damage? I think that number’s big. Phil Totaro: Yeah. It’s, it’s in the millions and we’ve actually been rerunning our calculations, um, recently. So, um, blade transportation damage is actually now number three. Um, lightning damage to blades has actually overtaken it as being the number one issue. Um, which may or may not be a good thing, I guess, depending on what area of the business you’re in. Certainly if you’re selling people lightning protection technology, uh, maybe that’s good. Um, but, uh, blade root cracking, uh, is also now a big issue. But all three of those, so. Lightning damage, blade root cracking and transportation damage are like your top three, uh, issues. And it’s all well into the hundreds of millions of dollars a year, uh, in annual, um, operations and maintenance expenditure just for the US market alone. Unfortunately, we don’t have data on, um, the faults and failure rates in other countries yet. Um, but based on recent conversations, uh, with my new friends in Australia that. Uh, it looks like we may get some data. Allen Hall: Alright, so after the break, I want to highlight what Phil was discussing here about the hundreds of millions of dollars in transportation expenses do to damage and what we’re doing about it or what we can do about it. Don’t let blade damage catch you off Guard the logics. Ping sensors detect issues before they become expensive, time consuming problems. From ice buildup and lightning strikes to pitch misalignment in internal blade cracks. OGs Ping has you covered The cutting edge sensors are easy to install, giving you the power to stop damage before it’s too late. Visit eLog ping.com and take control of your turbine’s health today. Okay, Phil. If there’s so much damage happening from transportation and lightning, by the way, it does seem like CMS should be used to detect it. Now it looks like GE is actually gonna use the internal rovers from Aeros to inspect them, but are there any CMS systems on a. Truck or on the cradle when blades are being transported at the minute? Phil Totaro: No. No way. That’s that’s way more sophisticated than this industry would ever employ. And way more expensive than anything we would ever choose to do if we can’t even get people to put CMS systems on turbines. Um, you know, even 4, 5, 6 megawatt turbines, then we’re not gonna have, you know, any kind of, uh, fault and failure detection on the, the transportation systems themselves. Not to say that that wouldn’t probably catch certain issues and, you know, you can certainly put like strain gauges and accelerometers on the truck, uh, or on a cradle. Um, and some people may in rare occasions use things like that. Um, but it’s not standard Joel Saxum: for sure. Yeah, Phil, I was gonna mention that. Not standard as well, right? So in Hamburg, two years ago, I ran into a company that was doing just this. They had a sensor that was about the size of a cell phone, and it’s really basic sensor, to be honest with you. It’s just GPS communications, a battery, and then an accelerometer and a gyro inside of it. And they were, it’s the same kind of stuff that’s used to track fleet vehicles, right? Like, oh, this is this vehicle, this is, so, you can see where it is if they hit the brakes hard, these kind of things. But they were wanting to put them, that was their goal. We’re gonna put ’em on turbine blades from the factory. So locationally geographically, we can track them, uh, wherever they go. And then also if they hit a bump hard, if they do something, if they get dropped or whatever, you can see the different G-forces on the blades themselves. But. You know, when I was speaking with him, I was like, that’s cool. I said, probably the locational part, because at the, to be honest with you, you’d have to put a half a dozen of these things on different parts of the blade to start to see if the root bending moments moved a bunch or something of that sort. And at the end of the day, you’re not gonna get, like, blades don’t show up cracked in half, you know what I mean? Mostly it’s lifting damage or something like that. So the accelerometer thing, I don’t know if that’s really a valid, but people have tried to do it. It just has never, could, never caught on. Allen Hall: Okay, Rosemary, when a CMS system should be installed, there must be some sort of criteria here, and I want, I want to get your thoughts about this because there is a lot of discussions about CMS and monitoring of blades and monitoring of gear boxes, and there’s a spec gonna come out in the next, I don’t know, it’s a couple of weeks, I suppose, and. There is so much discussion about it, but I want to hear some sane thoughts about when you should use a CMS system. Rosemary Barnes: You know what? I think that it’s got a lot to do with, um, the amount of. Um, spare time that your operators have on their hands, people that working in operations and maintenance and, um, all of those sort of, you know, like afterwards things, um, they’re so pressed for time. They do not have enough time to do all of the things that they already know they have to do. They kind of don’t want to know about additional things. And so when you say how much should you have, they should have that CMS because it will ultimately make their job smaller. Right? That, um. You that that will instead of. Having to replace, you know, some gearbox component or some bearings that means, you know, like a shutdown of a turbine for a long time and all of a sudden an emergency to, you know, get this fixed quickly. Instead of that, they would be able to, you know, monitor across the fleet. They would know, okay, we’ve got a few that are coming up and we’ll need to be replaced soon, so we’ll make a campaign and we’ll get them all together. But, um, yeah, so that’s, that’s what should be happening. The industry would work much smoother, but I know that the reality of it is that people are too pressed to start thinking about stuff like that. Allen Hall: Phil, what are the top four or five money losers? On turbines at the minute? Phil Totaro: Uh, well, generally blades, I mean, I can’t, you know, again, I can’t really categorize everything, um, specifically ’cause we don’t have enough information about all the faults and failure modes, but blades number one, uh, gear boxes, particularly bearings and anything having to do with kind of the drivetrain overall, uh, main shaft, et cetera. So that’s all kinda lumped in there. Um. Jaw bearing and pitch bearing. Those are, those are kind of your top three or four. Allen Hall: Okay. Let’s look. Let’s look at sources of problems. It was lightning’s number one, right? In terms of sources of problems Phil Totaro: for Allen Hall: blades? Yes. Phil Totaro: And for tower. And for tower collapses, potentially, yes. I mean, Allen Hall: right tower collapses. Catastrophic lightning has gotta be close to the top. The insurance companies will tell you that. Phil Totaro: Uh, yeah. Again, I don’t have the data to say that if an insurance company will tell you that, then I’ll believe it because that seems logical that, you know, I mean, how a blade is even able to strike the tower to kind of knock it down is if the blade’s got some kind of damage and there’s a load imbalance, um, it’s hard to just get a load imbalance from some other. You know, like you’re not gonna get a load imbalance from leading edge erosion, let’s put it that way. I mean, you’d have to have ridiculous leading edge erosion to have a load imbalance on the blade or the rotor Allen Hall: catastrophic. The things that will take down turbines today are light. It gotta be lightning. It’s gotta be number one. It’s not even a close second to that, I don’t think. Some sort of serial defect in blades. De bonding. Yeah, de bonding, right. Something that’s just. Almost immediate, but uh, but, but a structural problem, right? A structural problem that’s probably a factory issue, a quality issue. After that, it gets pretty consistent, right? You’re talking about gearbox failures, which are really. Time driven, some sort of bearing failure Rosemary Barnes: loose bolts in the tower. Right? Haven’t we seen a few of, a few of those Allen Hall: root blade root cracks, which are a manufacturing issue and yeah. The tightening of bolts. Rosemary Barnes: Yeah. Root inserts, Allen Hall: right Root inserts, Rosemary Barnes: detaching. Also foundation problems can cause it. Um, and, uh, could I just, uh, go off on a, a tiny tangent that you said, you know, lightning obviously I was talking to somebody recently, um, ’cause there was a, a tower collapse in Australia and they’re saying it was probably lightning. And anecdotally in the Australian wind industry, people are rolling their eyes going, oh, come on. As if that’s the case. So I don’t think it’s necessarily obvious. Um, I mean, I, I know that we all, we all know. That anything that can damage a blade so much that it, you know, falls in half or folds in half, or, um, you know, gets a big crack so it hits a tower, then you’ve got a big enough imbalance that your tower’s gonna start wobbling around like a noodle and then it’s gonna, you know, it’s gonna fall over. Right. Um, so it doesn’t, it’s not that the lightning. Struck the tower down, you know, even though, I mean, lightning can do that, we’ve all seen trees fall down right. From being struck by, struck by lightning. So I guess it, it, it could happen, but that’s not what the failure modes we’re talking about, right? It’s, it’s any, anything that can make the blades, um, damage, get damaged so much that they have strike the tower or a big chunk falls off and sets the, sets the tower wobbling. Allen Hall: I, I totally agree. And if those are the big money losers. The why are they’re not CMS systems installed to protect against the million two, four, $5 million loss. We’re focused on, weirdly enough gearbox monitoring, which is great, you know, but it, it is a time, long time derivative problem. It’s gonna degrade slowly. And we know what those curves are like, is just like leading edge erosion, right? So why wouldn’t you do the simplest. One first lightning transportation lifts. Then you’re looking at sort of serial defects. I think if, you know you got a, a root cracking issue in a particular kind of blade, then we put a CMS on it. But the, the gearbox monitoring and the oil monitoring all great, but are they, they’re not, wouldn’t be top priority in terms of money. Saved. Right. Rosemary Barnes: But I think it’s in terms of how easy it is to monitor these things, because I mean, maybe there are blade monitoring solutions today, I, I, maybe I’m not a hundred percent up to date, but at least until recently, there were ways to monitor it, but not cheap and not. Easy to actually monitor. You know, like it’s really hard to say, like, you know, um, wind turbines are, are, are cracking and stuff all the time. It’s like impossible to say, when is a crack gonna turn into something that I need to worry about? And unless you’ve got strain sensors like covering a blade like a net, you’re not actually gonna be sure that you’re gonna catch every single big crack that might happen. So I think that that one. Hard. Lightning I know is easy, but I don’t think it’s well understood how easy it is to monitor for lightning. Allen Hall: It’s a couple hundred dollars per turbine, right? Today. It’s cheap compared to a drone inspection, but I don’t think that’s Rosemary Barnes: well Allen Hall: known. Rosie would, would you say that the, all the cracks and the leading edge erosion and even some of those serial defects, because we’ve have drone inspections happening in some cases mandatory quarterly, quarterly. Yeah, quarterly. Would you, would you put a CMS system in, or we just rely on the internal external drone inspections as your quote unquote CMS? Rosemary Barnes: Well, I, I mean, I don’t think, I think you might end up with a false of a sense of false security by putting CMS to monitor cracks that were identified in drone inspections. I mean, if it’s a big enough crack to be worried about, it needs to be getting repaired right away. Um, it, and then there’s the next category down where. You wanna monitor it and see how it grows, then? Yeah. I mean. I dunno, it’s hard to say. I can see CMSI, I don’t know if even know if it counts in CMS ’cause CMS to me sounds like a, you know, like a monitoring while normal operation is happening. But when you know you’ve got a bad crack or maybe you’ve got like a serial defect issue and you know you’ve got 10 affected turbines in your site and it’s, you know, taking your long time to get, maybe you need even replacement blades or you know, you need to take them down and do a month long repair on each one. Um, sometimes you would really like to keep badly damaged blades operating. If possible, and then I can definitely see a case for you, you know, you’ve got an, a specific area that you’re monitoring, put some, there are systems that you can put in place to monitor a known one location of a, a crack. And then yes, definitely then you can, you know, run, you don’t have to be as cautious about shutting down your whole potentially affected, um, you know, uh, uh, population of, of turbines and, and blades. But beyond that, I actually, I don’t think that. Drone inspections are good enough and definitely not on their own. I mean, they don’t capture all of the inside stuff. Even the internal inspections don’t capture all of the inside stuff. I just think that you’re not actually like, you’ll get a little bit closer. Um, to knowing what’s going on with your blades, but not close enough to not have to worry about it. Joel Saxum: Yeah. I think that there’s a, there’s a couple of new advancements in, in CMS for blade cracks as well, so of course there’s, there’s multiple of these solutions actually out there, right? Uh, we have, we have a good friend of the show that’s installing cameras inside of. Blades to monitor cracks right now too. Uh, but also Aeros was doing that. They talked about it at Blades USA this week, uh, putting cracks in or cameras into monitor specific cracks. But there’s also been advances in CMS at that really minute level of ac accelerometers and vibration where, so a blade is inherently stiff, you know, the frequency of vibrates that if you start to get a crack in it. It reduces the stiffness, so the frequency changes in the whole blade. So it’s one of those things where like, if that happens, then it’s a flag come and look at me, I think. But, but I think where we’re at here now is this, Alan, you raised a great point with this conversation because if you were to ask Phil, Phil, what are the numbers for failures in the most expensive ones? 10 years ago, it would’ve been gear boxes. So in, in response to that, the industry was like, we need to monitor gear boxes. We need to monitor oil, we need to monitor all this stuff. And we have solved that. Not solved, but we have greatly reduced the cost of that problem as an industry. I. Right. So now we’re at the next stage. It’s like the industry has forgot that that’s how we solve that problem. And now we have the next iteration of problem, which is blades, and we have solutions for it, but nobody’s implementing them. Phil Totaro: Well, and the other, the other real issue for blades was about 15 years ago when a lot of companies were developing very sophisticated. You know, blade monitoring systems. They had, you know, fiber Bragg sensors that they wanted to put into everything. And I mean, but these, these systems were all so fantastically expensive and unfortunately unreliable, particularly as it, as these systems and the sensors on the blades interacted with lightning. Um, you know, you, you end up with. Uh, you know, a boondoggle that doesn’t really pay for itself. Uh, and so a lot of companies were just like, you know what, we’ll rely on drones. Which, you know, even again, going back 10 years, were cheap and still relatively are, um, to, to do that kind of an inspection as opposed to having a full fledged CMS system integrated into the blade as CMS technology gets cheaper. That increases the rate of adoption. Um, the reality is that the industry still needs solutions, but it needs more cost effective and targeted solutions. It sounds like Allen Hall: That’s what I’m saying is that I can go back to Phil’s point. You gotta have RROI, high, ROI on any kind of CMS. You put on your most expensive. Losses are catastrophic. Go cover those at a minimum. And the cost of those sensors to catch the catastrophic before they turn catastrophic are incredibly low. They’re in the hundreds of dollars well below a thousand dollars. Lightning ones are about $250 at the minute. They’re crazy low, they’re way less expensive than pretty much any other CMS on, on the turbine right now. Put them on, at least you’re gonna. Protect your Joel Saxum: huge downside loss. Yeah. Think about the simple math on that one. Alan. 250 bucks a turbine for lightning sensors so you know exactly when a tower got struck. And if you use them properly in operations, you can, you can instrument a thousand turbines. For the cost of one insurance deductible. Allen Hall: As Wind energy professionals staying informed is crucial, and let’s face it difficult. That’s why the Uptime podcast recommends PES Wind Magazine. PES Wind offers a diverse range of in-depth articles and expert insights that dive into the most pressing issues facing our energy future. Whether you’re an industry veteran or new to. Wind, PES Wind has the high quality content you need. Don’t miss out. Visit PES wind.com today. CPI composites, A major supplier in the wind energy industry has celebrated the production of its 100,000. Uh, the milestone highlights the company’s longstanding role in supporting the growth of wind energy through, uh, blade manufacturing across multiple global facilities. So, you know, obviously you do the math. 100,000 divided by three is like 33. Thousand turbines plus. That’s a lot of wind turbines. I was trying to do the math on where most of those blades were built. That, my guess is that a significant portion were built or, or are built right Joel Saxum: now down in Mexico. Right? Yeah. Everybody you talked to is like that. Yeah. That factory. That factory in Mexico. I think there’s three factories in Mexico. Two. I know there’s two. I think there’s three, but to me that seems, doesn’t that I, I honestly con congrats to TPI for the a hundred thousand to play, but. 30. Then when you do the math, Alan, you said 33,000 turbines. There’s almost 500,000 turbines in the world right now. That seems low. I would think that TPI would have a larger share. Allen Hall: Yeah, it does seem low. I, I would say they would have a lot more, so the a hundred thousand doesn’t make sense except that they were kind of, Johnny come lately in a sense that, that they were doing small production runs for a while. Mostly in the States when they started, they were making blades, I think in Rhode Island for a while. And then once it got to scale mostly in Mexico and Turkey and some other places, then it really picked up, right? Phil Totaro: Yeah. And then, but then they mothballed the, the Newton, Iowa factory in 2021 to shift production down to Mexico and India, where it was cheaper cost of labor and, um, you still had access to, to raw materials. Um, but. They’re now talking about, in part because of the, the threat of tariffs that are to be imposed on, on Mexico, potentially. They’re talking about restarting the, or accelerating the restarting of the Newton, Iowa factory, um, specifically to meet the demand for GE Joel Saxum: Renova. Oh, that’s cool. I mean, ge like the, the article you said today, Alan Scott Straza said a softening of the market there, but they still have order book. They still gotta create a lot of blades. I mean. They’re we’re, we’re, we’re built. Just think about the Sun Zia project. They’ve got hundreds of turbines just for that one project that they’ve gotta build. So, uh, yeah, I think maybe the TPI thing in my mind about why I thought it would be a bigger market share is just because a lot of the projects that, uh, that Alan, you and I, or our compadres in the industry work on. I have TPI blades in ’em. So maybe that’s just why my mind was going that way. Allen Hall: Well, and our friends at Vestas have opened up another presence in the United States. They opened some offices in Houston, Texas to much a great fanfare. Uh, they used to have an office in Houston years ago, as Phil has pointed out before we started recording today. Uh, but they’re back at it and it looks like they’re trying to get more of a foothold into the United States. They have about. 500 employees in Texas at the minute, but it does seem a lot of the manufacturing and production is coming out of Colorado. And obviously as Joel pointed out, you know, sun Z is a big project that Vestas is also involved with. Uh, so what does the growth outlook look like for Vestas and why the move right Joel Saxum: now? I, I don’t know what the growth outlook looks like, but I do know that being a person who lived in Houston and works and plays there still. There’s so many good engineers in Houston, and it’s not just mechanical electrical engineers. It’s every sort of engineer you can imagine, and a lot of it from that oil and gas world, right? So Houston as the. Energy capital of the world for oil and gas. Now that city is starting to rebrand itself as the energy transition capital of the world. They’re all the trade organizations are trying to do this. They’re grabbing people at oil and gas to be engineers. So there’s a lot of really good, smart people that understand the energy industry in Houston. If you’re gonna put an office in the United States and as a wind company, it’s a good place to be or or to do an event. Uh, this week’s wind farm of the week is the Jericho Rise Wind Farm. It’s an EDPR wind farm and it’s really close to the Canadian border, so it’s up in the northern part of New York state. And we’ll do a little bit of a wind farm, uh, by the numbers this week for the wind farm of the week. So, uh, this wind farm 37 S-G-R-E-G 1 14 2 0.1 megawatt machines, uh, that creates a total of 77. Point seven megawatts, uh, coming outta this wind farm. But the scope of work for some of the build out was, is kind of interesting. 55, 50 5,000 linear feet of access. Roads, 175,000 tons of sub based placed for roads and pads, 3.6 million pounds of rebar. Procured and installed for foundations. 23,300 cubic yards of concrete. Procured and installed 60,000 cubic yards of backfill, a hundred acres of trees. Uh, $132 million. Went into this wind farm with, uh, 76 construction jobs and six jobs created locally. So it gives you a little bit of the scale of what it takes to. Build one of these wind farms, uh, and this is 37 turbines, right? We’re seeing wind farms a hundred, a hundred fifty, two hundred, three hundred, even more than that for wind turbine numbers. So the, the size and scale of these things is, is growing and growing. So Jericho Rise Wind Farm, up at upstate New York by the Canadian border from EDPR, you are the Wind Farm of the week. And that’s gonna Allen Hall: do it for this week’s Uptime with Energy podcast. Thanks for listening. Give us a five star rating on your podcast platform and subscribe it in the show notes below to Uptime, tech News or Substack Newsletter. And if you haven’t joined us on YouTube yet, we’re getting close to a million subscribers. So you. Better click in there before we cross that magic number. We have to have some sort of giveaway at a million if we can figure out who that person is. That would be kind of cool. So we’ll see you here next week on the Uptime Wind Energy Podcast.…
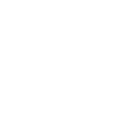
1 Nordex Optimistic in US, National Grid Sells US Renewable Portfolio 3:11
3:11
التشغيل لاحقا
التشغيل لاحقا
قوائم
إعجاب
احب3:11
This week on News Flash, Nordex’s determined stance on US growth, the Cenos Floating Wind Farm project, National Grid’s sale of its US renewable assets, and Europe’s wind energy production expansion to meet 2030 climate targets. Fill out our Uptime listener survey and enter to win an Uptime mug! Sign up now for Uptime Tech News , our weekly email update on all things wind technology. This episode is sponsored by Weather Guard Lightning Tech . Learn more about Weather Guard’s StrikeTape Wind Turbine LPS retrofit. Follow the show on Facebook , YouTube , Twitter , Linkedin and visit Weather Guard on the web . And subscribe to Rosemary Barnes’ YouTube channel here . Have a question we can answer on the show? Email us! Welcome to Uptime Newsflash, industry News Lightning fast. Newsflash is brought to you by IntelStor. For market intelligence that generates revenue, visit www.intelstor.com. Allen Hall: Starting off the week, German wind leader Nordex remains bullish on US growth despite President’s Trump Day one, suspension of offshore wind leasing. CEO, Jose Hlu Blanco confidently told Reuters they’ll hit targets, quote, even in worse case scenarios. North American business surged 3% to 10% of orders in 2024 while Nordex exceeded profit forecast with 296 million euros. The company now aims to recapture its former 15 to 18% of the US market position and projects five to 7% profit margins for 2025. Energy developers, flotation Energy and Vagrønn have filed for approval of their groundbreaking Cenos floating Wind Farm with Scottish authorities. The 95 turbine project will tower 320 meters above the North Sea, 190 kilometers from Scotland’s coast. The innovative offshore wind development secured through Crown Estate Scotland’s in into program will power both UK homes and North Sea oil platforms. Public consultation remains open until April 4th, building on momentum from their successful Green Volt project. In a major market move, national Grid is offloading its entire US renewable portfolio to Canadian giant Brookfield for $1.74 billion. The strategic divestment includes 1.8 gigawatts of operational assets and 1.3 gigawatts under development across solar, wind, and battery technologies. This sale follows similar renewable pullbacks by energy majors Shell, BP and Equinor Amid Profitability Challenges. National Grid will now concentrate investment on its core energy network infrastructure with the transaction expected to complete by early 2026. And finally, European wind energy suppliers are rapidly expanding production capacity with over 30 factories across the continent being expanded or newly built to meet ambitious EU 2030 climate targets. SEF is investing 300 million euros in Rotterdam to produce 200 triple XL offshore wind foundations. Annually by mid 2025 while Siemens Gamesa announced a 200 million Euro investment to upgrade its facility in France to produce next generation 14 megawatt turbine blades, creating 200 new jobs. The manufacturing expansion spans cable production in nine European countries and turbine component factories in Denmark, France, Poland, Italy, and the uk. These investments totaling 11 billion euros over two years, strengthens Europe’s energy security and creates thousands of jobs.…
Allen and Joel speak with Birgit Junker, co-founder of the Global Blade Group, a forum created to share knowledge and innovation around wind turbine blades. For over ten years, the group has been making blade information more accessible and approachable. For more information on joining the Global Blade Group, email tgbg@statkraft.com . Link to Blade Handbook – https://www.bladena.com/uploads/8/7/3/7/87379536/cortir_handbook_2019.pdf Fill out our Uptime listener survey and enter to win an Uptime mug! Sign up now for Uptime Tech News , our weekly email update on all things wind technology. This episode is sponsored by Weather Guard Lightning Tech . Learn more about Weather Guard’s StrikeTape Wind Turbine LPS retrofit. Follow the show on Facebook , YouTube , Twitter , Linkedin and visit Weather Guard on the web . And subscribe to Rosemary Barnes’ YouTube channel here . Have a question we can answer on the show? Email us! Allen Hall: Welcome to the Uptime Wind Energy Podcast Spotlight. I’m your host, Allen Hall, along with my co host, Joel Saxum. Today, I’m delighted to welcome Birgit Junker, a true pioneer in wind energy blade technology and the co founder of the Global Blade Group. This organization has become the premier forum for the wind turbine blade experts to collaborate, share knowledge, and drive innovation in areas like structural design, Lightning protection and blade inspection technologies. Welcome to Uptime Spotlight. Shining light on wind energy’s brightest innovators. This is the progress powering tomorrow. Allen Hall: Birgit, welcome to the Uptime Wind Energy Podcast Spotlight. Birgit Junker: Thank you very much and thanks for having me. Allen Hall: I want to start off by looking back a little bit into 2013. What were some of the challenges that when farm owners were facing with Blade technology and maintenance that led you to create the global Blade group? Birgit Junker: To start with Rege from Vattenfall and I, we were relatively new on the owner operator side. And we both found that when we were speaking to our colleagues, they, their eyes just glazed over every single time we said Blade. Cause nobody knew anything about blade. When I was hired at Eon I came from from Siemens. I was hired at Eon. I was told that they didn’t have blade issues. So I should expect to work about 80%, 75 percent on blades. And the rest of the time I should be spending on a drivetrain. 10 years later, when I left, there were 10 blade people. And I never ever had to look at a drivetrain. That was the attitude then. Blades were not a problem. We didn’t have blade problems. Blades were like that black box that you had. You just went out there and counted that they were all there. And you listened just to make sure that there wasn’t anything strange going on. And about, you 99. 9 percent of the time, nothing happened. There was nothing wrong. We even had contracts that said that blades were maintenance free. But then Reg and I started on the owner operator side. We came, we both came from OEMs. I’ve done catastrophic failure investigation. I’ve done field failures. I’ve done all sorts of things for what, 10 years before that. And knew that we did have blade problems. Ian just hadn’t found out yet. So when I started, Reg and I, we decided that we needed to talk to one another because we couldn’t talk to colleagues. Joel Saxum: Birgit, from experiences in the field I would, I want to follow up with that as a hard second. Because so many people Don’t understand even today what’s going on in the with blades. Like I’ll give you an anecdotal problem. I was in a field doing an RCA and out there with a site supervisor who was in charge of 120 odd turbines, big wind farms in the States, right? And he was looking up. He said, yeah, those blades, he’s they’re just, big plastic wings in the skies. And I was like, they’re not actually plastic. And he goes what do you mean? I said it’s it’s like fiberglass and this and that. He’s wait a second. So you mean to tell me that thing’s like a, it’s built like a boat. Like it’s like a fiberglass boat up in the sky. And I said, yeah. And I was like, I was like, that’s more in line of Ben, a plastic wing. And he goes, Oh, he’s I never really knew that. And I said, Oh, further conversations with this this gentleman, he’d been in wind for 15 years and it was running wind farms and didn’t know that the blades were made out of fiberglass. So I think that when you came in, what you’re talking about, it’s the origination story of Global Blade Group here. That could be echoed all over the world. There’s so many people that don’t know. What it really is. You and Reketpale from Vattenfall, so you guys got together, you understood that, Hey, we could talk to each other about these things and try to fix these problems. Did the next conversation go, let’s bring more along? Let’s bring some others along? Birgit Junker: Our initial goal was to increase the knowledge about blades in the industry. And I am still now after 22 years in the industry, I’m still asked, are blades hollow? So that goes along with your your guy in the U S asking if, glass fiber, really? But but yeah, the initial goal was to increase the knowledge, but also. And to have a common front towards OEMs and other interesting parties, the first meeting we had was actually with DNV and GL about the the guideline for blade design. And while we were sitting at the table, one of the managers looked at us and said, very discreetly, I’ve actually never spoken to an end user before. And these are the people doing the guideline for blade design that all blades are type approved type approved from. And with my normal way of speaking, sometimes I speak without thinking. I just looked at him and said, I guess that was about bloody time. Allen Hall: It leads to a good point, Birgit. So what is all this, when you have all this fragmenting knowledge running around from different organizations, how does that affect the performance and maintenance of blades out in the field? If you don’t understand some of the fundamentals, what are the consequences of that? Birgit Junker: You got two two very extreme consequences and then something in the middle. The. The worst consequence is that people look at them like a black box. Like Joel’s American site manager and don’t do anything. Especially if they have one of the really old contracts where it says that blades are maintenance free. And then you have the they don’t do anything. They run them and suddenly they fail and they get shocked and they’re like, Oh my God, something happened. I don’t know what to do. And then you have the other extreme. Where a company will have an independent service provider on blade repairs servicing their blades or the OEM servicing the blade, and they will do repairs that aren’t necessary because they are being over eager. They want to make sure that the blades are perfect all the time. And you don’t need that. You need something in the middle. You need to maintain your blades in such a way that they don’t fail and you get the expected AEP. But that doesn’t mean that you have to repair them every single year. It just means that you need to keep an eye on them, make sure that they don’t crack that they don’t have cracks in structural areas, that they don’t have open leading edges or open tips, that they don’t have lightning damages that are severe. And if you do that, you can cut down on your maintenance. And have a turbine that operates really well. Joel Saxum: I liken some of this, and this is not just this comet is not just blades, it’s drive, train, gearbox, bearings, all these things and wind. So if you have say, we talk about a fleet wide problem. You have a, we’re in the States, a Ford truck. Okay? A Ford truck. There’s millions and millions of these things out there. In the hands of all kinds of people. And so when there’s an issue with something, there is a tribal knowledge that’s so deep that you can reach out in every direction and find an answer. Everybody has an answer to how to fix this carburetor or whatever it may be on this vehicle. In wind, we have such a small size of a fleet, right? So if you’re, say you’re a XYZ wind operator and you’re a decent size, you have a thousand megawatts of wind production. You may only have 50 of one kind of turbine and 60 of one kind of turbine 80 of one kind of turbine So that’s not a very big like statistical fleet to pull information from because failures happen at different rates and different things and different blade Manufacturers then we get deeper and we get into this one was manufactured at this plant versus that and we have this model But they have those blades and so it creates an inherently tough problem for the industry And the answer to it is the same answer that we, or in my opinion, the answer to it is the same answer that we hear at almost every conference, trade show, industry get together. We hear collaboration and transparency. However, it’s hard to make that happen, but that’s what you guys have done here. That’s what the global blade group is based on is collaboration and transparency, because if you’re one operator and now all of a sudden you have, Eight friends that are operators and they can share information from their fleets with you. Now you have this collective piece of info or collective batch of information that can give you so much more insight into what may be happening on your own fleet. You guys have taken on a lot of projects in this manner. What, what does that look like for collaboration? Birgit Junker: To start with, we we were on a much lower level. We were just like, we want to function as small own operators, a back office support. We had companies that were part of the initial, we started being the blade group and then there was the. Scandinavian Blake group or Nordic Blake group. And then it became the European Blake group. And now it’s the global Blake group. But to start with, we had small owned operators that were part of it. And they would call us, some of us, one of us and say, my OEM says this. What is he actually saying? Or in one case, it was like, can I actually believe this? And we could then go in and translate what was being said to make them understand it a bit better. And that’s what I mean by we wanted to raise the awareness and the knowledge with, within the industry, especially the small owned operators, because a lot of those people, they were appointed blade specialists with actually never really seeing a blade. But that was just their area of responsibility in in the company. And they were just trying their best and and that’s fine too, but we wanted them to have a bit more knowledge when they said yes or no to to an OEM. Primary goal was to increase the knowledge. Secondary goal increase the matureness of the industry and increase the Communication between OEMs, ISPs, and OWN operators. Allen Hall: And that’s a different approach than other organizations take on BLADEs in particular. I’m not going to name them, but there are several organizations that are trying to do something similar. But I always feel like they’re very rigorous in the documentation phase, creating of standards, whatever that is. But they don’t have the requisite engineering at the table to help explain these things. Is that what the global Blake group really brings to the offering? Birgit Junker: We we’ve actually requested not to have any kind of commercial people present. We want it to be an open technical discussion. Of course we honor everything, which is, NDAs and all that sort of stuff is on it, but it’s critical. Communication of a technical nature between owner operators and and sometimes it’s also helping somebody to decipher what they’ve been told in connection with a failure or a new kind of blade, all that sort of stuff. And it’s just, um, because it’s free and because we only have own operators because of GDPR, which is the European rule set for communication and and data. We are able to speak relatively free, relatively freely without having to have lawyers present. And because we don’t have commercial people, and we don’t talk about projects if they haven’t been signed yet. We don’t talk about a lot of things where we would, you know, Require lawyers or commercial people. It’s technical stuff. And very often we don’t know what site people are asking us questions about. We don’t know. We know what turbine type because we don’t need to know what blade type, but we very often don’t know what country it’s in what area it’s in. We know if it’s onshore or offshore and whether it’s in a lightning area or not. If we’re talking about lightning, that kind of stuff. Allen Hall: Let’s focus on one particular problem, which I think is universal, which is lead, leading edge protection, leading edge damage. And I know you’ve been vocal in that area and I talked to you at Sandia a couple of months ago about this and I got an earful, which is fantastic by the way, because I like hearing your opinion about this, but how does that work in terms of the global Blake group? If you’re looking at a particular problem, how’s it sussed out among the members? Birgit Junker: We create what is called a JIP, which stands for joint industry project. Right now we actually have a JIP on leading edge erosion where seven own operators in Europe and the U S have decided to put some LEPs on turbines. And for most of them, I think it’s seven the seven own operators that are part of it. Six of them have put the same material on at least one turbine in the test. And then they have put two or three different LEPs on different turbines so that we all have the same one. So we have some, a reference point and then we have all the other ones and we we got some assistance from a third party in the UK, they get access to all the data from our inspections. They put everything together and we can now see five years down the line, which LEPs are better than others. Which ones fail first, which ones fail last. And because we all put the same LEP on as a reference point, that is the one that everything is compared to. And we can see that some of the LEPs fare really well, some of them not so much. And we can also see that some of them should have been put on from platform but weren’t and some have have been really easy to put on. And we’ve also seen a difference between the different LEPs in the sense that some tapes work better than other tapes. Some precasts are better than other precasts and within paints there are differences as well. And we got everything from a three layers LEP to a single layer paint LEP. Yeah, we do joint industry projects and it’s voluntary for the ones that want to be part of it. They pay what they do. And each company, each individual company pays for their part. So there’s nothing between us financially. Allen Hall: Yeah. So there’s no money coming to the table just to belong to the group. But if you want to participate in the testing program, like on this leading edge protection effort, you’re going to put some coatings on your blades. You’re going to donate that time and effort to go do that. But the return on that investment is a hundred X because you can’t find good information on leading edge protection from real world turbines. That is the hardest part. And then to tie it together with the engineering knowledge, And history of blades that the global blade group brings to the table. That’s not anywhere else on the planet right now. Is this just one of several projects that you’re working on at the minute? What are the other projects that you’re working on? Birgit Junker: We focused very much on the LEP because when we started this project we were three companies to start with Stattgart, Vattenfall and and Eon. And we tested 20 LEP projects. On a rain erosion test and chose the ones that behave the best. And then we made this JIP where we invited the rest of the Blake group to participate. And we ended up being seven own operators. And we’ve been, that has been running now for five years. We’re actually at the moment talking about starting two new JIPs, one on on databases and inspections and how we can deal with those because we we get information and very many different kinds of data. Formats and quality and stuff like that. Try and make something where we can do added benefit from the data that we get, and we’re also looking into the last one is that beginning, beginner stage. We want to test some some CMS data or CMS systems. But it’s like having a project that’s seven times as large as the one that you can do yourself individually in your company, And and you’re only paying for your own part. So it’s, you get a lot for nothing or a lot for a little. Joel Saxum: How do we add a fourth one for lightning protection upgrades? How can we do that? Birgit Junker: You ask kindly. Joel Saxum: I can get down on, I can get down on a knee. I think it’s a fantastic idea, right? Because you’re not only are you getting different I think the installation part is a big one. You’re testing the LAPs. Yes. But you’re testing how they were put on the ambient conditions. They were put on all that stuff is great. But the big part here for me is It’s being tested in varied geographies, right? Because you can put LEP on one wind farm in one spot and you’ll get a certain amount of tests. But if you spread that test from different corners of the world, different corners, closer to the ocean, maybe offshore, maybe onshore, maybe up in a mountainous range, maybe in Spain, maybe in Canada, wherever. And you add all of those together, you start to get a much better picture of the overall qualities of whatever this product is. So in that project, you had seven owners involved. What does a normal meeting look like? How many people, how many different operators are involved in a normal meeting? Birgit Junker: We don’t have a lot of meetings because we have a third party that does all the the analysis. The JIP was actually started by EDF. And they sent a project proposal to all the own operators and said anybody want to be part of this, you want increased knowledge. And the only way we can get it is by going out and doing it. And if we should do it ourselves, it’s going to be humongous. But if we do it together with the rest of you we can get more for less. And so EDF is running it. But we have a third party doing all the analysis and the reports. And if you come to the DTU event on leading edges in February, I think it is you will actually hear about the five year report. And we are also looking into extending it because there are at least three new LEPs that we haven’t trialed. And so we are right now discussing whether we can extend it or whether we should start a new one and and how we can do that. Joel Saxum: Bjerken, let me ask you a question, cause this is one that I have quite often and Alan, earlier in the show or in this little recording, you had mentioned different groups. In those different groups, and so this is, this may be a point of contention here, in those different groups, they want operators, and that’s great because they don’t want outside influence changing how they are. However, in my opinion, I think that at some of those meetings, they should have, or some of those conferences, some of those meetings, some of those get togethers, some of those white papers that are written, I believe that they should bring in subject matter experts in individual subjects. Like I’m talking, if you’re talking aerodynamics and you have a bunch of blatant people, that’s fantastic. But, in my mind, I would bring in Nicholas Goddard as an aerodynamic subject matter expert to supplement that conversation. It’s the same thing I talk, like, when we see people talking operators talking lightning. Alan and I live lightning all day, every day. That’s all we do for our day job, is we have to eat. When I believe that, in some of those conversations, that, that bit of knowledge could be very beneficial to that group. Do you guys bring that in, or is it all just operators and nobody else is allowed? Birgit Junker: Because of the confidentiality and GDPR and all that, we can’t bring in ISPs or subcontractors on specific areas, especially not if they’re suppliers. One of the main parts is that we’re not allowed to talk about the cost of using these subcontractors or suppliers. Because that would be a competition issue. But what we’ve done is that we’ve made working groups right now Bladina has a working group on stock on structural damages. So on the team site, which is the new place where we’re going to store all the data Bladina has access to the group the working group called structural damages and talking about Nick from PowerCurve After New Year he will actually be heading up a new group called Aerodynamics. And and Politech has yet said yes to head up a working group called Lightning. There will be webinars. There will be sharing of information. We will perhaps be making some kind of inspection reports together so that we are talking the same language. That’s one of the things that started the whole I think it was you, Alan, that mentioned it earlier. The Blade Handbook. The Blade Handbook was actually written by one of the owners. And it was like four pages. It was an information for employees. And then Vladina helped them make it. And and after agreement with this owner Vladina said, when we do these projects because they do a project very, very often they do projects for us we could add more data. We could add more knowledge, we could add words, we should have a common language. So that’s actually how the Blade Handbook started. It was it was an attempt for us to speak the same language, use the same words, understand what everybody was going on about. And it’s it’s now a very comprehensive book with lots of terminology. And that was the common goal was a terminology. So everybody understood what we were talking about. Whether it was, leading edge or trailing edge, the abbreviation for it, whether it was pressure side or suction side the abbreviation of it, but also the different ways that blades are built up. You’ve got the box bar, you’ve got the integral blades, you’ve got the web blades, you’ve got carbon, you’ve got a glass fiber, you’ve got balsa, you’ve got pine, you’ve got PVC, you’ve got PET, you’ve got all of that is in that blade handbook. to make sure that we speak the same language. Allen Hall: We’re going to put the link to the Winter and Blaze handbook in the show notes, because if you don’t have that as a reference on your laptop, your desktop, or printed out next to you on your desk, you need to do that because a lot of the knowledge that comes from the industry and all the experts that are from around the world when they put that into a condensed volume, that is explanatory. The average human can understand what’s happening. Those things are invaluable. And you need to go find that. We’ll include that in the show notes, Birgit, because it’s a really important document for the industry to continue to grow and understand what is happening. And I know we, Joel and I had talked to a number of operators and engineers that are interested in joining the Global Blade Group. How do they do that? What’s the process? Birgit Junker: They send an email. Allen Hall: It’s that easy? Birgit Junker: It’s that easy. If you’re an owner operator. And you send an email to the email that you will share on the screen at some point, Alan. I will be on the other end and I will send you an email specifying exactly what you have to do. And it’s all based on teams. So you have to join a team’s site and you’ll have to put your name in a membership list. That’s how easy it is. There are also bylaws because more and more owners didn’t want to join unless there were bylaws. Before COVID we were 52 owner operators. There are quite a few people that have left their jobs. So we need to reestablish the contact with some of these companies, but we’re we’re getting up there. And and the whole idea is to increase the knowledge. and have a common area where people can share information and ask questions and also ask the stupid questions. Personally, I don’t think there are stupid questions, just stupid answers, and they’re usually supplied by me. But if you don’t know what the leading edge of a blade is, you should have somewhere where you can ask that question. Because a lot of the people that actually work with blades. Don’t have the introduction to what a blade actually is. Allen Hall: Yes, that is so true. And if you want to join the global blade group and get connected with Burgett, the email address is tgbg@Statkraft.com. So tgbg@statkraft. com. Birgit, thank you so much for being on the podcast. We’ve wanted to have you on for a long time. We need to have you back more often because there’s so much information and you’re. Tremendous help to industry. So thank you for being on the Uptime Podcast. Birgit Junker: You are more than welcome.…
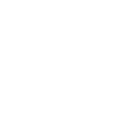
1 SkySpecs Predicts Component Remaining Useful Life 27:35
27:35
التشغيل لاحقا
التشغيل لاحقا
قوائم
إعجاب
احب27:35
Allen and Joel speak with Allan Larson, VP of CMS Products at SkySpecs , about their remaining useful life estimates for operators. By predicting component failures, operators can create better maintenance schedules, saving time and money. Fill out our Uptime listener survey and enter to win an Uptime mug! Sign up now for Uptime Tech News , our weekly email update on all things wind technology. This episode is sponsored by Weather Guard Lightning Tech . Learn more about Weather Guard’s StrikeTape Wind Turbine LPS retrofit. Follow the show on Facebook , YouTube , Twitter , Linkedin and visit Weather Guard on the web . And subscribe to Rosemary Barnes’ YouTube channel here . Have a question we can answer on the show? Email us! Welcome to Uptime Spotlight, shining light on wind energy’s brightest innovators. This is the progress powering tomorrow. Allen Hall: Welcome to the Uptime Wind Energy podcast. I’m your host, Allen Hall, along with my co host, Joel Saxum. And today we’re diving into a critical challenge facing wind farm operators, predicting component failures and optimizing maintenance schedules. Imagine if wind farm operators could instantly gauge the cost impact of their decisions And automatically assign a dollar value to the risk. It sounds like science fiction, but it’s actually becoming a reality through innovative approaches to remaining useful life assessments and automated risk detection. In today’s episode, we’ll explore how these technologies are revolutionizing wind turbine maintenance. Helping operators reduce downtime, cut costs, and extend the lifespan of their assets. We’ll learn how advanced analytics and artificial intelligence are enabling more precise predictions and smarter decision making in a WinFarm world. Our guest is Allan Larson, the VP of CMS products at SkySpecs. In his role, Allan leads all aspects of product development for the Horizon CMS platform, which is crucial for wind turbine drivetrain monitoring and diagnostics. As part of SkySpecs product team, Allan manages the product roadmap, conducts market research, and oversees the development and launch of new features. His expertise is key. In condition monitoring systems and AI based fault detection for wind turbines makes him a key player in shaping innovative solutions for the wind industry. Allan welcome to the show. Allan Larson: Thank you. Allen Hall: That was pretty good, wasn’t it? That was a pretty good intro. I feel pretty good about myself now. Play it when you go home from the show here, yeah. That’s the rap, people. Uh, so, you’re a drivetrain specialist. CMS drive space. Allan Larson: Yes. Specialist. These days, that’s what I’ve become. Yes. Allen Hall: Yeah. And that is, uh, obviously a really needed, uh, knowledge base, particularly as the number of wind turbines has grown dramatically and we’re rapidly producing turbines. We also rapidly produce drive train problems. And CMS is going to be the only way for us to dig ourselves out of a little bit of a hole on gearboxes and bearings and some of the drive train issues. Uh, what do you see as sort of the top level issues out in the field today and what are you, what are you hearing? Allan Larson: Well, I mean, I think about it not so much in terms of, uh, which, uh, which failure mode is occurring most today or whatever. It’s more, um, the failure modes that you have today is something that we need to detect early so we can act on it, right? And, uh, that’s what CMS is all about. It’s about this early and accurate detection of failure. of drive train failure modes so you can take appropriate action at the appropriate time. Allen Hall: Yeah, it’s been a very busy crane season in the middle of the United States. We’ve noticed a lot of gearboxes and main bearings being replaced. The CMS systems are going to play a bigger part in that. I think a lot of operators are becoming much more aware that CMS is needed on drive train. Allan Larson: Yes, um, actually when we, when we started, uh, the Company Vertical AI that SkySpecs acquired in 2021. When we started that, we thought, uh, our perception of the market was, say, uh, Europe is in front here, like they’re the most mature, most likely to adopt a new software solution. And then we thought US is a bit behind based on what we knew about the market. And we would say, well, I think the US is maybe a decade behind in CMS adoption. That’s it. Uh, and I think it’s almost the other way around now. And so the U. S. market has picked CMS up like crazy. Really? Yes. So, uh, this is more and more becoming the perception that you just need to have that. There’s no new turbines being produced in the market that doesn’t have a CMS system. Right. The manufacturer simply can’t offer a guarantee without it. Because they need to make the same maintenance decisions during warranty. And they need to know about it. Hey. Pending failures, uh, leading up to an, uh, end of warranty date. And if they want to offer long term guarantees like FSAs, uh, they need to know what the current, uh, failure status is in their fleet. And so you do that with drivetrain condition monitoring. There’s some damages you can detect up to a year, several years in advance. Right. And others that’s months, half a year away. Right. Like I said, we’ve, we’ve sort of. Uh, with our software focused in the beginning, of course, I’m solving the whole condition monitoring problem. But, uh, now we turn our attention a lot more towards how to drive action in the field more efficiently. That’s where the remaining useful life comes, comes into it. Um, How was Allen Hall: that, how was that implemented? I’m really curious how you think through that as a problem set and get to an output. What does that look like? Obviously you’re taking out all this data and we know more about turbines today than we knew 10 years ago. A lot more. There’s just so many more sensors on a turbine than there were, especially coming out of the factory. Even though I think a lot of operators do complain that the number of, uh, amount of sensors that are on there probably isn’t enough. However, uh, you got to give the OEMs credit. There is more data coming down and people are adding their CMOS systems on top of them. What do you do with that? How do you process that? What does that look like? How do you attack the problem of assessment? Allan Larson: As in on the actual condition monitoring Allen Hall: part? Yeah, how do you look at all that conditioning monitoring and then helping that site manager make a decision? Allan Larson: Um, I think the detection problem is too hard to explain on radio. Laughter Um, and uh, others have done it. I think I’d rather talk about the, the, um, Well, yeah, that’s what I’m trying to get at is it will kind of surprise you a little bit on how we approach it because, um, at the moment, it’s not so much about like, Oh, we’re going to combine all our data streams and then produce a magic output. It’s actually more of an understanding of the problem itself. So let’s say that you, um, detect something on a main bearing, detect damage on a main bearing, right? It’s, we’re not predicting that something might happen. We detect something that is happening right now. like a damage that’s ongoing and that will last a certain amount of time. But, uh, and so we, the diagnostic piece of that is saying, well, it’s an, it’s an inner ring fault or it’s an outer ring fault, or it’s a bearing, a spalling issue or something like that, right? You can diagnose it down to a really specific level. Um, but regardless of what it is, you’re going to have to exchange that main bearing at some point. You can’t avoid it. Maybe you can extend the life by greasing the bearings and purging the grease and re greasing it, so on. But the sort of prognostic of it, right, the prognosis, sorry, is clear, right? That main bearing is going to die, you’re going to have to exchange it. Allen Hall: So the remaining useful life is an interesting concept. Not a concept, I mean, it’s an action. But, obviously, when the designers of a component like a main bearing come to you and say, Well, The lifetime of this bearing is a thousand years. Allan Larson: Yes. Allen Hall: And then it’s five and it’s toast. Allan Larson: Yeah. Allen Hall: So something’s wrong there. Are you coming in for the remaining useful life and saying the lifetime of this bearing is actually a lot lower? Which then increases its cost? Is it based on history? Allan Larson: Yeah. No, so, um, Allen Hall: Because the predictive failure, right, the predictive failure rates are built into specs. So the OEMs are out going to the manufacturers saying, I need to have one of these out of a million fail. Yeah, well, so, Allan Larson: I mean, we’re talking about a domain where you detect something, right? You detect, let’s say that main variable, the probability of you having to exchange that main variable is 100%. Sure. It’s going to happen. Sure. It’s going to happen. Yeah. But there’s a, there’s a, there’s a time when there’s a step change in the cost and time on, and the time you have until then, that’s basically your remaining useful life, right? That’s what you, what’s for you, but you should be interested in the time until I think I incur a risk. So instead of saying that you have a probability for a risk, right? You’re talking more about using RUL as a proxy for risk probability. Okay. Okay, right. So you’re Allen Hall: saying there’s a time window where that risk is can occur in or maybe not. I’ll give you the US versus European example. 10 years, repower US. 30 years, Germany probably still running. Allan Larson: Yeah, but here you’re talking more about risk quantification on a fleet level. So like, should I buy this turbine or not? And like looking long term projections, but I’m talking about the detection of the individual failure mode. We have an ongoing case on a main bearing right now. How do I, how do I, uh, how do I make decisions on should I fix it? Yeah. When should I, when should I repair it? Is it when, or if Allen Hall: I want to get to that point, is it, is it a win or is it more like an if with a, with a 10 year lifespan and the economics, I think you raised a good, good question, Alan, which is Allan Larson: 10 years into the future. Like we just said earlier that the main bearing damage, like you, what will last you, maybe 12 months, right? Sure. You’re looking, you’re looking into either this or next financial year. Allen Hall: Sure. Allan Larson: Uh, and, and you’re not, you’re not doing, um, like, uh, you know, like your, your, your, your Weibull, uh, uh, Weibull based statistics to forecast failure rates in your fleet. You’re looking to make decisions on the, on the actual repair test. That’s in front of you. When should I do it? And how should I prioritize it up against the others? Okay. All right. Yeah. So it’s not that 10 years into the future or this and that fleet, you’re really looking at, um, um, I know what the, I know what the costs are sort of predetermined, right? I know what the liability is approximately, right? Sure. And I know what the risk is approximately. You can actually put that for all failure modes for the drive train. The individual customer will have an individual owner will have a cost assumptions they can put into something like that. Yeah. So the liability and risk, but you need something else just other than that to understand when I should and how I should prioritize. So. Okay. Okay. So. That’s a very interesting aspect. I’m realizing now this is also tough for radio to explain. No, no, no. Allen Hall: It’s good because I think this little walkthrough is indicative of the dilemma that a site supervisor would have and decisions they have to make. So, what you’re saying is, okay, inevitably we’re going to have to replace this part or a couple of parts probably were up there. When do we, when do we manage, how do we manage that? The outlay of funds. How do we best manage it so we’re, uh, best spending money? Allan Larson: Because that’s Allen Hall: ultimately what it comes down to. Allan Larson: You want to do two things. You want to, uh, you want to avoid risk, obviously. You want to avoid those costs. Sure. Oh, sure. Yeah, yeah. You want to avoid the risk. And on the liabilities you have, uh, or you can say all your, when I say liabilities, I mean all your, Repair tasks. Let’s say you have two gearbox repairs that are pending. You want to do it at the same time. So you only have to get the crane out to site one time, right? Right. That’s the, and you optimize on your liabilities in a way. So there’s optimize your liabilities and avoid your risks. RUL comes into place when you say like, well, look, uh, the ideal world would be, I have a countdown timer. I had it say, I have a 269 days until I have to exchange this main bearing or have to place the order because there’s an additional two months of lead time. Between my, my place in the order and it happening, right. And then I avoid unplanned downtime or you have, you have exactly 29 days until you lose that uptower repair opportunity. Right. But that’s, it doesn’t work like that. You don’t get that precise. RUL is really difficult. Allen Hall: Is it though? Allan Larson: It’s very difficult. Allen Hall: I’m asking, you’re the expert here. I’m the novice at this. For as many wind turbines, if we are built at particular models, I can think of, you know, Early Vestas turbines, GE 1. 5s, all those Siemens Gamesa turbines that are all the same. Do you not have some, at this point, predictive modeling of what that looks like? So that, if my CMS system is giving me this level of vibration noise, that, hey, that means you do have 300 days to make a decision. Allan Larson: Sure. Allen Hall: For Allan Larson: some, for some, uh, often occurring failure modes for certain populations of turbines. You’ll have a big enough data set to say something. That’s usually valuable. Yes, but it’s very rare that one actor has all of that data all at once, other than the OEM. And even when they have it, there’s huge mechanical variance. Even if you look at 2. 3s, Siemens 2. 3s, for example. Oh, sure. Joel Saxum: Different kinds of bearings in them. Even Allan Larson: those bearings, even if they have the same model, have used different batches of metal, right? Yeah. It’s often how you find like serial defects, right? Is that this or that batch of gearboxes was produced with a poor quality metal or something like that. Temper, right? So even within the same model, there are batches of, so the mechanical variance is huge. And then there are loads of factors that we don’t know what that, uh, that we can’t measure that drives a failure mode degradation. It’s really hard to measure loads. For example, on a live turbine, you can, you can approximate it with power curves, but you can’t really do it. Right. All right. And, uh, how is the individual turbine lubricated and, uh, cooling systems? How are they running? It’s a very, very complex problem to say, and they all affect the remaining useful life. I give you a counter example, right? Predict EV range, right? Let’s take Tesla cars, right? There’s probably how many millions of cars, millions of like, say, model threes out there, right? They’re, they’re very similar mechanically, like it’s not exactly the same, almost close, right? You have probably 500 million to a billion samples of battery drain from time to end. You have very few and measurable factors like acceleration, elevation, temperature, all that stuff to help you make predictions on battery life. But still, nobody drives their batteries to zero. Allen Hall: Right, because they know that’s a problem. It’s an estimation. Yes. Allan Larson: Right. Not only do you not really, um, trust that you would also constantly be looking at that countdown because it’s going to live update all the time, right? Right. It’s very hard to do with wind turbines. Is Allen Hall: it, is, let me, that’s a good analogy, right? So the electric vehicle is a good analogy in the sense that Tesla has Millions of vehicles on the road. I own two Teslas. Allan Larson: Oh, well you’re Allen Hall: contributing to the data set. Yeah, but, yeah, I know. You see what I’m saying? I just Allan Larson: want to say, just for good measure, I bought them before I knew Elon was crazy. Okay? Allen Hall: He’s going to put a man on Mars pretty soon, so. We’re a woman on Mars, we’re not the other. So you can’t be that crazy, but you know what they’re on the on that side on the on the Tesla side that they’re Analyzing all that data to do predictive analysis on lifetime and it then turns it to value it turns it to value for them turns It to valuation of the vehicle. I Want to return my vehicle and buy a new model 3. What is this model old model 3 worth? Well, only Tesla really knows. Yes, they can Use predictive analysis and remaining useful life on Allan Larson: it. And stuff like knowing what batch of metals goes into that. Only the OEM knows. And maybe, and maybe only really that the gearbox OEM, right? Yeah, true. But really no, really no, right? Like that visibility throughout the supply chain. It’s not, that’s not our transparency. It’s just not there. And I think it would be too complex a problem to solve to get it. So you need a, you need a different approach. So it’s, it’s, so actually that’s the best way to say like, so One of the things I’ve learned with working with our CMS engineers is that they’re not, um, they’re not afraid of saying, we think this failure mode will last this and that many months. So the true reality of RUL is that today you’ll say, Hey, this, this failure mode will probably last another two months, but, but I’ll check it again tomorrow. Allen Hall: Yeah, yeah, yeah. That’s the smart move. Joel Saxum: Yeah, I think the smart move is to take the worst case scenario. Like if you had, uh, 40 different types of bearings and different ones, the one that’s going to be the worst, that’s the one you model it off of. So you don’t run into the Allan Larson: Yeah. But you still need some sort of framework to communicate to site that they can use to communicate to their investors or management or whatever to tell them something about, you know, What’s the cost impact of this and that damage? What risk am I avoiding? And essentially, what value am I getting out of my CMS system? And that’s been sort of, that’s been what I’ve been really trying to do something about over the last year. Just come up with a model that kind of works. And I think one of the things we shouldn’t be afraid to do is just Rely on some of that experience from CMS engineers and put it in a framework. That’s big uncertainty. So you can say, Hey, I think this, you know, this main bearing typically lasts 12 months plus minus three months, but then you can use that uncertainty as a, as a, as a, as a risk gradient. So you will say until it gets to the lower bounds of this uncertainty, it’s low risk when it gets to the right, when it gets to the lower bounds, it’s medium. Upper bounds of uncertainty high and beyond that it’s critical, right? Cause then you have a decision framework. You can sort of look at your fleet and ongoing things to make priorities with. Suddenly you can make a trade off. Let’s say you have two gearbox damages. One is in very early stages and one is in the late stages, but I can get a 25 percent discount if I replace them both now, but what I’m sacrificing, so I’m winning and avoided risk, but I’m also. I’m, I’m, I’m exchanging another gearbox too early. What am I sacrificing? What am I sacrificing? Well, you’re pushing, you’re pushing, there’s two things, right? You’re pushing, uh, uh, uh, uh, a liability forward. So then you’re looking at it from a financial perspective. You’re saying, well, what’s the future value of cash, right? Yes. Right. That’s all about. Right. And so I’m willingly, I can, I can make that calculation because I’d have an internal discount rate of maybe 10 percent that I do that up against. And then I can say that, well, I’m, I’m saving, I’m saving 50, 000 by doing this, these two people at the same time, but I’m, I’m trading off 25, 000 in like life. Yeah. Yeah. In, in like early spend. Yeah. Right. Allen Hall: Right. Yeah. That’s the part that that’s the missing variable. And a lot of these equations is how much am I going to lose if I don’t do it? Yeah. And then, Allan Larson: and then that plan can change because then suddenly something happens that makes that someone, someone ran into a gate, right? That’s part of it. Allen Hall: Isn’t that the fight right now. If you look at an O and M building and you talk to the site supervisors, they’re held financially accountable for everything that happens on site. So they have to go get approval, especially when you’re talking about bearing replacement, gearbox replacement, anything involving crane. The big thing is the crane. Is, is, is you have to get approval up the chain and, and those people up the chain want to have a better understanding of why, why now? That’s usually the most important one. Why now? Why can’t I wait six months so they can combine it with another project? Or whatever they’re trying to do, right? There’s a lot of complexity to this. Allan Larson: Here you can present them with a strategy they can choose. Allen Hall: Yeah. Allan Larson: So if you have this fly buzzing around in my eye and my nose constantly and I don’t know why it’s Is it also you? It’s like Joel Saxum: turbine problems. They just don’t go, they won’t go away. Allan Larson: Rule. Um Um Do you want a high risk strategy? Because then we can run it into the high risk zone. Right. Right? Visual framework. You know the risk you’re taking is, uh, it’ll suddenly, here there’s a high risk that it’ll suddenly get to the stage where it can’t run anymore. And so, then you have two months of downtime. Because that’s our typical lead time for ordering a main bearing. Allen Hall: Yeah. Allan Larson: Right. Allen Hall: Yeah. Okay. Allan Larson: So yeah, I can clearly communicate it. And that’s the whole point of what we’re, what we’re trying to do. Joel Saxum: I’m going to ask you an overreaching or overarching question about the CMS product, like that SkySpecs is producing for the market right now. As we know, like most, every, every turbine that comes off the line is going to have some type of CMS that the OEM can monitor it, whether it’s under FSA or under warranty period or whatever, your CMS product is a built in It’s not a bolt on sensor, it’s not external sensors, it’s just taking data streams. It’s Allan Larson: just a software. Joel Saxum: So it’s just software, but it’s, it’s for an operator that maybe Running the site by themselves or running it with an ISP or even running it as an FSA with the OEM But they want to have their own eyes on what’s going on. Correct. So it’s like it’s because the Whoever wants to get control of that CMS that’s in the turbine. That’s not the OEM doesn’t get it Like that’s just not they’re not gonna get it So you guys are the option in the aftermarket to be able to give them the eyes and ears of that CMS. Allan Larson: Yeah In general there are three Three operating modes for like live monitoring or continuous monitoring. As we see it, there’s a, for the really big asset owners that have the in house engineering capabilities to do it, we can offer the software, they use the software, right? But they can then reduce the complexity of how they monitor because they could do it all from one software instead of five, one for each hardware, right? Allen Hall: Right. Allan Larson: The second thing is you might not have that internal expertise. Maybe you just have one mechanical engineer that oversees suppliers that deliver stuff into your fleet. They maybe help prioritize and stuff and like channel stuff to the site and so on. And there we do a service. We do the monitoring. Um, and, um, and there’s also a journey there where we support the in housing journey a lot. That’s, that’s kind of how we position ourselves as well. We, the companies that are just on the edge there, They want to in house it. We offer a flexible model to do that. The final model is that, and that’s, those two first ones are specifically for self performing sites and self performing. Right. As if you have an FSA, you’re right. You need that second pair of eyes because, um, and this is not to do OEM bashing. I know, although I know you love that, is, uh, the OEM is monitoring, monitoring. Tens of thousands of turbines, maybe 20, 30, 000 turbines that they have full scope services for. And I can guarantee you, your top priority site is not their top priority site. Right. Exactly. So how do you drive action? You drive that by actually knowing what’s going on. Allen Hall: Yep. Allan Larson: And it’s not about, it’s not about that. You have to get like some sort of gotcha moment with the OEM. You have to be a good partner to them, right? Because their site operations are also struggling. It is also sometimes a bonfire, a dumpster fire of side operations. And they’re struggling as well with the right resources and their internal priorities and stuff like that. But you can be a good partner to them if you know what’s going on in their turbine. Allen Hall: Oh, sure. And it’s the same thing with Allan Larson: performance analytics and other things as well. You want to be a good partner to the OEM, a strict, a firm partner. That knows how to drive your priorities, but you can’t do that without transparency. And so shadow monitoring is something that’s really on the rise in the industry right now. And actually also a lot in Europe. Allen Hall: Oh, I can imagine. We’ve seen it a lot more in the United States in the last two years, I would say. The shadow monitoring, because they’re trying to understand what they have purchased. Yeah. And they have another 10, 8 years or so of operating it. So they’re trying to get some insights before the warranty runs out. And even if they have an FSA, they’re really trying to validate it. And that’s what mostly happens in Europe. So that makes total sense. So the Verizon CMS approach is getting adopted more widely now, I would assume. Operators are becoming more aware of the situation in which they’re in and need help. Allan Larson: I don’t think anybody in the future is going to buy a sensor system specific software. Right? That’s going away. Yeah. And, uh, and, uh, and I think the sensor manufacturers out there that haven’t adopted this on their roadmap, they’re going to lose out in the market. Allen Hall: You’re seeing the essential manufacturers deliver API so that the data can be pulled into a system like Horizon CPS. Allan Larson: Yes. Yeah. Allen Hall: And that’s the right approach. And if, if, if an operator out there that. It has this issue and I, I don’t know of one in the states that doesn’t have this issue right now in terms of CMS and trying to understand the data and then look at remaining useful life. How do they get a hold of you, Alan? How do they start picking your brain and saying, Hey, explain to me this Horizon CMS system and how it all works and how do I integrate it into my platform? Allan Larson: Um, Find me on LinkedIn or they can just go to SkySpecs. com and look up. Well, that’s easy. That’s easy enough. That’s easy enough. Uh, you know, uh, carry a pigeon, uh, owl, owl, whatever. You’re, Allen Hall: you’re based in Denmark though. I’m based in Denmark. Yeah. Yeah. You’re not, you’re not in Michigan like the rest of the Sky Specs team, but no, that’s, you know, it’s good to bring in. But I speak to a lot of Allan Larson: US asset owners as well. That’s a big part of my job is to. Speak to customers and talk about the solution we have and understand their problems and challenges. Allen Hall: Alan, we’re going to put your LinkedIn information into this podcast so people can find you. Uh, this has been a really fascinating discussion. Uh, as SkySpecs pushes into new areas like CMS and Drivetrain, it opens up so many opportunities and it’s good to know that smart people are working on these projects like you. So I appreciate you being on the . I appreciate you being on the podcast. Of course. Course. And thank you for joining us. Allan Larson: Yeah. And it was cozy here, right in our drone hanger in an, it was a, a good setting for this. Yes, it is. Well, thanks for, thanks for having.…
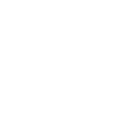
1 GE Vernova Closes Brazil Factory, Decommissioning Bonds for Wind Farms 36:25
36:25
التشغيل لاحقا
التشغيل لاحقا
قوائم
إعجاب
احب36:25
GE Vernova closes a Brazilian blade factory as installations drop 30%, while Australia faces issues with trailing edge serrations falling from turbines. Also, cultural differences between European and American work environments, blade recycling challenges, and the need for decommissioning bonds as the industry matures. Fill out our Uptime listener survey and enter to win an Uptime mug! Sign up now for Uptime Tech News , our weekly email update on all things wind technology. This episode is sponsored by Weather Guard Lightning Tech . Learn more about Weather Guard’s StrikeTape Wind Turbine LPS retrofit. Follow the show on Facebook , YouTube , Twitter , Linkedin and visit Weather Guard on the web . And subscribe to Rosemary Barnes’ YouTube channel here . Have a question we can answer on the show? Email us! You’re listening to the Uptime Wind Energy Podcast, brought to you by BuildTurbines. com. Learn, train, and be a part of the clean energy revolution. Visit BuildTurbines. com today. Now here’s your hosts, Allen Hall, Joel Saxum, Phil Totaro, and Rosemary Barnes. Allen Hall: Manufacturing capacity in the wind energy sector continues to contract as GE Vernova’s LM wind power continues to grow. Plant down in Brazil is being closed and that affects about a thousand workers, Joel. And it’s coming because the demand in Latin America for GE, Vernova wind turbines and all them products is diminishing quite a bit. Now it’s also part of a broader trend down in Brazil where installations have fallen by about 30 percent in 2024 compared to previous years. So there’s a big slowdown in Brazil. And. GE, Vernova, slash LM are ceasing operations there. I don’t see how this is going to last very long. There’s a number of operators that are coming into Brazil, especially Chinese manufacturers. You think this factory will get gobbled up like some of the other ones that LM has closed recently? Joel Saxum: Yeah, I think this one, we heard about this whisperings of this. We before it happened, we’ve got some pretty good connections down in Brazil. With some people that are in the factories and it is, it’s just following that trend. I think one of the interesting things about the Brazilian market as well is that, A lot of big turbines down there. People may not know that, but the majority of turbines, I think, are over like three megawatt machines. They’re big down there. They don’t have a whole lot of legacy old stuff like we do here. So there was this big ramp up to create all these bigger blades down there. Of course, making those big blades locally saves a lot of logistical costs. But you’re going to see this changeover, right? Like in the States, we don’t really, we don’t allow the Chinese manufacturers to come in. And in Europe, they’re not really allowing the Chinese manufacturers to come in, but in Brazil, they’ve been all over the place. And to be honest with you, some of the big asset owners down there have to, They’re not just Chinese OEMs. It’s Chinese owned asset owners like CGN and things like that. So there’s a, there is a big tie to China and I believe, like you said, Alan, I think this a blade factory is a kind of a pain to build. And one that’s just sitting there and all you really have to do is, Build some new molds and repurpose a couple of things and you’re ready to roll. I think this will get scooped up pretty dang quick. Allen Hall: Yeah, which should be good news for the employees down there because there is still a need for people who know how to build blades that are hard to find right now. Now, Phil, is this a broader move by LM that they’re going to be closing some of the factories because of GE’s demand more recently? Phil Totaro: Yes, and let’s keep in mind too that, GE stopped selling their turbines down there and that LM factory was largely just producing blades for Vestas V150s. It looks like it might be rough sledding for for some of the folks at LM. The good news is, so going, pivoting back to Brazil for a second, they’re suffering a little bit from some of the in 2024, they terminated the guarantees that the independent power producers got for curtailments. And that’s also what kind of led a lot more investment in, other forms of power generation solar displaced, some of the wind, hydro displaced, some of the wind And, we just couldn’t get enough wind contracts to make that a worthwhile market. So you’ve seen a massive slowdown across the board. It is likely that a factory like that will be gobbled up by somebody like Goldwind or, Sonoma has been poking around the market. They’ve already got one factory. But why not Look at a second one in a market that just like China takes advantage of cheap labor and has reasonably good access to raw materials down there. They can also start using that as an export hub. Should they need to. Joel Saxum: Phil, what do you do? Okay. So let’s just take the broader context of Brazil. Now I know we’re talking about building blades here and the export markets and all these different kinds of things, but in Brazil. What has to happen for, basically, 30 new wind farm installations down 30 percent in 2024. What has to happen to get that back up on pace? Is it what we’re sitting here like ERCOT, right? I was just talking about this a little bit ago off air, but batteries, do they have to get batteries in to avoid this curtailment issues? And does that make sense for you? economically down there? Phil Totaro: Potentially, yes. And the, I guess the reality of it is that either they need to go back to the old law, which basically gave, a certain amount of payment to the or certainty, at least to the independent power producers that they were going to receive some type of compensation when they were being curtailed. They’re still, potentially exposed to if they’re not largely on a merchant power market down there, it’s mostly fixed price offtake at least as part of the auctions that they’ve previously had but they just had an auction down in Brazil and there was no wind that was even bid into the auction. Because nobody wants to build wind farms down there right now. So it’s something has to change. Storage would help. But it’s not a cure all necessarily for a larger fundamental issue down there. I was going to ask Allen Hall: about that swap over to TPI, because TPI is going to open or is opening their facility in Iowa. And is that part of the move with Brazil closing? They don’t really even need it if Iowa is opening and TPI is going to be the main source of blaze over the next couple of years. What happened, Joel Saxum: but it but a blade factory TPI I think if you’re GE you’re looking at it like we it’s a little bit closer to home Of course, we can control QA QC a little bit better. We can it’s we can take some trips from Schenectady or trips from North Carolina up there, South Carolina. Sorry Greenville a lot easier And then you’re serving your biggest market right your biggest market of course for GE is the US and Canada And so everything’s close to home here. You’re going to be able to knock some things out, buy a factory in Iowa. It may not be you know, that perfect optimization economically, but the things that you’re going to make up in QAQC and cost support quality and these other kind of logistical issues, I think that’s a winning move in my mind to give more to TPI. Phil Totaro: Yeah, you also face the logistical cost and time, frankly, of, even though you’re getting cheaper capex on blades that are manufactured in a low cost market like Brazil, You still got to get them up here and if somebody needs a blade fast, they’re going to get it faster from Iowa than they are from anywhere south of the equator. Joel Saxum: As busy wind energy professionals, staying informed is crucial. And let’s face it, difficult. That’s why the Uptime Podcast recommends PES Wind Magazine. PES Wind offers a diverse range of in depth articles and expert insights that dive into the most pressing issues facing our energy future. Whether you’re an industry veteran or new to WIND, PES WIND has the high quality content you need. Don’t miss out. Visit PESWIND. com today. Allen Hall: There’s more safety concerns down in Australia as Australia’s largest wind project lost a set of trailing edge serrations from a Vestas wind turbines at the Golden Plains Wind Farm, which is down in Victoria. It’s the second time that trailing edge serrations have fallen off at this facility. And the site is a little under a year old, right? It’s about six months old, roughly which is creating all kinds of problems. Now, I’ve seen trailing edge serrations come off if you’re driven around the Midwest, where they do occasionally use serrations. You do see them missing from time to time. I guess my top concern wouldn’t be safety on those Joel. They just don’t seem, they’re not that heavy. I wouldn’t like to get hit in the head with them, that’s for sure. But the panels themselves are not particularly large or heavy. They’re going to Mostly flutter down to the ground, but it does raise concerns like it’s stuff falling off of turbines. What’s going on? And what are the probable fixes for it? Joel Saxum: I think to be honest with you a young wind farm like this losing Serrated trailing edge pieces right to me. That is something that happened in construction, right? They put like when these when these things are moved they put those Kind of yeah, transport like socks over some of them to keep them in place. And then you got to pull that whole thing off. And I think that they probably got the glue, got cracked, messed up, something got peeled up or whatever in that process. So to me, this is a, it’s a construction issue. It’s a quality issue at that level, right? That should be found. Or it’s a lifting problem at that same point in time, a strap or something like that, or, blocks on a crane could have broken these things, but it’s. Not enough QAQC during that construction process. And it just, it points to that they put in the press release. Storms on February 2nd, wind speeds reach 64. 8 kilometers an hour. That’s only 40 miles, 40 miles an hour. If 40 mile an hour wind, that’s not I would say that’s not a serial issue. That is a damage issue. So it’s frustrating to see that, right? Because these are, again, more kind of black eyes on the industry that shouldn’t be there. We shouldn’t have this stuff. This is pretty simple. Walk down the blade and make sure they’re all in place before you fly it. I guess that’s my take on it. Allen Hall: Yeah. There are signs before they come off. Usually they don’t just all of a sudden pop off. They tend to peel slowly over time and then bow is what I’ve seen. Now, if times are different and maybe it’s just different adhesives are being used and it’s all. I could see some design changes happening because of this or logistical changes, right? The transport is probably the problem. But why Joel Saxum: don’t we see trailing edges? And maybe this is a more of a rosemary question. Why don’t we see trailing edges like as a part of the mold process? Like in the, in sandwiched in the trailing edge? Is it because of the molds? Allen Hall: That’s a pain in the butt to do, right? But, LM, Phil and I have talked this on PowerUp, that LM has designed some more recent blade shapes that basically are quieting. They make that trailing edge longer. So instead of having trailing edge serrations, they’d extend that trailing edge out and change the shape a little bit. To quiet the blades down. So in reality, you don’t need to have the trailing edge serrations, which I think would be the way to go because less stuff on a blade means less things that are going to fail. That’s a better solution overall. Joel Saxum: Yeah. Or what about this? Make that trailing edge longer, right? You, so you make like basically a duck tail trailing edge, like you’d have on the back of a suit jacket and then go down and go clip, and clip the trailing edge or cut the trailing serrated edge into that long thing. afterwards, right? Phil Totaro: Yeah, no you could absolutely do that, but that’s the manufacturing complexity is really the reason why it doesn’t happen at least at this point. The other issue again, being, if you’re going to do that and do something where these are either factory Fabricated like you’re suggesting or the way it happens right now, which is they’re usually factory installed because they don’t want to spend the time doing a field installation on certain trailing edges once they get them to the site then it’s absolutely a quality issue, but it’s funny enough one of the things that came out two of the things, that came out of the recent Australian, wind energy on M event we did was a, you’ve got a bit of a different market down there in Australia where there’s a lot of, competent people, but they aren’t necessarily the ones, particularly the people doing like a lot of the EPC work. They aren’t necessarily the ones who were working for the, owner and operator, they may have been contracted. And even if the OEM was contracted, they were likely subcontracted and may not have the requisite experience with, how to transport, how to properly inspect, or even how to properly lift these, the blades. The second thing that came out of that was we had somebody come in from EnergySafe Victoria and talk about all the fines and penalties that people are having to pay now for having the, even little things, like having a Chunk of serrated trailing edge fall off the blade. That’s a fine for, the wind farm owner. So everybody’s going to have to start taking it more seriously moving forward because they, now it’s starting to hit them in the wallet. As opposed to, it’s just a PR problem, and they’re gonna pay a lot more attention to it from now on, I guarantee it. Joel Saxum: It’s a good thing they don’t have very much ice and snow in Austria, because if that, if every time something came off of a turbine, they got fined, you’d have a hell of a problem during ice storms. Dealing with damaged blades? Don’t let slow repairs keep your turbines down. Blade platforms get you back up and running fast. Blade platform’s truck mounted platforms reach up to 100 meters, allowing for a quick setup, improved safety, and efficient repairs. Book soon to secure your spot and experience a difference in blade access, speed, and efficiency. Visit bladeplatforms. com and get started today. Allen Hall: I don’t know if you’ve scanned Reddit once in a while, but there’s some pretty interesting discussions there. But a recent article that actually came from Reddit was about a German professional who was relocating to the United States with his wife, who was an American. And this German citizen described the transition from the Germany’s pay time off and work. culture to America as being a real huge shift, big culture shock, right? And a lot of it has to do with just basic labor practices between Europe and the United States. Since I do think there’s going to be a number of professionals that will be coming to the States this summer for the wind industry. At least that’s what it seems to be right now. Either be blade work or engineering work. I think there’s a lot of opportunities in the States. But there are big differences between what happens in Germany, what happens in the United States, right? Obviously Germany’s work week’s a little bit shorter and. And with has a maximum limit of 48 hours and like pretty much every airplane company I’ve ever worked for, 48 hours tends to be the minimum we would always work, right? That’s the bottom end. Like you have to work 48 hours or it doesn’t count. Okay. And also the pay time off, right? So there’s a good bit of pay time off in Germany. What is it? Six weeks of paid sick leave policy versus essentially zero in the United States. So it is a huge culture shift and as people come over I always think Better pay attention to those things because the work life in America is not the work life in Europe at the moment. Be prepared and adjust accordingly. Ask for the right things. And Joel, as we were over in Australia, I thought we saw that some of that different cultures and different the way employment is handled and The pay time off and those sort of things. We ran into a couple that were talking about, yeah there’s leave for having a child in Australia, but there is not in the states at Joel Saxum: all. I think that comes with quite a few things is like an American export import too. Like you would think that the common thought is like, oh, an American usually will have a harder time going abroad. Whether it’s for business to business purposes, or P to P, B to B, whatever it is, or going to a different culture, integrating. But what I’ve found in practice is actually it’s easier for an American to go and assimilate and work within and live within other cultures than it is for other people to assimilate. Wherever you come from to come to the States and integrate in and live and work in our culture. And a lot of it is this, these things, right? When I went to work for the Danish company, you go over there and it was like certain hours of the day, like you’re done. Like I remember being at the office at seven o’clock. Cause I’m like, all right, let’s get some stuff done. And nobody showed up until nine, two hours they’re sitting like, Oh, drinking coffee downstairs. Cause nobody was there. So that’s, that’s a small thing, but. We see this in like the sales efforts among companies too, in wind. For people to come say a Danish company, a German company, a French company, trying to come and sell into the United States is very difficult for them because of the way that we do business, the way that our work culture works. And part of it is that, You come to the field to get stuff done. Like I’ve been a part of these, go out to the field to get things done. We’re doing a demo of a product as an American, like we’re there until we finish, right? We’re going to get that. We’re going to get yeah, if we’re here for 12, 13, 14 hours and we’re fixing code in the truck and charging batteries on the fly, like we’re going to make sure this robotic thing or this drone or whatever this product works. And I’ve also been a part of that exact same process in the field. Denmark with Spanish companies and stuff where they’re like, Oh, we’ve been out in the field now for six hours. Like we’re done. What? We have a day to do this. It didn’t work. So I guess we’re going to go back to wherever we came from. Allen Hall: That same difference exists in like the handling of tools, right? How many A lot of times we’ve talked to training schools over in Europe about how many hours you can have a vibrating tool, like a grinder. And we have no requirements about that at all in the States, or I don’t even know if Canada does. I don’t think they do either. No. Joel Saxum: It carries on with some of the political conversations that are happening around the world right now with the difference in regulation. Like this, the idea that, I did not know this, I’ve never heard this before, you said a legal maximum of 48 hours of work in Germany. You’re not going to get anything done in 48 hours. Man, when I was working in the oil and gas world in the field, man, 100 hour weeks happened regularly. Like it was, that was, it’s not crazy. It’s not out of line, like putting in 16 hours a day, like that just happens. That’s, it’s not something crazy. I guess if you put 16 hours a day and you’d be done with work by Wednesday, like that’s not a bad gig, Allen Hall: yeah, but that you would see that in States, right? People would love to take those extra hours. You’re going to pay me for a hundred hours. Let’s go. Joel Saxum: Yeah, Allen Hall: for sure. Yeah. So as things pick up over the summertime and there will be a number of people coming over from Europe to work in the States. Thank you for doing that. Just be prepared, plan ahead, and ask the questions about what is PTO and yeah, what’s time off look like and what does a work week look like so you can get yourself prepared for it. Lightning is an act of God, but lightning damage is not. Actually, it’s very predictable and very preventable. Strike Tape is a lightning protection system upgrade for wind turbines made by WeatherGuard. It dramatically improves the effectiveness of the factory LPS so you can stop worrying about lightning damage. Visit weatherguardwind. com to learn more, read a case study, and schedule a call today. Allen Hall: We were talking about recycling over in Australia and Rosemary jumped into the middle of a discussion about that and said, I don’t think recycling of blades is a good idea. And I, I could hear the, Pindrop in the auditorium. Like what? Rosemary said what? Yeah, recycling of blades is not the most energy efficient thing to do. Bearing of blades tends to be the most efficient thing to do. However there is a big push to recycle blades and Axiona is actively involved in recycling blades over in Australia at the minute. And they unveiled a program called Turban Made about transforming the decommissioned wind turbine blades into new products. And if we previously remember, Axiona was involved with Elganzo, which is a company that makes sneakers and making wind turbine blade, recycled wind turbine blade pieces or granules, into shoes. Basically and Phil, I know you and I had looked for them to see if we could actually find a pair of them. I don’t know if they actually produced them or not, because I did go after and looked at them, and there were pictures online in the store, pictures online of those shoes. Never could find a pair. But in this particular case, they’re looking for off take. That they’re trying to find places where this ground up material from blades can be used. The big one, I think, in Australia is going to be road services, right? That’s probably the easiest place to include it to make the road services better and last longer? Phil Totaro: In all likelihood, yes. And that’s building on pilot projects that have been done in the U. S. And I want to say one in Spain, but also recently China. Just started doing that as well with some of their recycled blades. So it’s likely that’ll be the the primary use of it. The, but they’ve also ground up blades to use in concrete mix and things like that as well. So there’s if you don’t mind the energy inefficiency that, that Rosemary is complaining about and you still want to be able to use, the recycled material, then that’s probably going to be the most prominent uses of it. If they ever decide to make those sneakers maybe I’d. Check them out. But I, I did go online and don’t seem to be in stock. So I don’t know if that ever happened or not. I found out Joel Saxum: if you’re if you can get a, yeah, if you can get a Euro size between 41 and 45, which I think is like a nine to an 11. Yeah, it’s between an 8 and an 11. 99 Euros, Phil. There you go. Allen Hall: So is this going to be an efficient process over in Australia as they define it? Or is it going to get oversight? Australia’s pretty smart. Talked to a number of people over there in the last week or so. They tend to know what the environmental costs are. I’m a little surprised that this is going to move forward. I, I, Good on Axiona for trying to take care of all these blades that are going to come offline, but are there any other opportunity here besides grinding? I think burning is off the table, I hope. Phil Totaro: Probably down there, yeah, I would think. But that’s, it’s a good idea, though, to use them in I, why we don’t use it in, Like the roadways for project sites too, like we could, instead of just having dirt, it’s slightly more expensive than just having dirt roads, but, if you actually have something where you need some reinforcement beyond just dirt this would be stronger than dirt, not quite as strong as, a paved roadway, but it’s It’s a decent alternative and something that allows you to take advantage of the recycled material if you have it available. Again, we’re not Rosie’s not here, so I guess we’re not having the debate about total cost of ownership today, but if you’re gonna, if you’re gonna recycle blades just cause you want people to think you’re, being, environmentally friendly with recycling, then, you got to do something with that, Allen Hall: ground up material. Yeah, it gets back to the article I wrote on Substack a week or two or three ago. I forget how long ago I wrote it, but it had to do with decommissioning of blazing towers and all that and not having any real requirements in the United States to deal with it. And there was that situation that happened in Iowa where the two turbines in the being decommissioned and sitting there and getting hit by lightning and then catching fire and then subsequently being knocked over and what a mess that is. There’s a huge difference between an active recycling program and no program at all and I, at least the Australians in Acciona have a plan because right now in the states it is a little helter skelter, gotta admit. Joel Saxum: Do we know if there’s any little states that have a bond, a state bond? Decommissioning bond for wind farms. Allen Hall: I think Iowa is going to have one here very soon. And other locales will soon enough. Because of the problem that happened in Iowa. Yeah, Joel Saxum: because Texas has a huge bond law for every oil and gas well. Now, it’s a joke, right? It’s a write off for the oil and gas companies. They just pay it and they’re like, This is a cost, this is like a permit to do work. Because the bond fee is not nearly enough to remediate an old well. And then those wells are changed hands ten times, and then the last person goes bankrupt, and then all of a sudden there’s just a well in the ground, and the remediation fund has got a hundred grand in it or something, right? It’s not enough to do it. But I think that, That’s if we don’t have any states that have it yet, I would see that coming down the pipeline very shortly. Allen Hall: Ask yourself this question, Joel. I have this bond, which is basically money set aside to go do the reclamation project. Who is the person that’s going to do that reclamation? It’s a private contractor. The town would run a project. So they would have the money to go do that, but then they’re in the middle of it now. I’m not sure they want to be in the middle of it. Joel Saxum: Yeah, but at least if nobody’s going to take care of it. Then someone has to. This is the same problem that’s in oil and gas. Someone’s got to take care of it. So then it would be like, I’m XYZ County in Oklahoma. We’ve got this wind farm and I have now, I have this bond. So I’ve got 10 million bucks sitting here. Then I’m going to go out to bid. Hey, private companies come and bid on this thing and lowest bid gets the lowest qualifying bid, whatever, gets to work. And most likely, more than likely, the idea would probably be go energetically fell these things and just clean them up. Get him out of here? I don’t know. Phil, what do you think? Phil Totaro: To start off, yes, there aren’t any states or counties that as of yet are actually mandating the a bond, a decommission bond. However, landowners have and, some landowners, especially for actually some of these dilapidated assets because they’re sitting there with a dilapidated asset on their land which they don’t want. They’re mandating that if the site gets taken over by somebody else, that new, um, project owner signs a lease extension with the owner, they put a decommissioned bond in the new lease that gets executed so that’s already happening, but it’s not a legal requirement. Yeah, but it just comes down to, going and finding yourself Everpoint services or, name your other favorite company to do the actual work. There’s plenty of companies out there that’ll do it. But they obviously get paid and not just Hey, we’ll take this down for you and then sell off the scrap metal and whatever else we can get money for. They expect to have somebody that’s got a decommissioned bond that they can get paid for their time in, in doing this. And then some of that cost gets offset by, what they sell the scrap for. Allen Hall: Let’s go one step further because I think Joel. You and I have talked about this a little bit. Some of these recycling places of old where they’ve have a whole bunch of blades stacked up in a field and that business has gone bust tax entity, which would be the town or the city eventually takes her the facility and goes, I’ve got all these blades and I don’t have any money to deal with this mess. Do you think you’re going to start seeing bonds on the recycling facilities? I think that’s where the. Bigger problem lies at the minute because we have had a couple of lawsuits between OEM and one of those operators. It’s percolate a little bit. There’s a lot of discussion about that. And and towns don’t wanting, not wanting to have those recycling centers in their proximity because they don’t want to have to deal with it. If it goes bust, the town and the locale are responsible for dealing with the consequences and they just don’t want it. Would that Joel Saxum: be able to qualify because of the, okay. So because of, say you grind up blades and it puts dust in the air, whatever. There’s some, there is some health benefits to that. Things here with grinding blades, of course, right? You can’t you gotta have watering systems, all this stuff. Would that get to the point where it would qualify as Allen Hall: a Joel Saxum: Superfund Allen Hall: site? I think in the big scheme, probably yes. But it’s construction material. Blades are dealt like Two by fours, basically the same thing. Drywall, they’re all dealt with basically the same way. However, I do think politically it would, there would be a rationale for political influence to call wind turbines hazardous debris. That would, I could see that happen politically. Not that it would be right, but I could see it happening because it would open a box to more federal funding. Sure, here’s the Fed, here’s, we’ll call it a cleanup site, here you go, here’s your two million dollars, go do it, because right now you can’t do it that way. Joel Saxum: But if you take anywhere that there’s a heavy oil field presence, let’s take Texas, Oklahoma Golden, North Dakota even, or the front range of Colorado, anywhere in Pennsylvania, like these places where there’s been oil field for a long time, when there’s booms and busts in oil field, when you drive down and you just see lay down yard after lay down yard, of equipment, of old pump jacks, of pipe, of all these different things. All of that stuff is sitting there, and those companies go bust regularly, right? That’s like oil, that’s a strategy in the oil field, to be honest with you. Go bust, remove this stuff, start up another one. But! Those are sitting there on in lay down yards that are mostly gravel, but those things have hydrocarbons and oil and other things, grease, and it’s raining and it’s getting into the dirt. So what happens there usually is whoever owns that site, it may change hands. They try to get whatever scrap they can out of the metal, and then they’ll end up having to go in there and scrape out, six feet of dirt and remediate it and that kind of stuff that happens quite regularly in the oil field the difference being if you take to take over a facility that has a bunch of blades or a bunch of root ends or whatever it may be the scrap left over there’s no real value in it right now. Like nobody’s come up with something that’s Oh, this is value ad where it’s cheap and I can make money on it. There’s all these things that are like recycling initiatives, there’s, which is great. The energy argument that Rosemary has, of course, very valid in the situation, but. You’re not going to go and take over this facility and be like, Oh, I got all this value in these turbine lights. No, you’re screwed. You’re not going to take over that. Nobody’s going to take that facility. It’s going to be sitting in the hands of the government because, or whoever, the tax liens on it or whatever, because nobody’s going to want it. There’s no value in it. So yeah, we’re at a weird, like it looks like industrial waste, industrial facility, industrial lay down yard, but it’s not the same as the other things out there in the market because there’s literally no value in it. It has to be bonded. I think it’s gotta be. Allen Hall: So the problem recycling blades may not be the recycling part of itself. It may be trying to get a bond to hold them where you can break them down. That may be the bigger problem. So getting bonds on the turbines themselves to take the turbines down. Yes. I think that’s inevitable. But who’s going to hold that bond and who’s going to be the one responsible to do that work? Taking a couple of turbines down and say it was a hundred turbines. Big deal, but not overwhelming impossible. Taking up a hundred acres of recycled or unrecycled wind turbine blades and trying to do processing on them and get them out of there is monumental. Huge cost. Millions and millions. The wind Joel Saxum: farm of the week this week is Cooper’s Gap Wind Farm is owned by Tilt Renewables. And this one is an honor of us being down in Australia last week for the wind energy O and M conference. And also shout out to Tilt for letting us use their office to meet in. But the Cooper’s Gap Wind Farm is a, it’s a big one, 453 megawatt wind farm. It’s in the Western Downs and South Burnett regions of Queensland. So it’s about 175 kilometers Northwest of that state capital Brisbane. So this is the second Greenfield project developed by Tilt. They did it in a cohort with AGL, which is another big operator down in Australia. So it has enough renewable energy at Cooper’s Gap they’re creating to power almost 280, 000 average Australian homes. So these are big GE machines at this site. There’s 123 of them. The project cost about 850 million. So it was completed in 2020. 200 construction jobs were a part of the project, and 20 jobs once operational will be full time. AGL, of course, like we were saying, another operator down there, they are purchasing all of the power from Cooper’s Gap. And an interesting thing here, when I’m looking for Windfarm of the Week, I always like to look at what public data is available about a wind farm and these are things that we learned being down in Australia for the wind O& M conference. There is a ton of public engagement in the wind farms down in Australia. So they have literal maps of the decibels for the sound emitted and who’s a part of participating. Part of the project is a landowner and who’s not and you can see where they moved the design of the wind farm to eliminate noise For people that are not a part of the wind farm a landowner is not part of the wind farm very cool stuff And when I say information that you can find online You could spend a week reading about the Cooper’s Gap Wind Farm and all of the different reports and consultant reports and government reports about this wind farm before the construction, during the construction, and even after the construction. So for all of this amazing reporting that’s done in down in Australia, the Cooper’s Gap Wind Farm you are our Wind Farm of the Week. Allen Hall: And that’s going to do it for this week’s Uptime Wind Energy podcast. Thanks for listening and please give us a five star rating on your podcast platform and subscribe to our sub stack channel, Uptime Tech News, our weekly newsletter, and we’ll see you here next week on the Uptime Wind Energy podcast.…
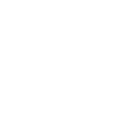
1 Xcel Energy Retires Coal, €16B for EU Wind Projects 3:06
3:06
التشغيل لاحقا
التشغيل لاحقا
قوائم
إعجاب
احب3:06
On News Flash this week, substantial investment for renewables across Europe by the European Investment Bank, Octopus Energy’s “The Collective” proves a success in the UK, and Xcel Energy plans to eliminate their coal power plants in the US Midwest by 2030. Fill out our Uptime listener survey and enter to win an Uptime mug! Sign up now for Uptime Tech News , our weekly email update on all things wind technology. This episode is sponsored by Weather Guard Lightning Tech . Learn more about Weather Guard’s StrikeTape Wind Turbine LPS retrofit. Follow the show on Facebook , YouTube , Twitter , Linkedin and visit Weather Guard on the web . And subscribe to Rosemary Barnes’ YouTube channel here . Have a question we can answer on the show? Email us! Allen Hall: Starting off the week, the European Investment Bank is making bold moves to accelerate wind energy development across Europe, signing significant agreements with both BNP Paribas and Banco Satandier. These partnerships will generate up to 16 billion euros in wind energy investments through innovative counter guarantee agreements. The initiatives are part of the EIB’s broader 5 billion euro wind power package, demonstrating Europe’s commitment to renewable energy expansion and industrial competitiveness. The deals will enable manufacturers to receive advanced payments and provide performance guarantees for new wind projects, while also supporting supply chain efficiency and grid interconnections. This financing structure is backed by Invest eu, the eus ambitious program aiming to mobilize over 372 billion euros in investments by 2027. 2400 onshore wind turbines representing 14 gigawatts of capacity. While the upcoming election has introduced some uncertainty with skepticism from leading parties, Industry experts still remain optimistic. The CDU, likely to lead the next government, is expected to maintain support for wind energy given its reliability and cost effectiveness in producing clean energy. Over in the UK, Octopus Energy’s groundbreaking investment platform, The Collective, has demonstrated remarkable success with its first two wind projects selling out within just one week. The platform democratizes renewable energy investment by allowing public participation with investments ranging from 25 to 20, 000 with no fees. Located in Yorkshire and Wales, these projects attracted hundreds of investors. And the company is now expanding to expand the platform through its Pass the Power campaign, inviting more renewable energy projects to list on the platform. And in the United States, despite challenging political headwinds, Xcel Energy is making significant progress in renewable energy deployment in the Upper Midwest. Their ambitious plan includes adding 3, 400 megawatts of wind energy and 550 megawatts of solar power. The company aims to retire all coal plants in the region by 2030 and potentially reduce emissions by up to 88 percent compared to 2005 levels. The plan also includes innovative energy storage solutions including testing new iron air battery technology at their Becker site. That’s this week’s top news stories. Stay tuned tomorrow for the Uptime Wind Energy podcast with Rosemary Barnes, Joel Saxum, Phil Totaro, and me.…
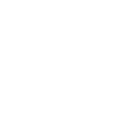
1 Wind Tech Training Excellence at Deutsche Windtechnik 28:03
28:03
التشغيل لاحقا
التشغيل لاحقا
قوائم
إعجاب
احب28:03
Momme Feddersen and Russ Leach from Deutsche Windtechnik discuss their innovative training programs for wind turbine technicians. Momme, as Head of Training Center, and Russ, as Director of Quality and Ops Support, explore how the company is tackling workforce challenges through apprenticeships and advanced training methods in both Europe and the US. Fill out our Uptime listener survey and enter to win an Uptime mug! Sign up now for Uptime Tech News , our weekly email update on all things wind technology. This episode is sponsored by Weather Guard Lightning Tech . Learn more about Weather Guard’s StrikeTape Wind Turbine LPS retrofit. Follow the show on Facebook , YouTube , Twitter , Linkedin and visit Weather Guard on the web . And subscribe to Rosemary Barnes’ YouTube channel here . Have a question we can answer on the show? Email us! Allen Hall: Wind Energy is facing a critical workforce challenge, finding and retaining skilled technicians to maintain the growing fleet of turbines. This week we speak with Momme Feddersen and Russ Leach from Deutsche Windtechnik. Deutsche Windtechnik is setting new standards for technician development through their comprehensive training programs, combining hands-on experience with cutting edge technology. Welcome to Uptime Spotlight, shining Light on Wind Energy’s brightest innovators. This is the Progress Powering Tomorrow. Allen Hall: Momme and Russ, welcome to the Uptime Wind Energy Podcast Spotlight. Momme Feddersen: Thank you. Good to be here. Thank you so much. Allen Hall: Well Deutche Wind Technique. Has always, to me, been a really high standard in terms of a company. But that comes through training. And Deutsche Windtechnik spends a great amount of time and energy on the training side. I want to talk to some of the challenges that are out there first, and what are some of those challenges that exist in training wind turbine technicians today? Russ Leach: Yeah, so they’re the same ones we’ve had since my entire time in wind. It’s finding the qualified personnel who are ready, available to climb that turbine and do great maintenances and great troubleshooting. The problem has been exacerbated with the growth of renewables with wind, right? They’re harder to come by. Um, And we’re all fighting for the same people, aren’t we? So that’s why we have our training programs, right? We have to start people out from nothing many times and build them up and get those competencies out there with them. Um, and, um, that’s the main challenge. Plus the distributed nature of the workforce, right? We’re, we’re across the country here in MoMA, they’re, they’re across Europe. And, um, so you have to put mechanisms in place to get the training to them many times and get them competent and, and verified as competent many times out where they’re at. So it’s a combination of Training facilities, which are very valuable, but also training that extends out to the field with the people themselves. Allen Hall: And Mame, let’s talk about the technical challenges because wind turbines have gotten more complicated. There’s more computers in them. There’s more electronics in them. There’s more cooling systems. How has that impacted the training of technicians? Did it just make it harder because there’s so much new things happening? Momme Feddersen: Here in Deutsche Windtechnik, we have to, we are focusing more and more on the, um, not on the, on the, on the MOOC. Highest moderns, tur, modern turbines, um, but more, um, on the older ones. So, um, but uh, when we look into the future, the, the topics you say are, are exactly the topics we have to, we have to face. Um, what what we did in the past was focusing on the practical side of the training and not focusing on the theoretical side. That’s why I think we did a. Kind of, um, interesting approach, uh, how we train here in Germany. Um, as you know, we are a multi brand, uh, company. We are servicing different brands. We are not focusing on Vestas or on Anaconda or something like that. We are, we have all of them. Also a challenge. And that’s why, um, we did that approach here in Germany, uh, what I think is outstanding in the, in the home. Allen Hall: And that comes with a unique thing that Deutsche Wing Technik does, is that you do have resources for the variety of turbines, which I think just makes this really complicated. Discuss the sort of the differences between what happens in Europe for Deutsche Wind Technique. Momme Feddersen: Yeah, we have different, uh, different, um, ways of training here in Germany. It depends on your experience. It depends on your age, on your, uh, on your skills you already got. Um, so for example, the, the people who are, who come directly from school, then they don’t know how to do it. So we have to start with, with the real basics. Um, our apprenticeships program, uh, starts when they are 18 years old, uh, directly from school. And they are in, in Deutsche Windtechnik for three and a half years, just with education, just with learning, just with everything. So, um, there are ways to shorten the time, but, um, yeah, you, you learn the basic. mechanic work in, in our training center, for example. Um, this is one way to learn it. The other way is when you have more experience, um, we got a level training for the people who are already working in the field. So we don’t stop working on ourself. We don’t stop educating ourself. Um, we have a level training from basic to level two or level three, where you learn how to troubleshoot very well. And the third one is the, uh, the, the career changer program. This is one of my favorite programs, I have to say, because these are people who are highly motivated. These are people who come from completely different fields, uh, uh, uh, in, in Germany, they all have, uh, uh, uh, uh, had a job before. So for example, they are plumbers, they are carpenters, they are something else. And in our training center, they learn, um, the real, uh, the, the, the, to be a wind technician, wind technician, they learn it in about six months, but only in the training center they are here for six months. And then they’ll go out and they start working what they learned here in the training center. And they did it and they do it then in the, in the field. And that’s my favorite program because, because the people. see this as a second chance in their life and they learn something completely new. Say they learn, um, to be an electrician. Um, and as you said before, the turbines are more and more complex. They are more and more, um, you have to be perfect in so many things. You have to be a mechanic. You have to be a technician, an electronic specialist. You have to be a Um, and yeah, so different things, so, um, yeah, it’s, it’s quite complex. Joel Saxum: That’s a stark difference from what we see in the United States because, um, and Russ, you can probably speak to this. You hear these, sometimes you hear horror stories from whether it’s an ISP, you know, OEM, it doesn’t really matter where it’s like, Hey, you’ve got your GWOs or even, you know, your equivalent of GWOs. You’ve been safety trained. You got a couple of tickets, get out in the field and now you’re expecting to produce. Uh, throw, thrown right into the fire. And, you know, from someone who grew up in some oil and gas worlds, that’s a tough place to be. That is a pretty , pretty, pretty stressful thing. Um, and so I know when Alan and I initially talked with the DWT team about the training, how it goes on in Germany, uh, it blew my mind. It was like three and a half years of, of actual. Really, uh, curating these technicians to get them to the point where they can get on their own in like three and a half years in the States. I’m thinking, that’s a bachelor’s degree. I’m at university. You know, that’s a really advanced person. Are you guys taking some of the, the lessons learned and the training and, and applying that in the States to your, your technicians here too? Russ Leach: Absolutely. We have our own apprenticeship program. We stood it up in May. Um, it’s a WIN Laborer. It’s part of the Department of Labor’s Office of Apprenticeship, um, under Construction Laborer. Really excited about it. Um, the model is MoMA and what they do over there. Ours is a two year. It’s a two year. Um, and it combines many of the same things. Um, we have our, uh, online learning. We have our in person training. It’s called Related Technical Instruction in the Apprenticeship World. And we got a heavy dose of on the job learning. It was structured on the job learning, well documented on the job learning that leads to competency verification. So, We’re really excited about it. Um, that, and it’s right now, it’s geared more towards the, uh, well, our existing training program. That was the beauty of it, right? We had our existing program that we just rolled right into a two year apprentice program. Um, but it’s geared more towards repower right now. What we’re doing in January, I’m super excited to say, is, is standing up one for O& M Techs. Probably be two year. And many of the same things, slightly different, um, around that too. So we have a structured learning path now for our people. Again, we had that already here in the U. S., right? But now it’s registered with the Department of Labor to their standards, with all the requirements for on the job learning. You need 2, 000 hours a year minimum on the job learning. You need 144 hours of what’s called related technical instruction, which is basically, Classroom type stuff, right? And, and certain structured, uh, um, competency verifications there. We got all that. It’s launched right now. And at the end of the day, they get a certificate that’s valid wherever, wherever they go. And, uh, and, and Momay mentioned life changes. We have something kind of similar to that too with veterans, with veterans. Um, we’re really excited to just get signed off on, uh, with the Veterans Administration to be a training facility where young men and women coming out of the military, can receive their GI Bill benefits while they’re earning money with us, their hourly rate. That’s huge, Russ. Congrats on that. Yeah, we’re really proud of that. We’re going to be bringing in a lot of veterans to us. But the main thing is, are they learning, right? Are they learning the safety things that matter? Um, the electrical, the mechanical, how to hoist and rig and things like that. That’s all part of it. Um, and that all leads to getting the all important competency verifications, the sign offs. What we say here is all roads lead to competency verifications, or JPMs. We call them job performance measures, right? They have to be able to understand hazards. Well, first understand the paperwork, the job safety plan, and the lockout tagout paperwork. How to call the operation center and shut down the turbine. Then they have to be able to recognize the hazards in the task and do it with high quality. And they’ll go perform the task, and then roll it back out, take off their lotto, fill out their paperwork, and they get signed off by, by what we call journey workers, or the more senior level people who are already signed off, or a technical instructor. It depends on the situation, really, right? So, so really the key to the kingdom in training is not the training itself. It’s the end result that they are competent to perform the task safely and with high quality, and that’s where our program’s going. I Joel Saxum: think it’s important that you just mentioned it is well, uh, on your repowers. You’re focusing on your repowers because there’s that nuance in the IRA bill of you must have an approved apprenticeship, a program, and you guys have to have that in place for PTC credits to roll for on those repowers of people working them. So the, that’s a huge part of that. And, um, I’m really liking, like, like that part of it. Russ Leach: Yeah. That’s a major forcing function in the industry. I will say that, um, the industry is moving towards, or the U S I should say, is moving towards apprentice programs slowly anyway, from 2011 to 2021, the number of apprentices went about 60%. But it’s still a small number compared to our, our, our, um, colleagues in, in Germany, right? They are, where they’re 1. 9 percent of their population is in registered apprentice programs. Here it’s 0. 18, right? So it’s really small. Yeah. But the IRA Act is a major forcing function around apprenticeship. If you have four more people in your company and you’re doing work that applies to the Inflation Reduction Act, for that owner to get the tax credits, they have to employ a Registered apprentices. 15 percent of the labor hours have to be from registered apprentices. Joel Saxum: Yeah, so let me, let me ask you a question about this one. So, at the end of the day, when we’re talking training, when we’re talking all these things, It’s a function of recruiting and resourcing for people to do the jobs. One of the problems that, and I know this is a global thing, but really exacerbated in the States is, um, basically retention of technicians because you may get them in and get them trained up and get them working on your processes. And then because there’s such high demand, it’s like, Oh, I’ll get, these guys will give me another dollar an hour. I’m over here. I’m over here. I have to imagine that the training programs and what you guys are putting in place to really build these, these technicians up in their career has to have a positive effect on retention rates. Are you seeing that too? Russ Leach: Yeah, it absolutely helps. Yeah. And of course the, uh, and you’re right, they’ll leave for a dollar an hour somewhere, but it’s a combination of culture and what’s in it for them and their future. Right. So we try to wrap them in a, in a really respectful culture that, In a growing company that people are having fun, but at the same time, especially with the apprentice program, give them a goal. Give them a goal. They want to stick around because they’re going to get this, this really valuable certificate that’s valuable for their career. Um, and if not a certificate, just a lot of training, right? Um, for instance, January, we’re, we’re, we’re standing up a two week intense, very intense intermediate troubleshooting course. What do we, what do we find out this last year? Lesson learned from us. We had a one week troubleshooting course that we set up, but 60 percent of the technicians who ran through it didn’t pass because we got them from other companies because we’re growing quickly, right? So we, we hire a lot of people from other companies and we put them into this, uh, senior techs into this, this troubleshooting course. And, and 60, like I said, 60 percent of them didn’t pass because they had not had training, detailed training around schematics and how to, and how components function and things like that. So. Lesson learned, right? Lesson learned. So what we did was, now we’re blowing that out to two weeks, two intense weeks where we’re focused on fundamentals, and then they get into the troubleshooting. But here’s the thing, here’s the really unique thing about it, they also teach, they’re taught how to teach back, they have to do teach backs. Um, you know, the, the, in this business, the team leader over the technicians, is almighty, right? They, they dictate everything that happens to them, right? So if they’re good instructors, if they’re trained to teach, if they’re trained to pass down that knowledge around, um, schematics, around how components work, around whatever, right? It’s just going to make the, these technicians, their experience just that much better and they’re more likely to stay around because somebody’s paying attention to them. So, to keep people, you have to give them a good culture. You have to pay them attention. You have to tell them what’s in it for them. And they have to see the value in that. And that’s one thing. That’s why we’re investing so much. I’m, you know, pinch me, right? Momi has all these nacelles, these beautiful nacelles in his facility. Guess what? We just signed an agreement. We’re getting a seamless 2. 3 megawatt nacelle this first or second quarter into our training center. As well as a Mitsubishi simulator. We have a lot of Mitsubishi 1000s. Great little machine if you, if you operate it right and maintain it right. We’re sort of taking the guts out of that and we’re putting that in there as well. And then after that it’ll be probably a GE15, I think, 1X of some kind in there. Just to get really hands on experience in our center. Similar to what Maume is doing there. Couple that with the apprentice program and you’ve got a winning combination that the Germans have proven over time. Right? Um, a good center, good apprentice program, on the job learning. And you wrap all that together and you get really good text out of it. Allen Hall: Moment. I want to talk about the type of people that are attracted to your training program in Germany, and I’m going to come back and ask Russ the same thing, but who are those people that are attracted to being wind turbine technicians today? Momme Feddersen: You have to learn, love to work with your hands. You have to work on your own. It’s a real tough job. I think you all know that. I think you, you need the experience in your job. I doubt that you are the person who, uh, That a person who always wants to go to the same shop, do the same thing is the real, um, uh, turbine technician. You have to be excited about everything. You have to be excited about the height. You have to be excited about, uh, small rooms. Um, I think, and you have to be really passionate about what you’re doing. And you, I think that’s the, the type of person. Um, who work in that and in our company and, uh, work in the bread. Allen Hall: Do they come to you straight out of school or are a lot of them coming from other industries and deciding to getting to win, to get a little more venture, maybe get out of the office? Momme Feddersen: All kinds. Um, so the apprentices all come, mostly come from school. The career changer already has a, has a different job, but we also have The ones who comes from other companies like Vestas, like Anaconda, or something like that. So we are, we are hiring about, just here in Germany, we are hiring about 150 people a year, just in the field. So we are growing quite fast. Allen Hall: And Russ, what does that look like in the United States? I think that the demographic for Future wind turbine technicians is a little bit different. What are you seeing in the U. S.? Russ Leach: A lot of entry level people or people who have tried other jobs and it just wasn’t fulfilling for them. We get a lot of folks who’ve, uh, just a few I’ve talked to recently worked at an auto store, like an, um, well, auto parts store, for instance. I’ve got others who come from the prisons, lots from the military, which we love. Um, and it’s really all across the board, but they all have some things in common is that they don’t want that office job. They see it as a challenge. They’re very proud of what they do. They’re all smart. They’re really smart. And, uh, they just want to do something that’s different than everybody else. And climbing wind turbines is as different as you can get. Joel Saxum: We see that as like an adventurist spirit sometimes, like a lot of, a lot of the, uh, the blade people we know, like when they’re done with the blade season, they go rock climbing and they’re free soloing in the Tetons and all kinds of crazy stuff. And it’s like, man, you guys are really nice. Um, but that makes that the right person to be. I mean, when you look at like, say again, like blade repair techs, they’re hanging from ropes, like, you know, hundreds of feet off the air. Like that takes a certain person that wants to do that. Or when you walk into the base of a turbine and you look up that ladder, there’s a specific person that is cool, that wants to climb 80, 100 meters every morning. Russ Leach: Well, they’re mentally and physically tough, right? If you’re climbing a turbine in South Texas or Oklahoma in August, you know, you’re not weak mentally or physically. And I have so much respect for the men and women who do that every day. Momme Feddersen: And what I really like is Our technicians are really proud to be that. Um, when you, when you have a look at our, for example, Instagram channel, you always see pictures from, from our technicians who are on a turbine. You see how proud they are, what they are doing, how thrilled they are about what they are doing. It’s, it’s, it’s so cool. Allen Hall: And what does that look like if you want to join Deutsche Windtechnik and you, and you want to be part of this apprenticeship program or, or try to advance your career or get out of the auto parts store or get out, you’re coming out of the military, what are they looking forward to? What is the next six months, year look like for them? Russ Leach: We start out with a one week of onboarding, which is just intense safety stuff, Allen Hall: right? Uh, Russ Leach: uh, individual, you know, competent climber, rescue training, the things you’re familiar with. We also throw in a high dose of, uh. Hydraulic tooling, because there’s a lot of fingers, fingers have been lost over time with hydraulic tooling. First day CPR, OSHA 10, things like that. NFPA 70 is a big one. Electrical safety, of course. Um, and, and of course, just the company policies. That’s, that’s the first week. And then they get assigned a whole bunch of training, and they go out. People learn better on, for wind turbines or anything, if they’ve been exposed to it already. So to get out there, working under the PAE, Primary Authorized Employee, from an OSHA standpoint, the person who’s there to make sure everybody’s working safely, also known as a team leader in many ways, working under them, um, and start getting sign offs on competency verifications on the, on the basic things. This is how you start a turbine, right? This is how you connect a bucket, for instance, just to keep things simple. Um, and they, they start going through that, and then, then when they’re ready, then we, we start cycling through more, more formal training. That we do now, and especially as we build out our center more, there’ll be more of it. That two weeks of training, for instance, um, that we talked about for troubleshooting and then, and it’s just a lot of experience on the job learning sprinkled with, of course, the regulatory online stuff that everybody has to do from an OSHA standpoint, um, and other training. And it takes time. It takes time to cook a good wind technician. It really does. Allen Hall: Deutsche Windtechnik has been involved in e learning, online learning at the same time, because you have people deployed. all over the place that need to keep up to date on the technology, on the training, on those certifications. You want to talk about what that looks like once you get into the Deutsche Windtechnik system? Momme Feddersen: Um, we are starting to do that because, um, we want to reduce our, uh, time in the training center with where you just learn theoretical stuff. We want to reduce the travel time. To, to training center. We want touse our, so, um, and, uh, that’s why we developed some online trainings. But, but especially the in instructions, what we have to do and especially the safety instruction where you, what you have to do on a regular basis. Um, but uh, as I said, right now we are focusing on the older turbines, but in the future we have to be. Um, prepared for the newer ones, and that’s why we, um, uh, develop kind of 360 degree, uh, videos of turbines, what we can use in our training facilities. Um, we have different things here in the training center where we can, what we use. Um, yeah, but also, uh, virtual reality is also a topic, what we are developing right now, where you can use your hands, do something without having the turbine in place, without having the tools in place. Uh, so that will, that will be a part of the future, definitely. Russ Leach: Yeah, we, we made a lot of custom, uh, e learning, uh, using our own internal developers and outside developers. There’s a lot of value around custom e learning. What we found is that technicians don’t like e learning that doesn’t specifically apply to what they’re doing every day. They don’t like it. They don’t want to waste their time on it. But you get one that’s specific to that, say, CEMAS that they’re going to work on every day, now they have a lot more interest, right? But like Mome says, we’re moving into this new realm. For us, in first quarter, we’re making one for, well, two of them, probably a Mitsubishi and a GE, this 360 degree type training where, You got these special cameras that you go film the whole turbine. And you, you load it in your software and you can look any direction like a 3d thing. But the main thing is you can, um, click on a cabinet. Well, it’ll cabinet opens, click on a component, zooms in on that. You got links to, um, hazards or work instructions that, that goes with it. And the cool thing about that is you can now tie it in with your engineering support and your technical support, where they can say, Hey, go check this component out, let’s take a look. And they open up the software and they zoom in on that contactor. You know, check the DIN rail behind this contactor. Let me show you which one it is. You know, especially if you have somebody who’s just learning troubleshooting. Um, or the site manager who might be really, really experienced in the turbine, you know, looking on their phone. Here, go check here. So we’re trying to leverage that to increase the, uh, to amplify the effectiveness of our technical teams to get the turbines up quicker. So we’re super excited about that. That’s rolling out this next year for us. Germany’s already using it. Allen Hall: That’s remarkable. Uh, to be a wind technician now is the right time doing it. 10 years ago, it just seems like it, it is a hundred years ago because the technology has got so much better and the training is light years, uh, away from where we were just a couple of years ago. And the investment by a number of operators and Deutsche Wind technique being the forefront of this is tremendous. Uh, so if you are interested in being a wind technician. You better get in line right now because there’s going to be a line at Deutsche Windtechnik store because of the training and the skill set you’re going to get from a high quality company. Now, Mami, how do people get a hold of Deutsche Windtechnik? How do they get into your system over in Germany? Momme Feddersen: The regular way. Uh, apply online. Uh, we got an awesome recruitment department. Um, so when you apply, I think a week later you have a, uh, an appointment with our recruiter. So nice people. Um, yeah, so it’s, we are extremely fast. Um, that is outstanding. I think here, I worked at different companies before and it took. Month to, to, to hire new people because the, the recruitment departments were slow and, uh, the, yeah, it should be honest. And I think this is really different here, um, to be fast, to be able to find the right people, to talk to people, um, to, and yeah. And for example, here at the training center, we, Always have people, um, who come, who come here to, to, to see what we are doing and, uh, to be able to see something, what, uh, when technicians do, um, even if they don’t work here, they, they see the training center. They see how serious. We, we do our things and, um, that’s why they are really interested in, in working for Deutsche Windtechnik. Allen Hall: And Russ, how does that happen in the, in the United States? How do they get a hold of Deutsche Windtechnik and get into the training program? Russ Leach: Very similar. The best way is to go on our website and our jobs listed and apply. That gets you into the system. We have some wonderful recruiters as well who are, uh, who are right on it. Talk to them, and it starts a sequence of interviews, Allen Hall: right? Russ Leach: And, uh, and once they, you know, everybody agrees to, that they’ll come on, then we schedule a date for them to come on. We have an onboarding every month, sometimes two onboardings a month in the summertime, kind of our peak hiring season. We’ve had up to 20 people in these. We average around 10 ish, uh, a month, uh, coming on. And, uh, they, you know, they come on. That starts their journey with us, uh, depending on where they’re going to go. We have our traveler teams, about 80 or 90 of those who travel everywhere. That’s right. We have our O& M teams or fixed sites. We got our new repower team that, that, that we’re building right now and is already operational, um, that can go there. Um, they’ll hire on for one of those teams. And then, um, of course, leadership development is a big deal, right? We have our leadership development program and the best and brightest can go in there and start moving into lead positions, manager positions, and things like that. We always prefer to hire from within our leadership because they know the company and they earned it, right? So they also have a chance to get into our LDP as well over time. Allen Hall: That’s really, that’s really impressive. So if you’re out there and you’re thinking about getting into wind and being a technician, and there’s a lot of opportunities right now. Think about Deutsche Wind Technique and you need to go visit their website, which is www. deutschewindtechnique. com. Uh, you just Google it and it’ll take you right there. And Momme and Russ, this is great. Thank you for being on the podcast. Well, we really appreciate you having us on and we look forward to Russ Leach: doing it again. Maybe we’ll have one on quality someday.…
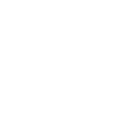
1 Wind Energy O&M Australia’s Success in Melbourne 36:41
36:41
التشغيل لاحقا
التشغيل لاحقا
قوائم
إعجاب
احب36:41
For the first time ever, all the Uptime hosts are in the same place! They discuss the fantastic outcome of the Wind Energy O&M Australia conference last week, highlighting the amazing presentations, attendees, and discussions. Keep an eye out for next year’s event ! Fill out our Uptime listener survey and enter to win an Uptime mug! Sign up now for Uptime Tech News , our weekly email update on all things wind technology. This episode is sponsored by Weather Guard Lightning Tech . Learn more about Weather Guard’s StrikeTape Wind Turbine LPS retrofit. Follow the show on Facebook , YouTube , Twitter , Linkedin and visit Weather Guard on the web . And subscribe to Rosemary Barnes’ YouTube channel here . Have a question we can answer on the show? Email us! You’re listening to the Uptime Wind Energy Podcast, brought to you by BuildTurbines. com. Learn, train, and be a part of the clean energy revolution. Visit BuildTurbines. com today. Now here’s your hosts, Allen Hall, Joel Saxum, Phil Totaro, and Rosemary Barnes. Allen Hall: For the first time ever, I think all four of us on the podcast are in The same location at the same time. Rosemary Barnes: If you include our amazing producer. So Allen Hall: this is a unique time and we just finished wind energy, O& M Australia. which was completely packed, insanely full, and it was a day and a half of informative discussions, no sales talks per Rosemary’s strict instructions. Good call. To get the information out to the industry and let everybody know what’s happening around the world? Is it, Australia is a really unique place, Rosemary. There’s a lot going on here. Rosemary Barnes: Yeah, I think so. And the wind market is definitely unique. We’ve got a few unique problems. We also, a little bit different to other markets I’ve worked in, like in in Europe and in North America, where there are a lot of engineers around who’ve worked on the design and manufacturing side. We don’t have those industries in Australia. And there aren’t as many people filtering through with that deep technical knowledge. So it’s taken us a bit longer to get to the point where one, people realize that they need to have that information. It’s not enough to just have, a service agreement and trust that they know what they’re doing and that they’re acting in your best interest at every moment. And two, for people to begin to, yeah, get that expertise. There was no shortage of, Expertise on the panels. And yeah, my favorite thing about the conference was hearing just conversations going on, just, overhearing people just geeking out over some, really niche topic that they hadn’t thought of that they’d heard, someone mentioned on stage, a couple of people connected who didn’t know each other, and now they know that they’re got the same problem or one of them’s got a solution and one of them’s got a problem. It’s yeah, just exactly what I wanted from the conference. Joel Saxum: I think one of the things I took is this joke was told a few times, literally and figuratively on an island here in Australia when it comes to wind energy knowledge, right? So we tried to, when we put this conference together, we tried bringing some expertise from around the world. Simply because, it’s hard to travel down here, right? That’s just a simple fact. It’s geographically remote. So bringing that expertise in here and And after we went through a bunch of things on stage, a lot of people talking on the sides like, I didn’t know this solution existed. Like the Soren Kellenberger stuff from CNC Onsite. I didn’t know you could precision machine things up tower. That was just like, to a lot of people that, that exists, right? Lightning protection upgrades do exist. There’s people that can do it. There’s things you can sense. Shadow monitoring of your fleet. Even when you have an an FSA with an OEM. Oh, this is a great concept. These are things that like in the States. In Europe, we’ve been doing for quite a long time and these things are there, but it’s just not down here because it’s a smaller market as well. Rosemary Barnes: Yeah. It’s also hard for Australian Australians that are working in the industry, can’t all get over to those international conferences. And to be honest, they’re not always great either. They’re, often very sales pitchy and yeah, cover the same topics over and over again, the kind of more lowest common denominator stuff, rather than that really technical. Geeky stuff that sometimes you just need . Phil Totaro: So I was fortunate enough to moderate the operator panel where it’s funny because we all joked before the event that might be one of the more contentious things that would come out of this is, the challenges that are being faced by owners and operators with these full wrap service contracts. But I was struck by the remarkable amount of, maybe they were biting their tongue a little, but the remarkable amount of collaboration that they were talking about and espousing and saying, we, we want to be able to, we’re a small market and we need to be able to depend and rely on each other. And so we can’t burn bridges and we can’t, do things to, to disrupt the the OEM relationship. Even if we choose to, eventually rely on an independent service provider. So that was very that was very interesting. And it was a very free flowing dialogue. Not only in that session, but throughout the whole day and a half. People actually opened up. Which is one of the things we wanted with developing the program. Was we wanted people to start talking. And they did Joel Saxum: sometimes when you do a panel and you say, Hey, can we get some questions from the audience? And you have to like pry one out. Oh, I know Alan, you and I, when we’re at conferences, it’s usually you and I, Hey, I got a question. We had no shortage of that at every single panel. We were running around with mics. Here’s a question. We got a question over here. We’ve got a comment over here. And I think the spirit of that culture, Went through the whole event up until the second day when we’re doing roundtables. Joel Saxum: You were, I was in the back of a few of them guiding some things. You were bouncing through, man, there’s conversations going on over here. Yeah. I know I was Joel Saxum: in one I had there was like 30 people in there and nearly half of them had different questions during the roundtables. So the audience here the wind industry here in Australia, it’s hungry for knowledge. Phil Totaro: Absolutely. And actually that’s one thing that I didn’t get a chance to say at the end was, We’re all here for you, not only the four of us, but the companies organizing the event, anybody that came from the States we came or anywhere else around the world, for that matter, we came because we are interested in helping the Australian market grow. The whole thing with us doing events is we’re not event planners, as Rosie said at the end of the session, but. We don’t measure success based on, how many pictures we get taken shaking hands with a politician. We measure success based on how many megawatts go in the ground and how efficiently you’re able to operate them. So whether you need Rosy’s, technical expertise, whether you need lightning upgrades, whether you need, CMS and sensor technology from eLogic’s Ping, or, any kind of strategy consulting or benchmarking that we can provide at Intel Store. Ask us. Please rely on us. We’re here to help you, and we want to help you, and I will bear the 15 and a half hour flight to come all the way back down here very gladly. One thing Joel Saxum: we should touch on there too, as we said, the four of us here, Matthew Stead and Thomas Schlegel from Eologics Ping. They’re not in this room right now, but they were key components of putting this thing together. Of course, Ping is a Australian born company. So the local connections here and all the way down to where we should go eat. That was fantastic, but much, much more than that. We wish those guys could be sitting here with us, but everybody’s got to travel. Allen Hall: Melbourne has been a great city. I’ve been pleasantly surprised. I thought it was gonna be really too hot, according to Rosemary. I Rosemary Barnes: think it’s gonna be 37 today, so you may still Allen Hall: get that wish. We did enjoy walking along the river. The restaurants are fantastic. There’s just a buzz to the city, which you don’t necessarily see the United States at the minute. So everywhere we walk, even this morning, there’s just people. Happily walking down the street and going to their offices and having coffee. And it’s, it is a lively city, which is enjoyable. You don’t always see that wherever you travel. So that was quite nice. And the, the piece I pulled out of yesterday was the expertise that Australia has developed, and I thought a lot of the things that Operational side should be coming over to the United States, actually, particularly on noise. I thought the session on noise was really informative about how the operators deal with noise and how they try to address it and how they deal with the neighbors. We don’t have that. And we just don’t do that. No. At all. In the States. Rarely. And it is a huge stumbling block. Yeah. But some of the approaches that Tilt and some of the other companies that were represented were surprisingly good. Thought out and were planned ahead. They weren’t just trying to be reactionary. They were proactive about noise. Rosemary Barnes: I think it’s cause I think Australia got hit turbine syndrome thing. And Yeah. Yeah. I know that you had problems with people thinking wind turbines made you sick in the United States. Maybe it was as bad as here, but it was pretty shocking here. Like even while I was doing my PhD, like just just sitting in an office by myself running finite element analysis models and publishing in academic papers, I was getting people emailing me about how, evil I was and how much damage I was doing to the world because I was captured by big wind and, you Making everyone sick. And like I know I was really shocked cause when I first heard about that, I was like that’s not a real thing, so I’m not going to worry about it. And I think the industry thought that, and then we realized, oh, okay, we can’t actually put new projects in because everybody thinks this. So thinking it’s a problem means it is a problem. And yeah, if you go to the more mainstream wind energy conferences in Australia, The word social license is mentioned at least once in every session, no matter what the topics are. I think that it’s just like super duper front of mind for developers here and yeah, and operators. Allen Hall: And supply chain also. Because you’re on an island and nothing is really manufactured in country. It always comes from somewhere else. The planning involved in supply chain was surprisingly aggressive and good. They’re thinking ahead, way ahead. In America, if something breaks, they just think I’ll just order it from China and maybe it’ll come soon. We have the Amazon syndrome there. Totally do. on Joel Saxum: Amazon. Allen Hall: And it doesn’t always arrive like you think it’s supposed to. And the term is down for much longer. In Australia, they don’t tend to do that. They tend to be much more ready for those situations, which is, I think, good. Beneficial to them. You want those turbines to be running all the time. Joel Saxum: Yeah. The one slide that someone popped up and I don’t remember exactly which assessment it was in. And there was, I think, Phil and you and I talked about it. It was like, these are the installed turbines in Australia. And it was like, there’s 13 of these and there’s eight of those. And there’s 11 of these and there’s, I think Rosemary Barnes: it was Katrina Joel Saxum: Swallow from Wind Lab. There’s 22 of these and there’s 46 of these. It was like, man, to find parts for that, to get them down here for those specific turbines, like that’s going to be tough. Tough as they start to age. So I think that was actually a really good session we had was the lifetime extensions session that the people were when you turn around and you look in the crowd and I did this quite regularly during the whole event was just to see how many, when slides are up, how many people had their phones up, trying to take a picture of a slide or how people paying attention stuff. And it was all eyes forward. Everybody, You didn’t see a lot of people sitting back like, yeah, I’m at a conference because I have to be here because I’m typing away on my computer. People were engaged. It was good content. Phil Totaro: And one other thing with that panel that Rosie moderated, the Life Extension panel, was You know, when my biggest question coming down here and having studied this market for a while was they’ve got a lot of assets that underperform because the market is so highly dependent on wholesale market. For their power sales and those prices fluctuate wildly, day to day and even year on year. But the proactive thinking about wanting or frankly even needing to to life extend and how much benefit is that buying you. That was something that I still feel like we didn’t quite fully address it. So hopefully that’s a topic that we continue to talk about next year. But also it was interesting the foresight that you know, Katrina, who represents WIDLAB and Christian Peek, who was also on that panel from Mint Renewables the, they were the two the two owner operators there. They. had some very good insight on, what’s going to be necessary in terms of both market conditions and technical requirements to be able to do any kind of life extension. And it was it’s obviously fundamentally different than the kind of market we have in the United States where it’s subsidy driven, repowering after 10 or 11 years. This requires, just like you were talking about with logistics and everything, Joel, it’s, this requires a lot more forethought to, all right if we get to, 20 years of life and we haven’t necessarily fully paid back the capital that got spent on this project, what do we do? Because we have to life extend, we can’t be underwater on a project. What do we do to ensure that we get the kind of operational life out of this thing while maintaining the performance level? And Joel Saxum: the flow of the sessions worked out well for that conversation is at the same time because we had a complete session on just CMS and CMS for, yes, we can solve problems with it, like the noise mitigation thing. But also CMS for understanding the health of the assets before we get to that stage of lifetime extension. And then you roll that in with having some of these MCE providers at Gearbox, people with the ZF and the Schefflers up there. Hey, if we’re going to be doing this, let’s all work together. We can get kit here. We’ll have it in country stationed and ready to go. There was quite a few of those collaborative conversations and that’s something we even say in the U S all the time, transparency and collaboration. Everybody’s saying to the operators, to the OEMs, involving the ISPs, involving the supply chain and the, those conversations were flowing with the gates wide open during the day and a half. I was impressed with that. Phil Totaro: Yeah. And the one thing about that too, is that the more, and I talked to three or four different people, both, folks that came from other countries, including the U S down here or Australians about this. And the consensus was that, Hey, we recognize the fact that if we are more transparent. It’s going to attract more foreign direct investment into this market. And that’s something that not everybody in the world kind of understands. So again, good foresight on their part to recognize the fact that, they, the whole reason we’re able to do all of the analysis we do on profitability of assets, et cetera, et cetera, is because they take the five minute Skated data and put it online so that the entire public can get access to it, which is nuts. Try getting that in Germany or, anywhere else in Europe or, we barely have that in the United States, but we get it published after, nine months later. We’re gonna wait until September of 2025 to get data on what happened in 2024. to every single wind farm in the US. It’s preposterous. So the fact that they have, the five minute average data available like that for every project, every type of renewable to solar battery storage, you name it it’s all out there and it’s public and they’re transparent about it, which gives you the ability to analyze it, to see where things are working well and where it’s not and focus investment to, to help improve it. But that’s the thing about Australia, Allen Hall: which is a little bit different than any other country in the world at the minute, is that they have a large renewable grid and they’re able to do it every time in the States. And Rosemary knows that when we get criticized in the States, it’s renewables are never going to have a place. And I just say Australia. Yeah, we have Rosemary Barnes: the same conversation here. It’s power prices spiked because a coal power plant blew up in the hate and two other coal mines are flooded. It’s renewables. Renewables can’t, they’re not reliable. Look how high our prices are. It doesn’t matter what happens. There’s a storm that blows out of our power line. Oh, wind power to blame again. It’s it’s a political conversation, Joel Saxum: not a technical one. Yeah. Yeah. The, Rosemary Barnes: It happens, I think. But what I think is a little bit unique, or it’s not unique, but like rare in Australia, is that it’s not it is really primarily not governments pushing for this to happen. Coal power plants have announced their closure date based on economics projects are going in based on the economics of it. And yeah, there are some struggles at the moment. There’s a lot of negative power prices. A lot of, a lot more curtailment than people would like, but we’ve also got. So many batteries that are online. I was just trying to Google to find but the pipeline of projects under construction is gigawatts. And I think I saw that it was like four or 500 megawatts in the last quarter connected. So I think even within the next 12 months. that you’re going to start to see batteries make a huge difference and like slice out like a huge amount of the high evening prices where gas peakers come on and, demand a lot of money for doing that. I think you’re going to see like in regular days where, you got really sunny middle of the day and batteries can charge, which is nearly every day in Australia, let’s be honest. You’re going to see the, yeah, pricing environment completely change. I’m not a. Financial analyst or energy market modeler, so I’m not going to try and guess what the impact is going to be, but yeah, you like, look at the number of gigawatts of batteries we’re going to have compared to the number of gigawatts of gas in the evening, and it’s very similar. There’s not like much of a difference. And so intuitively, that’s going to make a difference. And Yeah projects that are struggling now I do hope that they are going to struggle a bit less. We’ll get a lot further with renewables before before we start to see the same sort of pricing thing happen again. Allen Hall: Yeah, that’s actually a good question because Australia is leading in so many different areas. Solar for one battery two now. Does that battery addition make profitability and wind go up? Because there’s just evening out the grid and you’re not going to, the curtailment basically stops. Is that the magic ingredient that a lot of countries are not really invested in at the moment to make the solar, wind grid work? Rosemary Barnes: Yeah, I think so. And I think it has the most obvious effect on solar because solar is all, it all comes on at the same time in the middle of the day when price is negative. It would be, horrible to be trying to make a profit off a, Utility scale solar farm that was just, exposed to market prices and nothing else. But yeah, no, I think it is a solution, but I think also you need to have the problem before anyone will invest in the solution. So I think like Australia has really high volatility and it’s electricity prices and you need that to attract people to want to buy. A battery and install it. Joel Saxum: We’re seeing that same thing. I would say the closest market to here in the states would be Ercot in Texas. Yeah. And you’re seeing how many you and I driving around there, how many battery installations are going in and talking with some of the ISPs out there and the construction companies, EPCs, they’re just like Word. We’re building batteries, we’re servicing batteries, we’re signing contracts. So battery, that’s going to be the key to the renewable mix as we go forward. Rosemary Barnes: But it’s another, it is really similar and I think actually the same people were involved in designing the electricity market in, I can’t remember who got inspired by who, but Australia and Texas’s. Energy only markets are very similar in design, and I understand that it’s not a coincidence. But, it’s not like the Texan government. It’s yay renewables, let’s do whatever it takes, right? That’s happening because the, conditions are right there for it to make money for developers, and so they put it in. It’s similar here. Joel Saxum: I could say something that’s a little bit controversial, but one time I was told that Australia is basically British Texas. Here we go. Here we go. Phil Totaro: Now, there’s one other comment on this concept, though, of energy storage solving the problem. Theoretically, yes, but keep in mind two things. One, as Rosie just said, how much Price volatility and how much dependence there is. So for wind energy projects in Australia, I think about 94 percent of the power offtake is done through a wholesale market. Like a, merchant, what we call a merchant market. With very few projects actually having a fixed price or some kind of firm power offtake. With, a utility company or, some kind of government entity or what have you. That’s very different than in the United States where it’s 80 percent of our projects have some kind of utility fixed price off take contract etc. The second thing is, Storage can solve a problem like curtailment and negative pricing in Australia because of the transmission and grid constraints as well. So if they were to build more transmission, then you don’t need as much storage. But the question then becomes is a battery cheaper and faster to implement than it would be to build additional transmission? Allen Hall: Yes. Phil Totaro: The answer to that is yes. Yes. Absolutely. Yeah. And we Rosemary Barnes: did see in one case, Broken Hill, which is a it’s connected to the main grid, but it’s quite far away. It’s very far inland and away from most of the grid. They have transmission connection, but it’s not enough. So they considered, do we want to upgrade that or, assumed that they would need to upgrade it, but then did, ran the numbers and found that energy storage would be the cheaper way to get that same reliability. I think they actually went with compressed air energy storage for a big part of that. So we’ll see how that goes. And I also have to caveat with yeah, recently they had a very lengthy period of blackouts or brownouts yeah in the town because, yeah, so it’s not totally smooth sailing, but they, at least the concept is there. And I think that household batteries is going to be a big thing too, cause we have Like at the moment in Australia, rooftop solar, if you add it all up, that’s the biggest generator in Australia by quite a lot, but there’s not many batteries and yeah it’s a really challenging for the grid because it’s not controllable, like it’s just yeah, it just goes in, we’re starting now to come up with some mechanisms to be able to control it, super duper unpopular. You can imagine, you’ve spent 10, 20 grand putting solar panels on your roof, you don’t want to be told you can’t use it. But I think that yeah, home batteries, even though I know I’ve been told over and over again by very smart engineers who have very good models, it’s not the cheapest way to get storage in the system, but I think we’ll see it anyway because it means that individual households can make that decision on their own and use their own power later in the evening or whatever. And I think that’s going to be a big thing in Australia in a couple of years time. That’s my unpopular prediction. Joel Saxum: Democratizing power generation. Rosemary Barnes: Yeah. Yeah. And it’s yeah, I don’t probably necessarily disagree with your British Texas thing. Maybe the British part, I don’t like that bit so much, but Australians do to not have to rely on the utilities. Like people, Australians do not like utilities in, in general. They don’t like the government telling us what to do with stuff that we’ve bought. I’m putting our Phil Totaro: own house, like how very right wing of you. Joel Saxum: Interesting. Let me shift gears a little bit to the, in within the context of our conference here that we put on. There’s a difference between of course, how the market operates down here and how say we operate in the U S versus with ISPs, OEMs, full service agreements. However, Down here I was. ’cause I wanna see what each of you heard and what your opinions are on the ISP involvement in the market for operations and maintenance. So to, we saw RES, we had a conversation with RES, of course RES, huge ISP around the world. Rig comm was here, rig comm, of course. The sponsored the coffee carts. Fantastic team. They were up there on some panels as well. They’re a part of a larger blade group, GEV, that’s operates all over the world as well. So they’re bringing that expertise down here at, from a local standpoint. Rosemary Barnes: Worley. Joel Saxum: Worley. Of course, Worley. Dr. Larry’s presentation on some leading edge erosion stuff. Fantastic. So there is some ISPs down here. I don’t see the market fully saturated, right? Cause it’s just, there isn’t the want or the drive for it. The market’s not big enough. But you started to see a lot of the ISPs that I saw here were really happy about this conference. They were happy about the conversations we were having and saw the opportunity. My question, Alan, what did you hear and see from the ISP world as far as operations and maintenance opportunities here? Allen Hall: Everybody’s trying to break into Australia. They’re still trying to find a foothold. There’s a lot of ISPs outside of Australia that have been looking at Australia for quite a while. Four or five years, roughly, and are trying to find that time to make the transition over. With the amount of growth that Phil pointed out that’s going to happen over the next ten years, you better get into Australia relatively soon if you want to be part of that growth. It is such a dynamic market. It’s insanely changing from what I could tell. And just listen to the people talk. One of the key things I picked up was they, the engineers working for ISPs or operators, know what they’re doing. We talked to a lot of operators around the world and sometimes it’s wow, they really are struggling. Not here. There’s a game plan. There is a process. There’s a reason why they’re doing what they’re doing to get return on investment or try to create more power to level out the grid. It is all planned, which is amazing. And when one of the beneficial things I pulled out of it was like, wow, it’s a lot of resources and maybe we need to bring some of these people over to Europe and then we get them into America and start talking to some of the operators over there, because There is a lot of knowledge here, and that marketplace is going to explode. Now, one of the things that happened at the end of the discussion yesterday was we were all gathered around figuring, Are we going to do this next year? Was there enough response back that we would see people wanting to do it again? Was it a high enough quality conference? Did they learn enough that they would want to do it again? Overwhelmingly, yes. Everybody was like, you got to do this again. When can we schedule it? Can we get on the books? Can I sponsor? Whoa, okay, we just finished this. We’ve been working pretty hard, not necessarily me, but everybody else on the team has been working really hard on it. And yeah, it’s just whoa, okay, great. So we, I think we did fill a little bit of a void and that is important. I think that’s one of the things about the podcast and Rosemary, you’ve been on it with me the longest. Rosemary Barnes: Yeah, out of the current crew. Allen Hall: Yeah. Yeah. How many years has it been? We’re almost about five years, by the way. Rosemary Barnes: The podcast as a whole. Yeah. Every now and then I I’m like researching a topic and I I, a 20, 20, 20 episode of Uptime Podcast comes up and I go back and listen to it. You and Dan. Jokes about Godzilla and stuff like that. That’s what it was like when I started, it was really fun. Yeah, but it has been fun to see it evolve and have, having more people is good. Obviously it gets hard to find the time every single week to, to get together. So yeah, it’s nice to be able to tap out, but yeah, Yeah. I think we agreed that we will, we might change things up a bit because this year we really wanted it to be not for profit because that’s one of the ways that we could get people. It’s hard on your first event to get people to trust that it’s going to be good. And I was like, really I don’t know, I felt really I’m trying to think of a word that doesn’t sound like really over the top, but I’m thinking like blast. I don’t use that word, something like that, but turn it down a bit. I was pleased that people trusted us to, people came from overseas, people, took time off work and came to this little conference that has never been put on before by people have never put an event on before. I think all of us heard like probably dozens of times. That’s better than I thought. That was like the Rosemary Barnes: number one comment for the first day at lunchtime was off. Wow. Yeah, no, this is better than I thought. And then a lot of people have told me, I haven’t been to a conference that had so many topics that I really needed to know about in so long. So we’ll do it again. I think none of us can manage the organization effort again. So we’ll probably partner with a event. organization next time, which will necessarily remove the not for profit part of it, because they’re going to want to make a profit, but it’s definitely still keep the thrust of it, use the money to get good people in. I think that’s a big difference with our conference and others is like really focus on getting the right people speaking, not the person that has the most money, definitely still not doing pay to present. That’s not a thing that you’ll ever see at this event. I don’t think, Oh yeah, not while I’m working on it anyways. So yeah, put together a really good program and we’ll still manage the agenda and the speakers and definitely people listening get in touch if you’ve got a good speaker. Cause yeah, it was we won’t be able to come up with another program based on people we just know next year. So we’re going to need help. Joel Saxum: Yeah. I think that’s a good point here is to touch on some of the speakers that we had. Rosemary Barnes: Yeah. Joel Saxum: We had a couple come from, we had Jeremy Hanks from CIC NDT bringing that NDT experts, expertise over here from the States. Our friend of the show, John Zalar, he’s been on the podcast a few times. 22 years in GE, right? So he’s bringing a lot of information over. He came over and got onto a few panels. We had operators here from, of course, Tilt. We’re in Tilt’s office recording right now. Thank you, Tilt. Yeah, thank you, Tilt. Baron was fantastic. We had some of the team from Sky Specs here talking about CMS, right? How you can shadow monitor some of these assets to Make sure your OEM FSA is getting fulfilled the way you want to. We talked about some brand new technologies that, say, the Rowan’s team is putting forth, internal inspections. I sat on a roundtable with, about some of these technologies and the questions were just boom. You couldn’t keep the hands down enough. So the new technologies bringing in asset management strategies, some of the supply chain stuff. It was, Allen Hall: To get that level of knowledge exchange, you would have to Travel to their sites. Like you would have to go to Latvia. It was a lot easier to go to Melbourne. And it’s nicer in the Joel Saxum: wintertime. Way better. The northern winter, northern hemisphere winter. I’d rather be here than Latvia right now. No offense to the Rowan’s team. Rosemary Barnes: The last session of the conference was really good too, because we had two international people who had come over and brought knowledge of solutions I didn’t know exist. Yeah. Kellenberger. Talking about precision machining up on a tower, while it’s swaying around they’re doing precision machining so you don’t have to, do component replacements. You can repair. We had, yeah, Jeremy how do you say his name? Hanks. Hanks. We had Jeremy Hanks who has similarly like amazing repairs for blades. But then we had two Australians, Katrina Swalwell and Christian Peake. Both of who have been working in the Australian wind industry since 2001, which is day one of Australian wind. So they’ve seen the whole thing happen. And I think that’s just like the, I don’t know, the conference in a nutshell. It’s that mix. It’s, like everyone that knows, The specifics of the Australian industry are specific problems. People from overseas who know, how the range of solutions available there, so we don’t have to travel there to see them. And I think it’s really important that it’s not just it’s not a flow of speakers to audience for, these are the solutions now, receive them. I think it’s as valuable for sponsors and any other company that’s there to hear the problems. Yeah, like a lot of us in the industry are engineers and that’s our favorite thing. It’s to know the right problem to solve. That’s how you get a really good product and, sales and profitability is much easier if you’re solving the right problems, I think. So I, yeah, I really think it’s that, Joel Saxum: that Rosemary Barnes: good Joel Saxum: mix. One other person that we had on stage that was on multiple panels and the guys literally in encyclopedias, David King from Golfwind technology. Rosemary Barnes: Yeah, he was good. Joel Saxum: You ask him a question and it was like he had rehearsed, no matter what the question was, What’d you have for lunch today, David? It was like he had rehearsed and had a perfect speech written for it. But I think the overwhelming wealth of knowledge, this back to your point, Alan, you said earlier about like, I didn’t realize we would run into as much knowledge as we did down here. I thought it was going to be a little bit more nascent of a market and the people that were on stage, Christian Peak from Mint Renewables and his, the strategies and the things you think all everybody up there, I was really surprised. So the, to be honest with you, Allen Hall: that’s not a negative. It just, we deal with the whole world, Rosemary. It’s a thing when we run across somebody that’s like super confident. And then we ran into a whole room full of super confident people. It’s wow, this is great. I love this place. Yeah. That’s why we’ll be back next year. Yeah. Allen Hall: And if anybody’s interested in being a sponsor next year or be a speaker, and I know there’s a lot of people that wanted to speak this year that couldn’t do it, so they need to start planning for it. I’m planning for next year right now. Rosemary Barnes: Yeah topic ideas for the round tables were we had these small breakout sessions where people got together to discuss a certain topic that they were all interested in. Those worked really well. We’ll do more of them next year. So more scope, tell us what you, where you, you want the ability to, yeah, get together in a small setting to discuss your problem in detail, then, suggest the topic. Allen Hall: And you need to get a hold of Phil to start that process. And Phil’s going to be the repository of all emails that come in. So if you send it to Rosemary, Rosemary’s going to send it to Phil. Phil Totaro: We can, everybody can just go back to windaustralia. com and we’ll update the website with those kind of submittal forms. So we’ll be capturing ideas and capturing speaker requests as soon as we can. Get the website updated. As soon as you get some sleep and get back on California time. Or at least more than three hours of sleep. Allen Hall: Well, Rosemary this whole conference started because you and I had a complaint session on, with microphones at the time. And then Matthew Stead heard it and said Why don’t you just run a conference? And my first response is are you insane, Matthew? Rosemary Barnes: The magic words, I’ve got some people that can help. Organize, we could do it. We Allen Hall: could do we totally do it. It’s Australia. People will pitch in and that is exactly what happened. So I appreciate your participation and your idea to kick this thing off because it’s been tremendously successful. It really has. I’ve Rosemary Barnes: been blown away. Yeah. I didn’t know we were capable of putting on such a high quality event. So lots of teething problems, like small little details that you can see why, like expert conference planners, they have learned a trick or two, but it’s not the part that people really care about. People will. We’ll tolerate a few little teething issues if the agenda is right, if the speakers are right, and I think that’s what we, that’s what we achieved. Allen Hall: Yeah, so thanks to everybody and good to see everybody in Australia, and I guess we’ll see everyone a year from now. And reach out, yeah, if you’re interested in participating in Wind Energy O& M Australia 2026, you better start now because that room was full. We’re going to have to expand this thing, but you want to get your tickets and get a hold of Phil and Rosemary and Go to windaustralia. com as soon as you can.…
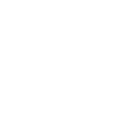
1 8-Tree waveCHECK Makes Blade Wrinkle Detection Simple 26:27
26:27
التشغيل لاحقا
التشغيل لاحقا
قوائم
إعجاب
احب26:27
In this Uptime Spotlight, Erik Klaas and Johannes Leib from 8-Tree discuss their waveCHECK system, which detects and measures surface defects on wind turbine blades. The system uses 3D optical scanning technology to identify wrinkles and other issues with high precision, helping improve quality control in blade manufacturing and maintenance. Fill out our Uptime listener survey and enter to win an Uptime mug! Sign up now for Uptime Tech News , our weekly email update on all things wind technology. This episode is sponsored by Weather Guard Lightning Tech . Learn more about Weather Guard’s StrikeTape Wind Turbine LPS retrofit. Follow the show on Facebook , YouTube , Twitter , Linkedin and visit Weather Guard on the web . And subscribe to Rosemary Barnes’ YouTube channel here . Have a question we can answer on the show? Email us! Allen Hall: Welcome to the Uptime Wind Energy Podcast Spotlight. I’m your host, Allen Hall, along with my co host, Joel Saxum. Today, we’re diving into revolutionary blade inspection technology from 8-Tree. 8-Tree’s WaveCheck system uses 3D optical scanning and augmented reality to detect and measure surface defects on wind turned blades with unprecedented precision. Joining us is Erik Klaas, the co founder and CTO of 8-Tree, and Johannes Leib, a program manager with 8-Tree, who brings over 15 years of wind blade industry experience, specializing in composites and fiber reinforced plastics. Joel Saxum: Welcome to Uptime Spotlight, shining light on wind energy’s brightest innovators. This is the Progress Powering Tomorrow. Allen Hall: Erik and Johannes, welcome to the show. Erik Klaas: We are glad to be on your podcast. Allen Hall: I’m excited to talk to both of you because I’ve seen your technology on YouTube quite a bit and now on LinkedIn and it’s quite impressive. And I want to start by asking really, how are you trying to handle wrinkles? It seems like wrinkles are a huge problem in the wind industry. They’re hard to detect and we’re getting escapes out of the factory. You want to discuss how big of an issue wrinkles are. And Blades is at the moment. Erik Klaas: Yeah, most likely this is a good topic for Johannes to speak about for one hour. But as I got into this business late, maybe I get to give you my perspective. So when I got into the wind business first, our legacy is in aerospace. So I saw a wrinkle and I never thought it could be such a problem or lead to catastrophic results. What is a wrinkle? I happen to have a separate part here. Which is a mock up that we did. We do this for testing our system. A wrinkle basically is a deviation in the glass fiber layup of a turbine blade. And it’s very small, so you can’t even almost not see it. But it can lead to the blade cracking in these particular areas where the wrinkle happens. And therefore, the inspector’s task is to measure how wide and how high is a wrinkle. And so the ratio between width and height is what they then calculate, and there’s a limit to that ratio. And that is what an inspector has to do. And currently, they are doing it with hand tools. And a hand tool is a Dial gauge or it can be what they call a comp gauge. So they push it on the surface so they get the contour of this wrinkle and then with that contour they measure actually the width and the height of it. Allen Hall: It can be very difficult to detect some of these wrinkles because the laminates in these longer blades, the laminate is very thick. So if you have a wrinkle somewhere in the middle of this laminate, the surface Defect or the surface curvature change is minuscule, right? Erik Klaas: It is. And there is a limitation of our technology that I need to speak about. So we can only detect and measure those which are on the top layer. So if they go through the whole layup of layers and they are visible on the surface, we can measure them. And if they only appear in deeper layers, we can’t. So you need like NDT measures, methods that go to deeper layers to inspect those. But most often also the layer the wrinkles in deeper layers are visible than on the top surface. Joel Saxum: So you need that physical deviation on the top. If you ran your hand over it, you’d be able to feel it. And that’s what you guys need to be able to have to sense it. Okay. Erik Klaas: Yes. What we are doing Joel Saxum: so our Erik Klaas: measurement technology is a surface inspection technology. So it always measures deviations on the surface. Correct. Allen Hall: So as part of blade inspections, ideally those wrinkles are getting measured for length and width and all of them in which there can be a number of them on any blade because wrinkles are not uncommon. It’s the question of, are they serious enough to be repaired? I think the question then becomes how sensitive is your equipment to do this? Because we seem to have a lot of blades out in service that do have wrinkles. I’ve seen them. Yeah. Over the summertime, I saw a number of them. It’s hard sometimes to detect the wrinkles. It is not necessarily obvious to an inspector that the wrinkle that exit may exist there or how critical that is, but the sensitivity of your equipment is quite impressive. You want to describe how sensitive it is to small perturbations on the surface? Erik Klaas: Yeah. So what we use, the technology is, it’s called structured light scanning and how it works. It projects a pattern on the surface and from a different angles. Those patterns are observed from a camera, a digital camera, and as there’s an angle in between, so when the surface changes, also the shape of these patterns changes, and that’s how is, how we get access to the third dimension in these measurements. And so what’s good for us, that technology has developed over the last 20 years quite significantly and it’s not a to go into the micron level of detail. surface deviations. And I mentioned, so our background is aviation industry. So we, with the same technology, we measured dents and bumps on the outer skin of aircrafts. And so there are our measurement uncertainties in the magnitude of 50 microns, or those People that prefer inches, so that is two thousandths of an inch yeah, 50 microns. Accuracy in the wind power industry, or on surfaces like glass laminates, is a bit worse. Because the surfaces are difficult to measure. They are a bit transparent, they are a bit rough. Yeah, it’s, in the best case, 50 micron. Joel Saxum: Yeah, I think anybody that’s been inside of a blade can attest to at least one defect in every blade, right? If you’re in there looking around, you see something, whether it’s a, extra glue here, or some dry glass here, or a little bit of D lam here, and it, one of the difficult things from, from an untrained eye, I’ve been in a lot of them supporting people. is knowing what’s actually an issue, right? Because you’d look and be like, oh, is that a problem? Is that going to affect structural integrity? Maybe not. Maybe this one will. And that takes expertise. But what you guys have created is a tool to help these experts. And so what I want to talk about is then, The ability to scan, cause a lot of times we’re talking inside of the blade, right? Cause we’re looking, cause the outsides gel coat, it’s all cleaned up. Everything looks pretty. So everything’s been sanded and smooth. But if you’re inside the blade to get that 50 micron accuracy, Okay. So in my mind, I’m always thinking geometry, there has to be a certain distance to be able to look at that angle. How big is this tool? So how far can these experts get in the blade with it to be able to look at things? Erik Klaas: Yeah, good question. And so of course also the tool has evolved over time. So in the background we see actually two versions. There’s one over there. I hope that’s visible in the image. So that tool has a standoff of about 50 centimeters. The weight is about four kilograms, four and a half kilograms. It’s all self contained. So it’s battery powered, so there’s not an additional computer. It’s all within that unit. And. Yeah, you can go pretty far into a blade to use it until your space is limited to this about maybe 70 centimeters. So that’s the space you need in front of the surface. Joel Saxum: And anything I mean, 70 centimeters is, so if you’re getting down to basically, with someone operating at like a meter of a chamber or so, most all of the defects that need to be dealt with are going to be from there back towards the root anyways. Because that’s going to be the high structural loading zone. That’s where, if you’re going to develop a crack or something, those are the ones that you really need to see. Can you tell us about some use cases in the field or where this thing’s being used right now? Erik Klaas: So yeah, we mentioned wrinkle measurements and wrinkles in and maybe that’s a better question for Johannes to answer because how blades are made, I think is that there’s different opportunities and as these butterfly blades, where they make them out of two shells. And glue them together afterwards. There it’s not a problem to access the entire inside of the blade. So to the very tip of the blade. But what are the other technologies, Johannes, that used to make Johannes Georg Leib: Currently, our tool is mainly used in the manufacturing because that’s where we started developing it with some of the big global blade manufacturers. But we are also looking into applications in the field because the, yeah. The functionality of the tool is just the same in the field as it would be in the factory. In the factory, we are now also going towards automatization. That it’s not a handheld tool anymore, but we’re doing some research on having it automated on either a robot or yeah. a portal stuff. Basically the technology works everywhere because it’s independent from any infrastructure, you can take it anywhere. It’s a, it’s very portable. It’s battery powered. You don’t need a a power Allen Hall: supply. So the wave check system has changed or morphed over time to become more compact, more powerful. The first generation I remember seeing. The sensor was maybe, I’m going to speak in feet here, but it may be two feet, two thirds of a meter away from the surface. I saw it in aerospace quite a bit. And it was, it’s fairly far away, but now it’s getting more compact and is still all battery powered. So really it, it doesn’t take anything to hold it up against the surface and take an image. Exactly. So that’s the Erik Klaas: first unit’s design and then we took all the user feedback that we got from the first five, six years of A Tree being in existence. And we came up with this design, which looks quite a bit different, but, The measurement engine and the technology is still the same. So we’re using a projector on this side where the light comes out. We’re using a camera on this side. We are having a battery now in the bottom, which makes a bit more ergonomic handling possible. It’s more like a power tool, where you have your battery in the handle or below the handle. So that makes a nicer central center of gravity. And the handling is just easier. And yeah, it lost like one kilogram in weight. I see a lot of carbon fiber there. Yeah. And there’s carbon fiber in the handles and in the housing and on top is a display, so that makes it a bit easier to adjust for different settings. So you can change tolerances for your wrinkles or you can change also what we take into account is the fiber direction. So usually we are measuring perpendicular to the fiber direction, but there’s requirements sometimes also for the other direction. So things like this can be set with the help of this touch display. Joel Saxum: So how do you actually collect data with it? Is it taking a snapshot? Is it taking a video? Is it giving you a 3d map? What does that look like? It’s all of the above, but Erik Klaas: the main feature is a 3d map. Not sure whether that’s visible in the video, but I push the trigger here on the handle now and you see a blue flickering light being projected on the surface. And that’s taken in a tenth of a second and about two, three, four seconds later, we get the result. And the result is a 3D map, about 2. 4 million points, 3D data points on the surface. And what’s unique about the system, it projects those results on the surface. So you don’t have a computer attached where you see the result on the display of the computer, but everything is visible on the screen. On the surface where the defect actually happens. Joel Saxum: Yeah. You got a two man team there. Like one guy can run the gun. One’s got a pen. You can mark it out perfectly, exactly in real time, what you’re seeing for that anomaly on the blade, if it’s a wrinkle Erik Klaas: and on top of that, the Joel Saxum: results are Erik Klaas: stored on the device. So there’s a relatively large hard disk. So you can save 10 thousands of those measurements on the hard drive, just like a photo. Allen Hall: I just want to get to the use piece. Cause I think people want to understand how this actually works. Erik, I take your device, I push it against the blade, I press a trigger, it takes a photo, it processes it, and then it re displays the changes in the surface. on the blade itself. So you see color changes right on the surface, which you then can just take a pen and highlight. And it stores that data on the unit, but also stores it in the cloud, right? So not only do you have a record right in front of you, this is what that defect looks like in a wrinkle, but everybody back in the office, all the engineers and the quality department have an instant record of what this thing looks like. Is from your unit. So there’s, it’s very quick and precise, which is the problem with blade checks today is that they’re slow, cumbersome and inexact, and you fix all of that with one tool. Erik Klaas: Yeah. That’s a very nice summary. Thanks for that, Helen. And on top of that, so we also now in the process of making interfaces to quality systems, because we know we are not the end of the game. The results that we are delivering need to go somewhere. And now we try to make that even more seamless by defining APIs that then connect to a quality management system or an ERP system so that these results are filed away. Ideally, they travel then with a blade to the customer. So the customer has a digital twin of that blade and he can look up, okay, there was a wrinkle in production, but it was below the limits. And Allen Hall: some of the best blade manufacturers in the world are using your technology now in the factory. You want to describe that? Who’s using it? We developed this Johannes Georg Leib: with input, even before I, as the blade expert in EITRI joined. We developed this together with LM Windpower and they were actually also the first first users of this. But nowadays some other of the global blade makers such as TPI have also implemented it in the, during the last year, yeah. And yeah, we see that they have a lot of yeah, making a lot of progress in this let’s say digital evaluation of defects, which yeah, which is really driving quality assurance of blades, a big leap forward from our point of view. I’ve been working in blade manufacturing as well as in certification, and I remember the times when there were big fat file folders with paper yeah, tons of paper per blade. And if you wanted to look up something then it was not properly filled in and so on. It was not traceable at all. If you wanted to look up something in the aftermath, you just had no chance because yeah. And nowadays, you would have like a. Exact representations, 3D representation of certain defects, which you could easily retrieve 10 years later and and check, what was going on there. For example, if a blade breaks you could really have accurate records and check if there was something or not. And that’s something that is not yet appreciated enough. from our point of view, from the industry, because they want to avoid any cost. Yeah. As we all know in blade manufacturing, cost is still a big topic while quality is, yeah, more on a second or third position. And we think it’s time for changing this by by applying, let’s say 21st century technology to blade inspection, because let’s say the tools that were used when I entered this This industry in 2008? Yeah. These were actually the tools that were already used or that you could have already have been used a hundred years ago, I would say. Yeah. So we had no involvement in, in, in such inspection tools over a hundred years. And we think now, with all these AI stuff, the time should have come for doing something. In a new and in a different way. And that’s what we are striving for and working on. Joel Saxum: I think that the basis of that is what you guys are delivering. It’s data, it’s structured data. If blade manufacturers want to get better at what they’re doing. The one thing is in, in, at the end of the day, Inspections in the factory are basically reactive in my opinion, right? They’re done. We look at it right now. Okay, now we might have to do a repair because I know a lot of these blade manufacturers have on site repair teams to prepare stuff before the blades leave because it’s a controlled environment and all that. But there is times when a lot of these blades make it out to the field and then all of a sudden, oh no, we have to do this big repair out in the field. But the idea behind collecting structured data that can be cataloged, reviewed, and once you get. enough of this stuff amalgamated, you can start running some algorithms on it. You can start running a little AI. You can start doing some analysis to see where the manufacturing process might get better in the future. That’s a big thing for me is if you’re collecting all this data, that’s fantastic. We can fix problems right now. But if you get some smart people behind taking that data and using it for the next next edition, next iteration, next legacy of blades and how we may adjust manufacturing things. If we keep seeing the same wrinkle of the same size in the same kind of space because you guys have collected or your tools have collected the data to show that, now we can get to the point where let’s put a manufacturing fix in. Let’s get to the manufacturing engineers and see if they can’t design something to solve this issue in the future and that makes That’s better for the whole wind industry, that’s what we want. We want blades that come out of the factory that are good to go, that we don’t have to worry about in the future. Thank you guys for creating this tool for that. Yeah, that brings me to Johannes Georg Leib: one point I want to mention because right now our tool is mostly used when the blade has already been produced and there is a need for repair often then if you detect something, but what we are also investigating together with some partners is to apply it even before the The problem happens. Yeah. So for example, during the layup, we do scans of the layup. And then, the workers are told online during the manufacturing process, Hey, this layer is maybe 10 centimeters too far away from the correct position. Please move it even before the blade is being infused. And that’s let’s say the next generation we are working on where the tool is not anymore used handheld by an inspector who just evaluates things that have already happened, but use it, let’s say proactively Beforehand, the stuff even happens and in an automated environment, where you have a lot of different sensors, like cameras but also our 3d scanner that then creates information that avoids the mistakes already during, in the course of the manufacturing process. And that’s another initiative that we’re doing yeah, and that might also be interested in, maybe it will take another 3 to 5 years until it’s ready for market. But it’s, I think it’s good to know that there are some people also working on such things. Allen Hall: Erik, it can’t take three to five years. We need this in about six months. So you got to get to work. Erik Klaas: Yeah. The good news is, yeah, I see a lot of parallels between the wind power industry and the aerospace industry, for example. So in the early days, when we founded A3, like in 2012, We went to a rigorous process of running so called gauge R& R testing. So because our customers wanted to know, how do you make sure one tenth of a millimeter is one tenth of a millimeter or one thou is one thou? And so we learned it the hard way that we needed to test and test. And we ran like thousands of such gauge R& R tests. And now, when we started with LM Windpower, we did that again. So people wanted to trust us that when we say, okay, this wrinkle is within or without limits, that we are really on the right side of that decision. And how can you make sure? And then we found out that there is actually an ISO 17025, which guarantees your measurements are traceable to national standards and you can trust us. And so in the course of this development, and that took a long time, and now I’m back to that question, why does, do things take so long? We had to run with Johannes help, we got our calibration accredited by German lab so that they say, okay, you can trust these guys. And now we have that stamp of approval, which is called ISO 17025. And that helps a lot now because in industrial processes, they want to know, okay, how do they make sure they measure what they measure is correct. Allen Hall: Absolutely. ISO 17025 is the world standard for calibration. And if you can show that your tool. matches those requirements, it’s a really good tool and it’s used all over aerospace when that happens. So the accuracy has to be there when you’re dealing with aircraft in particular because of the, there’s a lot of people inside of there. So those systems that are developed from aerospace now directly. Correlate over to the wind industry. So it’s tremendous to have that level of calibration. Now, I want to expand this out a little bit because there’s a lot of old blades in service, hundreds of thousands of blades in service that didn’t use your technology in the factory. And. I want to understand, is there a use case for this for independent service providers to go in and to look for places where wrinkles could occur? Back to Joel’s earlier statement, around the root area where the loading is so great and where cracks start to develop. Can you take this existing tool off the shelf and start looking at existing blades and documenting where wrinkles may exist? Erik Klaas: Yeah, we absolutely think you can and we start to talk to the first companies that do that sort of inspection. And of course, that’s a different story because getting up tower, getting into the plate is a different story. It’s more work and it’s also more time consuming and it requires smaller tools. And that’s why we did the second generation. So that also helps to to enable this inspection up tower. And but we are in the early stages. Joel Saxum: Yeah. The looks of it, it looks like the second generation can fit through a root closure panel and to get into a blade a lot easier than the first version. Yeah. So for that Erik Klaas: exact reason, we can fold this frame together. We can remove that handle so that you can put this in a backpack when you go up tower. So it’s just more compact for that purpose. Allen Hall: It looks like the system is ready to go for inspections out in the field, which is tremendous. So if you’re an independent service provider or a quality organization or an NDT organization, And you want to learn more about WaveCheck and all the great things that are happening at 8-Tree. How do they get a hold of you, Erik? How do they contact your company? Erik Klaas: Very simple. Send an email to info at 8-Tree. We have for wind power applications, a dedicated LinkedIn page. Go up there or go to our webpage, 8-Tree. com. Eight with a hyphen tree. com. And yeah, we are happy to explore what’s next. Allen Hall: And the website is the number eight dash tree, T R E E. com. Erik and Johannes. It’s wonderful to have you in the program. I’ve learned a tremendous amount. Your technology is very exciting. So congratulations on all the breakthroughs that you have. And yeah, we love to have you on the program again as you get further out into the field. We’d like to learn how that’s going. So you’re invited back. Thank you for joining us today. Thank you for having us. Erik Klaas: Really enjoyed Allen Hall: it. Yeah, it was fun. Thanks.…
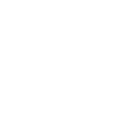
1 Siemens Gamesa De-Icing, Vestas Permanent Tower Crane 8:14
8:14
التشغيل لاحقا
التشغيل لاحقا
قوائم
إعجاب
احب8:14
We discuss Siemens Gamesa's advanced blade de-icing system, their blade root repair fix, and a tower designed by Vestas with its own permanent crane system. Fill out our Uptime listener survey and enter to win an Uptime mug! Sign up now for Uptime Tech News, our weekly email update on all things wind technology. This episode is sponsored by Weather Guard Lightning Tech. Learn more about Weather Guard's StrikeTape Wind Turbine LPS retrofit. Follow the show on Facebook, YouTube, Twitter, Linkedin and visit Weather Guard on the web. And subscribe to Rosemary Barnes' YouTube channel here. Have a question we can answer on the show? Email us! Phil Totaro: This is Power Up, where groundbreaking wind energy ideas become your clean energy future. Here's your hosts, Allen Hall and Phil Totaro. Allen Hall: We have really interesting patents this week, Phil, including this first one from Siemens Gamesa, and it is a wind turbine blade with an advanced de icing system. Now, you say to yourself, well, there's been a lot of de icing systems on wind turbine blades. In fact, Rosie has worked on a number of them for LM. But this one's a little bit different. So it It uses a kind of a matrix setup of thermal heating areas arranged in sort of series and parallel connections, and it creates overlapping heating zones that can be very precisely controlled. Now that is very beneficial because a lot of times you More temperature, more heat towards the tip than you do at the root. So you would like the temperature to be graded up towards the tip. It's kind of hard to do a lot of times. But in this situation, you can adapt it to the situation. And this seems smart, but I haven't seen it implemented. And I know Siemens Gamesa owners. Like the icing system. So maybe this is coming out in the near future, Phil. Phil Totaro: Yeah, this would be interesting because this is very different than your conventional like blown air solution, like Enercon and other companies use. Where you could have a scenario where you've got like hotspots and, and heat concentrations at different points along the blades, particularly where you have ribs or bulkheads or something that would kind of get in the way of the airflow. a thermal heating mat with again, different zones where you can kind of trigger, on off to, to try and either prevent ice accretion or actually provide deicing for the blade. So it's, it's a really interesting approach in that it gives you more granular control over where you want to be able to, to de ice and again, based on ice thickness, and you can, monitor your Phil Totaro: performance, or you might have a more sophisticated system that actually monitors how much ice is still stuck on the blade. So. The, the implementation of this I think would be welcome. And it's probably something that, I mean, heating mats are almost inevitably, they do introduce a certain amount of challenges, especially with lightning interactions. But generally speaking, they are a good way for wind turbine blades to to be de iced. So hopefully this does make its way into more commercially available products in the future. Allen Hall: Well, it looks like it will save somewhere between 20 and 50 percent of energy consumption to, to heat the blade. That would be remarkable if you could make a, even a 10 percent change in the amount of power required to heat the blade up. Going to 50 percent would be astounding. And that makes me think you're going to see this, this patent idea Phil Totaro: show up pretty soon. I mean, to be blunt, like, and I'll do respect to Enercon that pioneered a lot of this technology, but volumetric heating is just wildly inefficient, so it's like, something that's a more, cost efficient and thermally efficient solution is probably desirable. Allen Hall: Our next patent is from Vestas and this. Seems like a relatively simple idea, but it evidently isn't because they were able to patent it. So,…
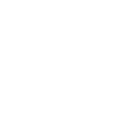
1 Ørsted CEO Change, Shell Leaves Atlantic Shores 27:22
27:22
التشغيل لاحقا
التشغيل لاحقا
قوائم
إعجاب
احب27:22
This week on Uptime, we discuss Ørsted CEO Mads Nipper stepping down, Shell withdrawing from the Atlantic Shores offshore wind project, and a study showing only 15% of employees feel their managers are transparent about challenges in the workplace. Fill out our Uptime listener survey and enter to win an Uptime mug! Sign up now for Uptime Tech News, our weekly email update on all things wind technology. This episode is sponsored by Weather Guard Lightning Tech. Learn more about Weather Guard's StrikeTape Wind Turbine LPS retrofit. Follow the show on Facebook, YouTube, Twitter, Linkedin and visit Weather Guard on the web. And subscribe to Rosemary Barnes' YouTube channel here. Have a question we can answer on the show? Email us! You're listening to the Uptime Wind Energy Podcast, brought to you by BuildTurbines. com. Learn, train, and be a part of the clean energy revolution. Visit BuildTurbines. com today. Now here's your hosts, Allen Hall, Joel Saxom, Phil Totaro, and Rosemary Barnes. Allen Hall: Danish Renewable Energy Company, Ørsted, announced a leadership change, with CEO Mad Snipper stepping down after four years at the helm. Rasmus Erbo. Uh, the company's deputy CEO and chief commercial officer will take over as group president and CEO, uh, in February. Uh, the transition comes as Orsted adapts to evolving market conditions in the offshore wind sector. Now this, uh, I guess around the industry was expected news. Uh, if you had talked to somebody, uh, about offshore in the US, uh, they felt like what had happened over the last year or so was really rough on the leadership at Oersted, part of this too, guys, is that some of it is just happenstance, interest rates rising, the supply chain nightmares that were happening and Mads Knipper would just happen to be there at that specific time. Is, is that the feeling like it was just bad timing, uh, for Mads? Phil Totaro: Yeah, it's, it's part of it, but the, the reality I think is you, you've got a scenario where he, he was there and the buck stops here and all that sort of stuff, um, if you're the boss, but he also was one kind of overseeing a lot of the deals that got him put in place that led to all those impairments that they ended up having. It's like, yeah, okay. Interest rates are high, but. It's like he, he, you know, was there signing off on these, these deals with, uh, PSEG in New Jersey and, uh, Eversource in, in Connecticut, uh, and Rhode Island that were just frankly terrible deals. I mean, it just, they, they ended up, Orsted ended up having to pay. for whatever the utility companies had invested time and money and effort and et cetera, uh, into, you know, the development work on these deals, um, in case they decided to pull out plus, you know, uh, a little extra. And it's like, that's, that's the way it is. You know, you might think that that's typical, but when you get into a deal like this for an offshore wind farm, uh, I mean, we're starting to talk in the hundreds of millions of dollars, and it led to this, this multi billion dollar impairment that they had, you know, last year. So, you know, I think I said on the show six months ago that he was likely to be gone, and guess what? He is. Allen Hall: My feeling about it is there's just a little bit of happenstance, but that's the problem at being in leadership You don't get to choose the economic times in which you're running the company and you have to play what the cards are dealt right, I Wouldn't say any offshore wind developer in the United States. This has great numbers at the minute So it isn't like Orsted has is in a different bucket at the minute it but I I I think the, my contention at the time was New Jersey really screwed Orsted. Not the, the government in New Jersey was just negotiating in bad faith. And they wanted to take all the federal tax credits, which Orsted agreed to, and then they needed them back. And then it just went back and forth there.…
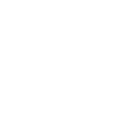
1 Shell 2024 Financial Results, Mitsubishi Reviews Offshore Projects 6:01
6:01
التشغيل لاحقا
التشغيل لاحقا
قوائم
إعجاب
احب6:01
On News Flash, Allen and Phil discuss Caverion's acquisition of Huolto-Lepistö, Mitsubishi re-evaluating their offshore wind assets and Shell's 2024 financial report. Fill out our Uptime listener survey and enter to win an Uptime mug! Register for Wind Energy O&M Australia! https://www.windaustralia.com Sign up now for Uptime Tech News, our weekly email update on all things wind technology. This episode is sponsored by Weather Guard Lightning Tech. Learn more about Weather Guard's StrikeTape Wind Turbine LPS retrofit. Follow the show on Facebook, YouTube, Twitter, Linkedin and visit Weather Guard on the web. And subscribe to Rosemary Barnes' YouTube channel here. Have a question we can answer on the show? Email us! Welcome to Uptime News Flash. Industry news lightning fast. Your hosts, Allen Hall, Joel Saxum, and Phil Totaro discuss the latest deals, mergers, and alliances that will shape the future of wind power. News Flash is brought to you by IntelStor. For market intelligence that generates revenue, visit www.intelstor.com. Allen Hall: Well Phil, a busy week in mergers and acquisitions. Caverion has acquired Huolto-Lepistö’s, a wind turbine maintenance business. Now this acquisition gives Caverion a new base on Finland's west coast. And the acquired business specializes in wind turbine service lifts. Repairs, inspections, and maintenance. There does seem to be a lot more activity in Finland Phil Totaro: for wind. Yeah. And, and as their installed base grows they have a lot of large turbines up there in, in Finland. So I think the average, if I remember correctly based on our data and Intel store, the average turbine size in Finland these days is Something like. 5. 5 megawatts and upwards of like 140 something meter rotor. Again, taking the entire installed base in, into account. So, growing installed base, big turbines, big responsibility, and. Admittedly, I don't know very much about Kaverian as a company, but looking into it after this deal was announced earlier this week it's, it's very interesting how they're trying to position themselves. And the fact that they want to go after the, the wind services market also demonstrates, I think that they're making a commitment to a segment that they see a lot more growth potential with. Allen Hall: Over in Japan, Mitsubishi Corporation is reviewing its offshore wind projects due to significant changes in the business environment. Now, the company leads consortia that won three projects in Japan's first state run offshore wind auction in 2021, and those projects total about 1. 7 gigawatts of capacity. Capacity. The partner company, Chubu Electric, posted an 18 billion yen loss on these projects. It looks like Mitsubishi is trying to reevaluate the profit margin on these projects, and with the high inflation in Japan and maybe even stagnation being discussed, it's going to get a little rough for Mitsubishi. I wonder if they're going to finish these projects. Phil Totaro: Yeah, well, it's funny because Japan was a market with their offshore wind potential that looked, poised to take off. They heavily invested in floating offshore wind demonstrator projects, more than a decade ago. They have a finite amount of, of space on land, obviously, where, They can install onshore wind and solar for that matter. So the exploitation of offshore wind looked like a really promising segment to the market. But they've never been able to get their act together. And I mean, this is frankly a very common thing amongst a lot of governments that, that have a lot of offshore wind potential, resource potential. But they don't have the right structure in place. And you could say the same thing about South Korea. You can say the same thing about Brazil. That they, they've got a tremendous amount of interest and enthusiasm. And frankly, people that want to invest money there, including Mitsubishi, but if they don't get a sense of like how they're going to see a...…
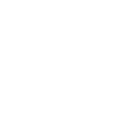
1 Vårgrønn’s Massive UK Offshore Floating Wind Project 24:19
24:19
التشغيل لاحقا
التشغيل لاحقا
قوائم
إعجاب
احب24:19
In the Uptime Spotlight today is Stephen Bull, CEO of Vårgrønn, the company building the world's largest offshore wind farm with a government contract: Green Volt. Stephen discusses the massive project's progress, planning, and logistics to be completed by 2030. Fill out our Uptime listener survey and enter to win an Uptime mug! Register for Wind Energy O&M Australia! https://www.windaustralia.com Sign up now for Uptime Tech News, our weekly email update on all things wind technology. This episode is sponsored by Weather Guard Lightning Tech. Learn more about Weather Guard's StrikeTape Wind Turbine LPS retrofit. Follow the show on Facebook, YouTube, Twitter, Linkedin and visit Weather Guard on the web. And subscribe to Rosemary Barnes' YouTube channel here. Have a question we can answer on the show? Email us! Allen Hall: Welcome to the Uptime Wind Energy Podcast Spotlight. I'm your host, Allen Hall, along with my co host, Joel Saxum today, I'm excited to welcome Stephen Bull, CEO of Vårgrønn, who is leading the charge in developing some of Europe's most ambitious floating offshore wind projects. Stephen brings over 25 years of energy industry experience and currently oversees Vårgrønn's Impressive portfolio of projects across Northern Europe, including Greenvolt, set to become the world's largest floating offshore wind farm with a government contract. Welcome to Uptime Spotlight, shining light on wind energy's brightest innovators. This is the progress powering tomorrow. Allen Hall: Steven, welcome to the show. Thanks so much, great to be here. Well, the Greenvolt project is one of the most important Impressive projects going on in the world right now, and you're heavily involved with that, of course, as being the CEO of Vårgrønn and I want to understand a little bit about how that project came together and what problem Greenvolt is trying to solve. Stephen Bull: Yeah, sure. I mean, it's kind of neat to say it's the most exciting project. I think it's, uh, it's quite a scary project in many respects for us as well when you work within the offshore wind sector at the moment, but definitely within floating offshore wind. Yeah. If we sort of dial it back down to the project itself, I mean, what we're solving for here is, is the generic problem with offshore wind in deeper waters. And, uh, and really when you start to push the boundaries beyond 60, you know, 60 odd plus, 70 meter water depths, you need to start to go into the floating territory. Um, and that's something that you find distinctly within the coast of Scotland as well. There's only so much of that seabed that is shallow and then it starts to push out there. So, Scottish authorities, the Scottish Crown Estate, the guys who basically own the seabed license around there, want to have further developments within offshore wind, but um, they are inhibited in the sense that they have deeper waters. Um, at the same time, there's still a quite large oil and gas industry in, of Scottish waters as there is in Norway, as well as the two largest producers in Europe. They also have carbon issues, carbon problems of CO2 emissions from their own Scope 1 emissions. So the Scottish authorities have put together a concept which is called targeted oil and gas. And essentially they've been looking to lease out areas where we could develop offshore wind, both that go straight into the grid. For the benefit of consumers, but also could help decarbonize oil and gas operations as well. So that's the background around it. It's happened pretty quickly. To be honest, we, we received our, uh, you know, essentially our lease just over a year ago, year and a half ago. Uh, we won a contract for difference from the UK government in September. Uh, for 400 megawatts and we're just basically right in the middle of procurement and developing the whole concept now so we could be online by 2030. Allen Hall: Wow, that's a really short timeline.…
This week we discuss cooling system patents, including Siemens Gamesa's method for creating air channels for better temperature control, Goldwind's predictive temperature moderating, and GE's adjustable power output based on component temperatures. Fill out our Uptime listener survey and enter to win an Uptime mug! Register for Wind Energy O&M Australia! https://www.windaustralia.com Sign up now for Uptime Tech News, our weekly email update on all things wind technology. This episode is sponsored by Weather Guard Lightning Tech. Learn more about Weather Guard's StrikeTape Wind Turbine LPS retrofit. Follow the show on Facebook, YouTube, Twitter, Linkedin and visit Weather Guard on the web. And subscribe to Rosemary Barnes' YouTube channel here. Have a question we can answer on the show? Email us! This is Power Up, where groundbreaking wind energy ideas become your clean energy future. Here's your hosts, Allen Hall and Phil Totaro. Allen Hall: Phil, this episode of Power Up is going to focus on cooling. And as wind turbines get bigger and bigger, thermal controls are becoming more important. You need to make sure that there's no thermal runaways, and with the amount of power. 8, 10, 12, 15 megawatts going on inside of some of these nacelles. You're seeing a lot of patents and innovation around cooling, and this first one is from Siemens Gamesa, and it has to do with the generator itself. And the patent describes a cooling system for the generator that places air channels to better control temperature. Within the generator. Now, the key feature includes the magnet elements arranged in rows with groove like recesses that allow for targeted airflow between the components. Now, that design creates multiple cooling paths with gaps somewhere between like a half a millimeter and ten millimeters wide that enable better heat dissipation. So, obviously Siemens Gamesa sees the future, which is thermal control in a generator, because if you have overheating in generators That can be quite expensive to fix, so they're trying to address it up front, Phil, with this basically airflow pattern. Phil Totaro: Yeah, and, and as you mentioned, not only are generators getting bigger but particularly for offshore, the operational efficiency matters a lot. and how you control both the flux density and efficiency of the generator, balanced against how you have to cool the thing to maintain the kind of an air gap that you need in order to get the efficiency you want. It, it just throws these thermal engineers into complete chaos most of the time. So the way that they're architecting this is so that you can control the airflow in those channels in between the, the magnet holders to prevent hotspots. For the long term, if it keeps happening and you keep getting the hotspot, it can actually cause thermal degradation in the magnets and in The, the generator structure itself. So again, in order to maintain kind of peak operational efficiency, cooling becomes a a critical component to that. Allen Hall: Our second patent is from Goldwind and it is also focused on cooling up and then the cell. And it. Is an idea that is wrapped around really a sophisticated coolings control system that uses predictive temperature monitoring to optimize cooling. And as you can well imagine, as these generators get bigger, there's just a lot of nooks and crannies and you need to be able to monitor the hole in the cell area for temperature increases and to control it. Well, this system connects a cooling device and a yaw controller to a frequency converter that controls the operation based on the predictive temperature. Temperature thresholds. Now the key innovation is ability to anticipate when cooling will be needed and by calculating future temperature profiles and allowing a more proactive reaction to that temperature control. So they're, they're using a lot more information to predict where the temperatures will be and from what it...…
مرحبًا بك في مشغل أف ام!
يقوم برنامج مشغل أف أم بمسح الويب للحصول على بودكاست عالية الجودة لتستمتع بها الآن. إنه أفضل تطبيق بودكاست ويعمل على أجهزة اندرويد والأيفون والويب. قم بالتسجيل لمزامنة الاشتراكات عبر الأجهزة.